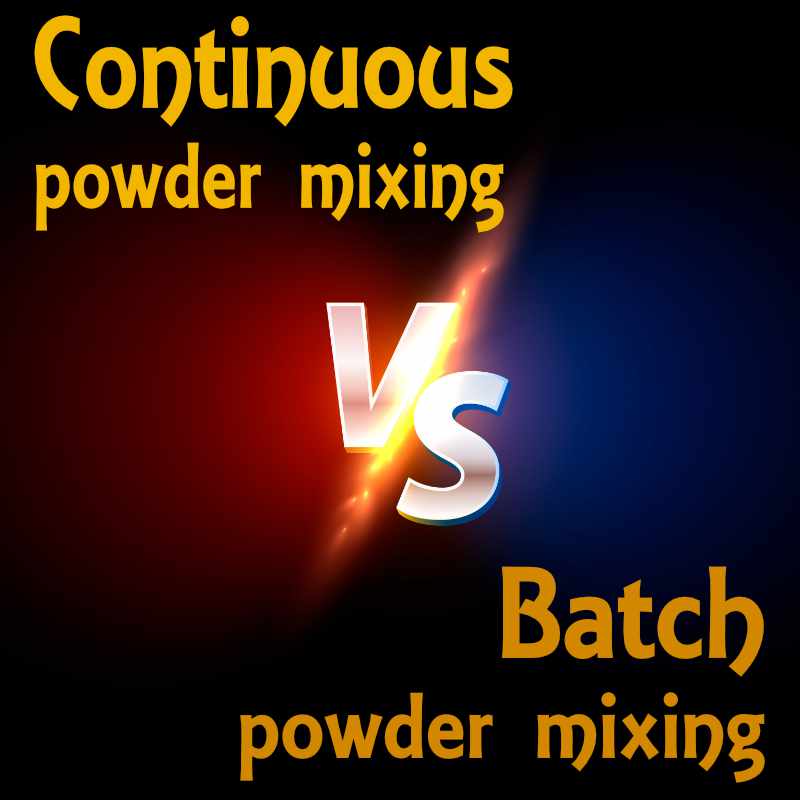
Mezcla continua frente a mezcla por lotes
La mezcla de polvos y los procesos complementarios como la humidificación, la desagregación, la aglomeración, el calentamiento, el secado, el enfriamiento, la gasificación, el aglutinado y... pueden realizarse de forma discontinua o continua.
Sin embargo, también existen criterios de exclusión. Ciertos procesos de mezcla solo pueden llevarse a cabo con uno de los dos métodos de mezcla. Esta entrada del blog trata de las ventajas y desventajas de ambos métodos de mezcla.
Los mezcladoresamixon® se utilizan tanto para procesos de mezcla por lotes como para procesos de mezcla continua. Ambos procesos de mezcla cumplen los requisitos de los operadores:
- alta calidad de mezcla y reproducibilidad segura
- alta flexibilidad al cambiar de receta
- proceso de mezcla robusto, la alta calidad de mezcla se logra incluso con una consistencia variable del material a granel
- un buen vaciado de los restos protege contra la contaminación
- buena accesibilidad
- buena capacidad de limpieza que ahorra tiempo y costes
- se cumplen los más altos requisitos de higiene
- la construcción robusta y duradera de la máquina garantiza unos costes de mantenimiento mínimos y
- una larga vida útil
Clasificación general
Si comparamos el número de mezcladoras de funcionamiento continuo con el número de mezcladoras discontinuas en todos los sectores, se obtiene un resultado interesante: hay muchas más mezcladoras discontinuas que mezcladoras de funcionamiento continuo. La gama global de tipos de mezcladoras también está dominada por las mezcladoras discontinuas.
En general, se prefiere la mezcla continua para la fabricación de productos en masa. Sin embargo, si se van a mezclar muchos componentes, se prefiere la mezcladora por lotes. También se prefiere una mezcladora por lotes si los requisitos de calidad de la mezcla son muy elevados.
Una mezcladora discontinua es relativamente fácil de manejar. En la práctica, ofrece mucha más flexibilidad. Esta es otra de las razones por las que los sistemas de mezcla por lotes son mucho más comunes.

