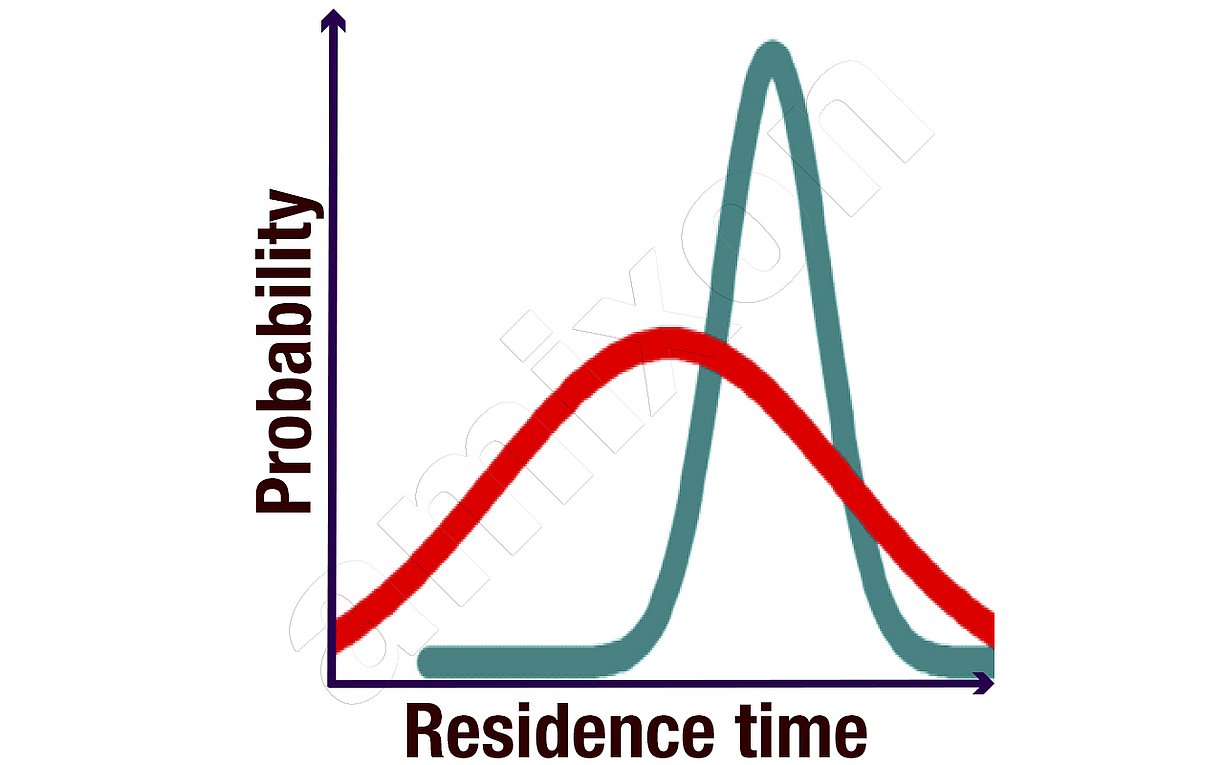
The red line depicts the residence time of the mixing goods during a continuous boiler flow. The green line depicts the residence time of the mixing goods during a pipe flow.
Continuous mixing of powders: Pipe flow versus boiler flow
The industrial mixing and wetting of powdery goods takes place either batchwise or continuously.
In industry, bulk materials are mixed in batches or continuously. Mixing" is used here as a generic term for a variety of accompanying processes such as deagglomeration, crushing, colouring, decaking, coating, liquid wetting, agglomeration, tempering, mixer drying, synthesis reaction, bonding, ... Please also read our blog post: "Continuous mixing versus batch mixing"!
In the case of continuous mixing, a distinction is made between the pipe flow and the boiler flow. In practice, there are also hybride forms of both processes.
Pipe flow
If the mixing takes place in the form of the pipe flow, then the continuously introduced components are conveyed from right to left. Mixing tools convey and swirl the mixing goods. The principle of "first-in-first-out" applies here. The mixing effect is intensified when individual tools convey against the flow direction. An increased degree of filling is present there. The more return conveyance takes place, the longer the residence time. Increased return conveyance also requires increased energy input.
Boiler flow
In the case of continuous boiler flow, the main flow direction is determined by gravity. A helical mixing tool distributes the mixed goods particularly effectively by conveying them upwards. A very high mixing quality is already achieved after just eight revolutions. The raw material components are continuously fed into the mixing chamber from above and flow into the completely homogenized mix bed. They are randomly distributed in the mixing room. A constant filling level is set in the mixing chamber, which can be between 40% and 80%, for example.
