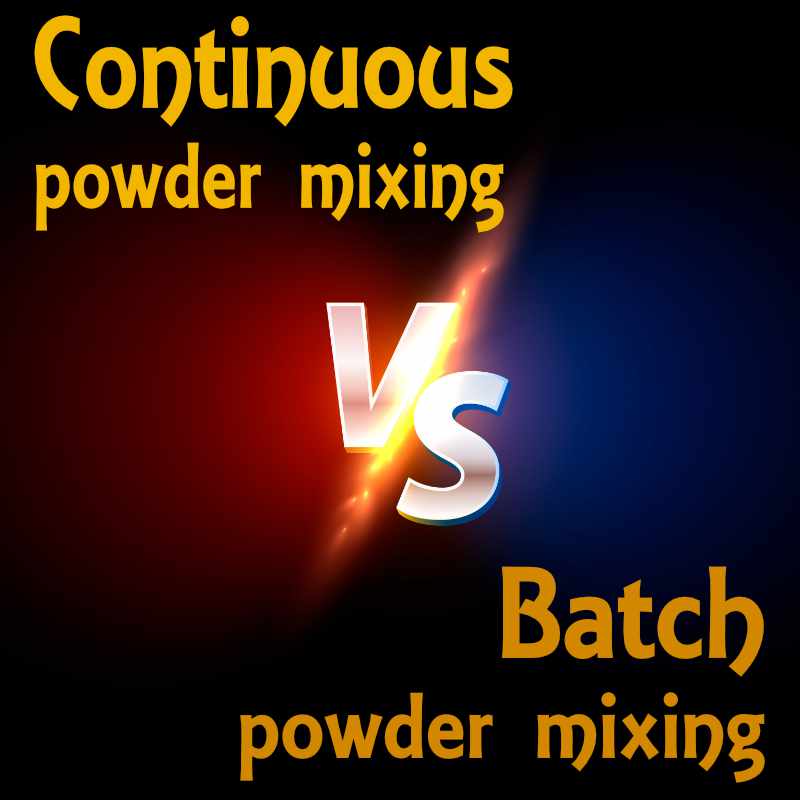
Batch mixing versus continuous mixing
Powder mixing and accompanying processes such as moistening, deagglomeration, agglomeration, heating, drying, cooling, gassing, bonding and much more can be carried out discontinuously or continuously.
However, there are also exclusion criteria. Certain mixing processes can only be carried out using one of the two mixing methods. This blog post deals with the advantages and disadvantages of both mixing methods.
amixon® mixers are used for both batch mixing processes and continuous mixing processes. Both mixing methods meet the requirements of the operators:
- high mixing quality and reliable reproducibility
- high flexibility when changing recipes
- robust mixing process, even with fluctuating bulk material consistency, the high mixing quality is achieved
- good residual emptying protects against contamination
- good accessibility
- good cleanability saves time and costs
- highest hygiene requirements are met
- long-lasting, solid machine construction guarantees minimal maintenance costs and
- long service life
General classification
If one were to compare the number of continuous mixers and batch mixers across all industries, one would quickly see that there are far more batch mixers. The range of different mixer types is also dominated by batch mixers.
In general, bulk materials are preferably mixed and treated continuously. However, if many components have to be mixed and if very high mixing qualities are required, then batch mixing is preferred. In practice, a batch mixer offers much more flexibility. This is another reason why batch mixing plants are much more common.
A batch mixer is comparatively easy to operate. In practice, it offers considerably more flexibility. This is another reason why batch mixing plants are much more common.
Comparison
The batch mixer - on the left - works in batches. The mixing tool only starts to rotate when the individual components have been filled in. The mixer changes the position of all particles in relation to each other by three-dimensional flowing of the goods. The state changes from "unmixed" to "technically ideally mixed". Only then does the discharge process take place.
In the case of continuous mixing - shown on the right - the components involved are continuously fed into the mixer in the correct mass ratio. The material streams are homogenized in the mixer and the mixed material is continuously discharged. In this case, the concentration gradient is lower because the so-called continuous boiler flow has already produced a homogeneous mix base. Input material flows are comparatively small in relation to the already homogenized vessel contents. For example, the average residence time can span between 0.5 and 3 minutes.
At this point, it should be noted that a distinction is made between two types of continuous powder mixing: The tube flow and the boiler flow.
The dwell time in the continuous mixer
The residence time distribution of mixed materials in a continuous mixer can be described by a Gaussian normal distribution function. The normal distribution is often used when the residence times are distributed more or less symmetrically around a mean value, especially when random fluctuations play a role.
The fluctuations are the sum of all possible errors: dosing fluctuations, concentration differences of the components, inhomogeneous raw material components, strong heterogeneity (particle sizes and densities vary greatly), errors in sampling, errors in sample analysis, measurement errors, .....