Comparación
- En el mezclador por lotes (izquierda), el proceso se realiza por lotes. La herramienta de mezcla no empieza a girar hasta que se han introducido los componentes individuales. Mediante la dispersión tridimensional de los productos, el mezclador modifica la posición de todas las partículas entre sí. El estado cambia de «sin mezclar» a «mezcla técnicamente ideal». Solo entonces se produce el vaciado.
- En el caso de la mezcla continua (derecha), los componentes se introducen en el mezclador de forma continua en la proporción correcta. Los flujos de material se homogeneizan en el mezclador y el producto mezclado se descarga de forma continua. La diferencia de concentración es menor en este caso porque el llamado flujo continuo en caldera ya ha creado una base de mezcla homogénea. Los flujos de material introducidos son comparativamente pequeños en relación con el contenido del recipiente ya homogeneizado. El tiempo medio de permanencia puede ser, por ejemplo, de 0,5 a 3 minutos.
Cabe señalar que hay dos tipos de mezclado continuo de polvos: el flujo tubular y el flujo de caldera.
El tiempo de permanencia en la mezcladora continua
La distribución del tiempo de residencia de los materiales mezclados en una mezcladora continua puede describirse mediante una función de distribución normal gaussiana. La distribución normal suele utilizarse cuando los tiempos de residencia se distribuyen de forma más o menos simétrica en torno a un valor medio, especialmente cuando intervienen fluctuaciones aleatorias.
Las fluctuaciones son la suma de todos los errores posibles: fluctuaciones en la dosificación, diferencias de concentración de los componentes, componentes de la materia prima no homogéneos, fuerte heterogeneidad (los tamaños y densidades de las partículas varían mucho), errores en el muestreo, errores en el análisis de las muestras, errores de medición, .....
- t: Variable temporal que describe el tiempo de permanencia de una partícula en el mezclador
- μ: Valor medio: Tiempo medio de permanencia de la mezcla en el mezclador continuo
- σ: Desviación típica: Medida de la amplitud de la distribución del tiempo de permanencia.
- σ2: Varianza: La desviación típica al cuadrado indica la dispersión de los tiempos de permanencia en torno al valor medio.
- e: Número de Euler (aprox. 2,718).
- π: Número circular (aprox. 3.14159).
- f(t): Densidad de probabilidad para un determinado tiempo de permanencia t
La expresión describe el hecho de que los valores cercanos al valor medio μ tienen una probabilidad alta, mientras que los valores alejados de él tienen una probabilidad baja.
El factor de normalización garantiza que el área total bajo la curva corresponde al valor 1. La suma de las probabilidades es exactamente 100 %.
El diagrama muestra un ejemplo del tiempo de permanencia en una mezcladora continua. La línea discontinua roja muestra el tiempo de permanencia de la mayoría de las partículas de la mezcla.
Resulta ventajoso un proceso de mezcla continuo,
- Cuando se requiere un tiempo de permanencia corto definido
- si la desaglomeración debe producirse en poco tiempo
- cuando la mezcla se aglomera espontáneamente
- cuando la adición de líquido desencadena una reacción química espontánea
- cuando el resultado de la mezcla viene determinado por el aporte exacto de energía mecánica
- cuando se producen reacciones exotérmicas y hay que disipar grandes cantidades de calor
- Si el producto final fluye mal (por ejemplo, como una pasta o crema muy viscosa).
- Cuando el producto final consta de pocos componentes
- si se estandariza la receta y se garantiza la calidad de los componentes
- Cuando se producen grandes cantidades del mismo producto o de productos similares, posiblemente en tres turnos (productos a granel como alimentos básicos en molinos de grano, almidón, piensos, productos químicos básicos, jabones metálicos, detergente en polvo, derivados de la celulosa, productos semisólidos, plásticos, materiales de construcción).
- si las mercancías mezcladas van a envasarse directamente sin almacenamiento intermedio
- si .....
Aprovecha para realizar pruebas. En el centro técnico amixon® tiene a su disposición mezcladoras por lotes, mezcladoras continuas y sistemas de dosificación para sus ensayos de mezclado.
La mezcla por lotes resulta entonces ventajosa,
- si se trata de procesos de preparación complejos, por ejemplo, procesos de mezcla en varias fases o procesos de mezcla con aplicación de sobrepresión o vacío.
- si debe realizarse un análisis de laboratorio antes del llenado
- si la garantía de calidad insiste en el control de lotes y
- si la limpiezadebe realizarse después de cada preparación
- cuando intervienen muchos componentes. Es el caso de los alimentos infantiles, los nutrientes dietéticos, los agentes de panificación, los preparados de especias, los estabilizantes, los alimentos instantáneos, los condimentos, .....