Boiler flow in this context refers to the fact that almost all components are present in homogenized form in the mixing chamber. Raw material components are added continuously. They are added in the correct ratio and their volume flow is comparatively small. The mixing efficiency is calculated in such a way that they are homogenized after a few seconds in the mixing chamber.
Question from a customer: Which type of continuous mixing is to be preferred in the bulk solids processing industry: the pipe flow or the boiler flow?
Response from amixon®: There is no general answer to this question. Both systems have specific advantages. It always depends on the respective application.
The pipe flow is always preferable to the boiler flow:
- if the preparation process is time-critical, such as rapid tempering, build-up granulation, coating, or if components should react spontaneously chemically ...
- if substances are difficult to mix, in particular if intensive deaglomeration is required during mixing, if liquid additives are highly viscous or adherent
- if the vertical installation space is limited
- if additives must be mixed in one after the other in sequence ... along the mixing chamber. - This may be the case if the particles of the mixture have to be coated with different substances one after the other
- ...
Boiler flow is to be preferred to pipe flow
- if start-up losses are to be avoided when starting the mixing plant.
- The very first grams of the mixed product should be homogeneous according to specification.
- if the mixer should compensate for short-term dosing errors in the best possible way
- if the mixing process has to take place particularly gently
- when a wide spectrum of residence periods is desired
- if the same mixer should be able to homogenize both large and very small volume flows
- if the same mixer should also serve as a precision batch mixer.
- For example, the same amixon® conical mixer can prepare a premix from many small components. This premix is later continuously mixed with other components in the same mixer.
- ....
amixon GmbH can conveniently demonstrate the continuous mixing methods described above for you, so please feel free to come to our technical centre in Paderborn with your products. We will be happy to demonstrate the mixing processes to you!
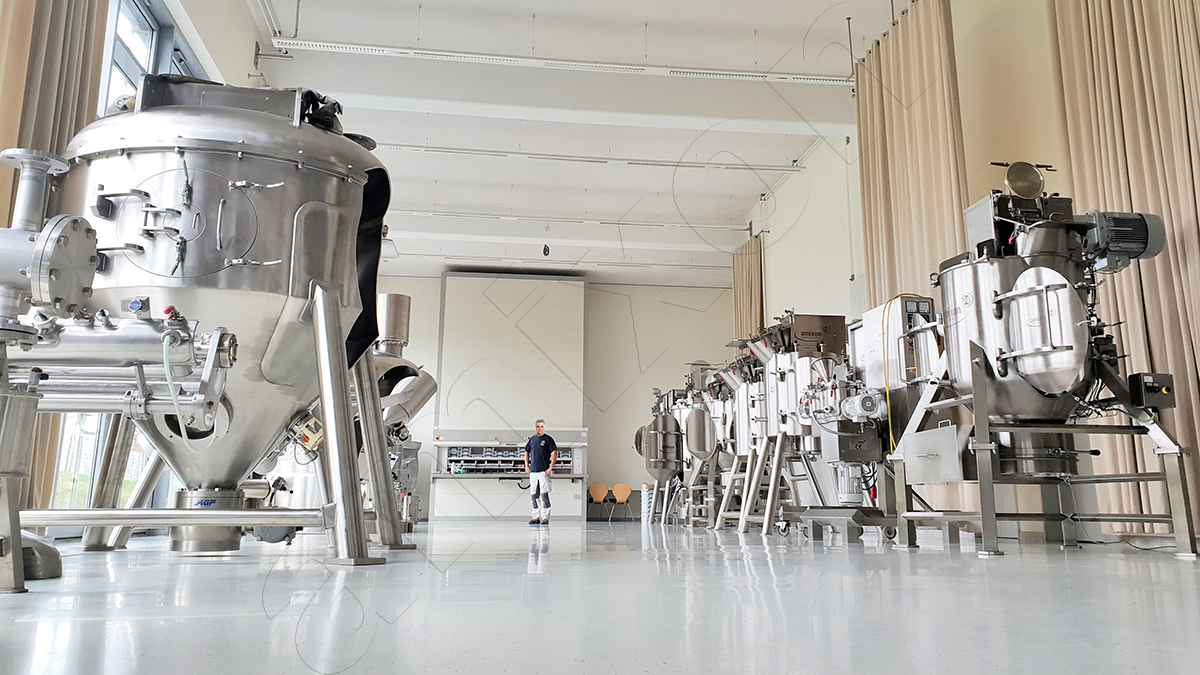
© Copyright by amixon GmbH