Mixers for detergent powder manufacturing
Even in difficult economic times, laundry detergents and household cleaners are stable core sales drivers and highly competitive. Manufacturers operate in a competitive and customer-oriented market environment in which innovative strength and brand reputation are crucial. Market leaders enjoy a high level of consumer trust, which must be defended again and again. In times of dwindling resources and polluted seas, the demand on manufacturers is growing.
The goal is either: (1) Reducing batch times through shorter mixing times while ensuring ideal mixing qualities. Efficient use of raw materials through better residual discharge.
Or: (2) Increasing production output by making the mixing operation continuous.
For almost forty years, amixon® has been developing and manufacturing high-precision mixing systems to meet the requirements of powder detergents and liquid detergents as well as household cleaners.
Benefit from innovative, tailor-made solutions for your product and specifications.
amixon® reactors are used for the preparation of metall soaps for a wide range of industrial needs.
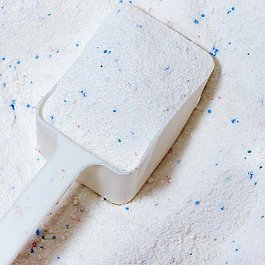
Requirements for cleaning product and detergent making equipment
The quality of your washing powder is determined by its ingredients, formulation, and processing. Washing powder manufacturers must pay special attention to particle size and homogeneity in order to create an end product that cleans powerfully, dissolves readily, and stores easily.
The detergent powder manufacturing process involves many challenges, including eliminating dust, breaking up clumps, forming uniform agglomerates, and avoiding excessively long processing cycles. Furthermore, many of the ingredients in household detergents are heat-sensitive. Because mixing processes generate heat, mixers for dishwasher and laundry detergent manufacturing must be able to work both quickly and gently.
amixon® mixers as detergent making machines
amixon® detergent mixing machines are up for the challenge. Our powder mixing equipment gently yet efficiently creates perfectly homogenous mixtures with varying filling levels as low as 5%.
With adjustable processing settings ranging from intensive deagglomeration to tumble growth granulation, from drying to coating, you can fine-tune the mixing process in order to create the ideal conditions for your washing powder formula.
All of our mixing equipment is designed in according to EHEDG, FDA, and GDMP standards, facilitating the certification processes for your detergent manufacturing facilities.
And with global testing centers located in Europe, North America, and throughout Asia, our processing and validation experts are always on-hand to help you ensure the highest performance and quality standards in your detergent making equipment. Together, we can develop a detergent powder mixer that meets all of your processing requirements.
Industrial mixers for cleaning product manufacturers
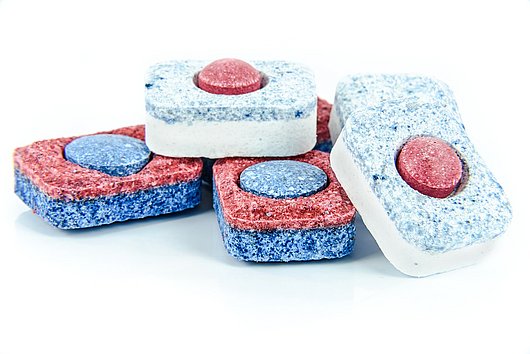
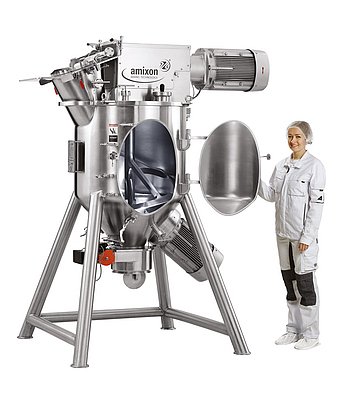
Mixing heat sensitive detergent formulations
The 3-in-1 vacuum dryer, powder mixer, and reactor AMT makes it possible to carry out multiple processing steps in a single piece of equipment.
The vessel is pressurized and airtight, capable of reducing the atmospheric pressure and thus the temperature at which liquids evaporate. Every product contact surface within the mixer is jacketed and can be cooled for mixing especially heat-sensitive detergent formulations.
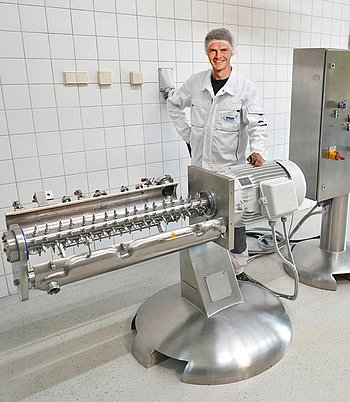
Create uniform granules
The RMG pin mixer and continuous granulator is the ideal mixing machine for creating agglomerated detergents. Loose powders are granulated through tumble-growth techniques, accumulating into perfectly uniform granules.
Products agglomerated with the amixon® RMG pin mixer are easy to store, dose, and measure, offer improved solubility and bulk density. In addition, the detergent granules are uniform in shape and size, offering improved aesthetic characteristics.
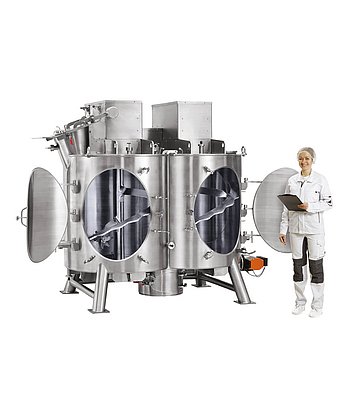
Deagglomerate, disperse, and coat
The dual shaft vertical mixer HM is a versatile powder mixer for handling detergent powders at a number of processing junctures.
Chemical formulations that are prone to lumping can be intensively deagglomerated before their dispersal into bulk materials. Alternatively, viscous or liquid additives can be effectively dispersed into bulk powders during the mixing process via a built-in spray nozzle and high-shear cutting rotor.