- cuando se trata de productos a medida con recetas en constante evolución (complementos alimenticios, preparados de especias paraempresas cárnicas, aromas para la industria alimentaria, platos instantáneos, bebidas instantáneas,...)
El mezclador KoneSlid® de amixon® es una evolución de nuestro mezclador de cono. Mezcla de forma especialmente suave con un tiempo de mezcla extremadamente corto. La velocidad del mezclador es especialmente baja. Los productos que fluyen libremente se vacían por completo en cuestión de segundos.
Los mezcladores cónicos amixon® pueden mezclar materiales a granel tanto en lotes como de forma continua.
El mezclador cónico que se muestra aquí puede realizar fácilmente ambos procesos de mezcla cuando se coloca sobre celdas de carga. La mezcla continua requiere sistemas de dosificación que funcionen de forma continua.
Para sólidos muy difíciles de dosificar
En función del tipo de mezcla continua, pueden definirse espectros de tiempo de residencia. Los mezcladores continuos con grandes espectros de tiempo de residencia son tanto más capaces de compensar breves errores de dosificación.
Las particularidades de la mezcla continua en forma del clásico "flujo en tubería" y del clásico "flujo en caldera" se describen en otro apartado de este blog de amixon®.
Si una mezcladora continua es especialmente grande, la dosificación puede realizarse en pequeños lotes. Sin embargo, el tamaño de los lotes y los tiempos de adición deben definirse con precisión.
Las mezcladoras Gyraton® pueden mezclar de 10 a 100 m³ con precisión
La mezcladora Gyraton® se desarrolló para la homogeneización precisa de grandes lotes de polvo. Una misma mezcladora puede mezclar tanto lotes pequeños como grandes con una precisión ideal. Lo mismo se aplica al mezclador Gyraton® que a todos los demás mezcladores amixon®: no importa si los materiales a granel están secos, húmedos o mojados, si fluyen bien o mal o si son heterogéneos. ....
- La cámara de mezcla tiene un diseño cilíndrico que ahorra espacio.
- El motor de accionamiento es muy pequeño,
- La potencia de accionamiento es muy baja.
- Las partículas de la mezcla apenas se estresan.
- La mezcla no se calienta durante el mezclado.
- Esto hace que el funcionamiento sea muy económico.
La mezcladora Gyraton® es adecuada tanto para procesos de mezcla discontinuos como continuos. Hay disponibles mezcladores de prueba.
¿Cuál es el mayor reto en la mezcla continua de materiales a granel?
Cuando se requieren altas calidades de mezcla, el caudal másico exacto de los polvos es crucial. Todos los componentes de la mezcla deben entrar en la mezcladora al mismo tiempo y en la proporción correcta. A diferencia de los líquidos, los materiales a granel son mucho más difíciles de dosificar. Los errores de dosificación merman la calidad de la mezcla.
Sin embargo, los sistemas de mezcla de funcionamiento continuo se han consolidado desde la aparición de los sistemas de dosificación de polvo de precisión. Los modernos sistemas de dosificación de sólidos a granel reconocen incluso los pequeños errores de dosificación y los corrigen con gran rapidez. Los flujos de masa son precisos incluso a intervalos de tiempo cortos.
En cuanto a la calidad de la mezcla, son preferibles los dosificadores gravimétricos. También se conocen como dosificadores por pérdida de peso. Por regla general, cuanto mejor fluya el material a granel, más precisos serán los sistemas de dosificación continua.
Para no influir en la señal de pesaje, las bocas de entrada y salida están conectadas con manguitos plegables. En el interior de la carcasa de dosificación, una herramienta de aglomeración giratoria garantiza que el polvo se afloje uniformemente. De este modo, el tornillo dosificador recibe el producto suelto. Esto favorece el comportamiento de control.
El nivel de llenado de la tolva de pesaje de la unidad de dosificación disminuye continuamente. En el ejemplo mostrado, la tolva de pesaje se llena neumáticamente. El tiempo de llenado debe ser lo más corto posible. Durante este tiempo, el tornillo dosificador transporta a una velocidad constante sin control. En la práctica, suele aceptarse una "fase ciega" de este tipo.
© Copyright by amixon GmbH