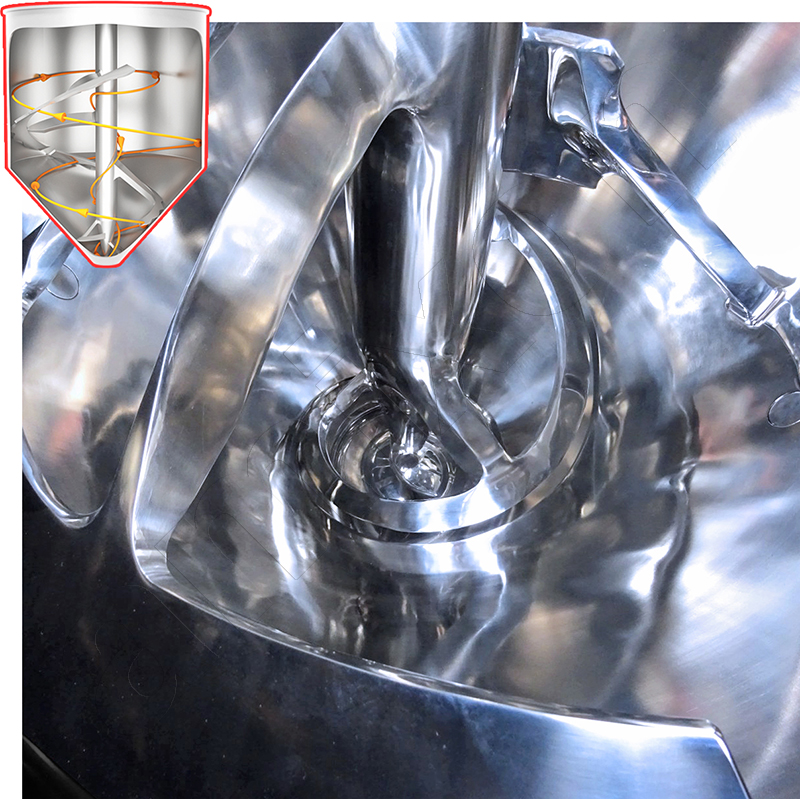
Producción de alimentos infantiles en mezcladores altamente higiénicos - amixon® Mixing Technology
La demanda de alimentos infantiles producidos industrialmente a partir de derivados de la leche en polvo es muy elevada en los países industrializados y emergentes, al igual que las exigencias de calidad y composición de los preparados en polvo utilizados.
Los microcomponentes como los probióticos, los prebióticos, los minerales y los oligoelementos —entre los que se encuentran elementos esenciales como el zinc, el cobre, el selenio o el cromo— deben distribuirse en los alimentos para bebés con la máxima precisión y uniformidad. Debido a las pequeñas cantidades de dosificación y a la gran relevancia para el equilibrio nutricional, solo se pueden utilizar mezcladores de precisión.
El proceso de mezcla debe ser cuidadoso: la estructura de las partículas de las materias primas debe mantenerse. Los ingredientes funcionales que están encapsulados, como las vitaminas o los cultivos probióticos, deben conservarse. Los productos mezclados no deben calentarse.
- Parte 1: Tecnología de mezcla para alimentos infantiles con el ejemplo del mezclador vertical de dos ejes HM
- Parte 2: Tecnología de mezcla® amixon para alimentos infantiles con el ejemplo de la mezcladora KoneSlid® KS y la mezcladora continua AMK
Los mezcladores amixon garantizan la conservación de las cualidades de las materias primas, en particular sus propiedades instantáneas cuando se disuelven en agua:
- Ausencia de polvo
- Dosificación, comportamiento de flujo
- Excelente dispersabilidad
- Humectabilidad fiable
- Hundimiento rápido
- Disolución segura
Los mezcladores® amixon consiguen siempre una calidad de mezcla ideal. Independientemente del tamaño de las partículas, la densidad aparente o las propiedades de flujo.
Además, amixon® garantiza un vaciado rápido y casi completo de los mezcladores de polvo. De este modo se evitan pérdidas de producto y contaminaciones cruzadas.
Los sistemas de mezcla® amixon cumplen con los más altos estándares de higiene y están diseñados de acuerdo con las directrices de tecnología alimentaria aplicables (por ejemplo, EHEDG, FDA, GMP).
© Copyright by amixon GmbH