- t: Time variable that describes the dwell time of a particle in the mixer
- μ: Average value: Average dwell time of the mix in the continuous mixer
- σ: Standard deviation: A measure of the width of the dwell time distribution
- σ2: Variance: The squared standard deviation indicates the dispersion of the dwell times around the mean value
- e: Euler's number (approx. 2.718)
- π: Circular number (approx. 3.14159).
- f(t): Probability density for a given dwell time t
The expression describes the fact that values close to the mean value μ have a high probability, while values far away from it have a low probability.
The normalisation factor ensures that the total area under the curve corresponds to the value 1. The sum of the probabilities is exactly 100 %.
The diagram shows an example of the dwell time in a continuous mixer. The red dashed line shows the residence time of most of the mix particles.
A continuous mixing process is advantageous,
- if a defined short residence time is required
- if desagglomeration is to take place in a short time
- if the mix agglomerates spontaneously
- when the addition of liquid triggers a spontaneous chemical reaction
- when the mixing result is determined by the exact mechanical energy input
- when exothermic reactions take place and large amounts of heat have to be dissipated
- when the final product flows poorly (for example, like a highly viscous paste or cream)
- when the final product consists of only a few components
- when the recipe is standardised and the quality of the components is assured
- if large quantities of the same or similar products are produced, possibly in three shifts (bulk goods such as staple foods in grain mills, starch, animal feed, basic chemicals, metal soaps, washing powder, cellulose derivatives, semi-solid goods, plastics, building materials)
- if the mixed goods are to be packed directly without intermediate storage
- if .....
Take advantage of the opportunity to carry out trials. Batch mixers and continuous mixers, as well as dosing systems, are available for your mixing trials at the amixon® technical centre.
A batch mixing operation is advantageous,
- when complex preparation processes are performed, e.g. multistep mixing processes, or mixing processes with gaugepressure or vacuum application take place
- if a laboratory analysis must take place before packaging
- if quality assurance insists on batch control, and
- when cleaning must be performed after each batch
- if many components are involved. This is the case with baby food, dietary nutrients, baking agents, spice preparations, stabilizers, instant food, seasonings, ....
- when customized orders with ever changing recipes are involved (food supplements, spice preparations for meat companies, flavors for the food industry, instant meals, instant beverages,...)
The KoneSlid® mixer from amixon® is a further development of our conical mixer. It mixes particularly gently with an extremely short mixing time. The speed of the mixing tool is particularly low. Free-flowing products can be emptied in seconds without leaving any residue.
amixon® conical mixers can mix bulk materials both in batches and continuously
The cone mixer shown above can comfortably perform both mixing processes when resting on load cells. The requirement for continuous mixing is the presence of the dosing systems.
Please read the summary in table form!
For bulk solids that are very difficult to dose
Depending on the type of continuous mixing, residence time spectra can be defined. Continuous mixers with large residence time spectra are all the better able to compensate for brief dosing errors.
The special features of continuous mixing in the form of the classic "pipe flow" and the classic "boiler flow" are described elsewhere in this amixon® blog.
If a continuous mixer is particularly large, dosing can take place in small batches. However, the batch sizes and addition times must be precisely defined.
Gyraton® mixers can precisely mix 10 to 100 m³
The Gyraton® mixer was developed for the precise homogenisation of large powder batches. One and the same mixer can mix both small and large batches with ideal accuracy. The same applies to the Gyraton® mixer as to all other amixon® mixers: it does not matter whether the bulk materials are dry, moist or wet, whether they flow well or poorly, whether they are heterogeneous. ....
- The mixing chamber is cylindrical to save space.
- The drive motor is very small,
- the drive power is very low.
- The particles of the material to be mixed are hardly stressed at all.
- The material does not heat up during mixing.
- This makes operation very economical.
The Gyraton® mixer is suitable for both discontinuous and continuous mixing processes. Test mixers are available.
What is the biggest challenge in continuous mixing of bulk materials?
If high mixing quality is required, the exact mass flow of the powders is crucial. All the components of the mixture must enter the mixer simultaneously and in the correct proportions. In contrast to liquids, bulk materials are much more difficult to meter. Metering errors impair the mixing quality.
Nevertheless, continuous mixing plants have become established since the advent of precise powder metering devices. Modern dosing systems for bulk solids are able to recognise even small dosing errors and correct them very quickly. The mass flows are accurate even at short time intervals.
In terms of mixing quality, gravimetric dosing units are to be preferred. They are also referred to as loss-in-weight dosing units. Generally speaking, the better the bulk solid flows, the more accurately continuous dosing systems can work.
In order not to influence the weighing signal, the inlet and outlet nozzles are connected with folding sleeves. Inside the dosing housing, a rotating agitator tool ensures that the powder is evenly loosened. The dosing screw thus receives a loosened product. This favours the control behaviour.
The level in the weighing container of the feeder decreases continuously. In the example shown, the weighing container is filled pneumatically. The filling time should be as short as possible. During this time, the dosing screw conveys unregulated at a constant speed. In practice, such a ‘blind phase’ can usually be tolerated.
© Copyright by amixon GmbH