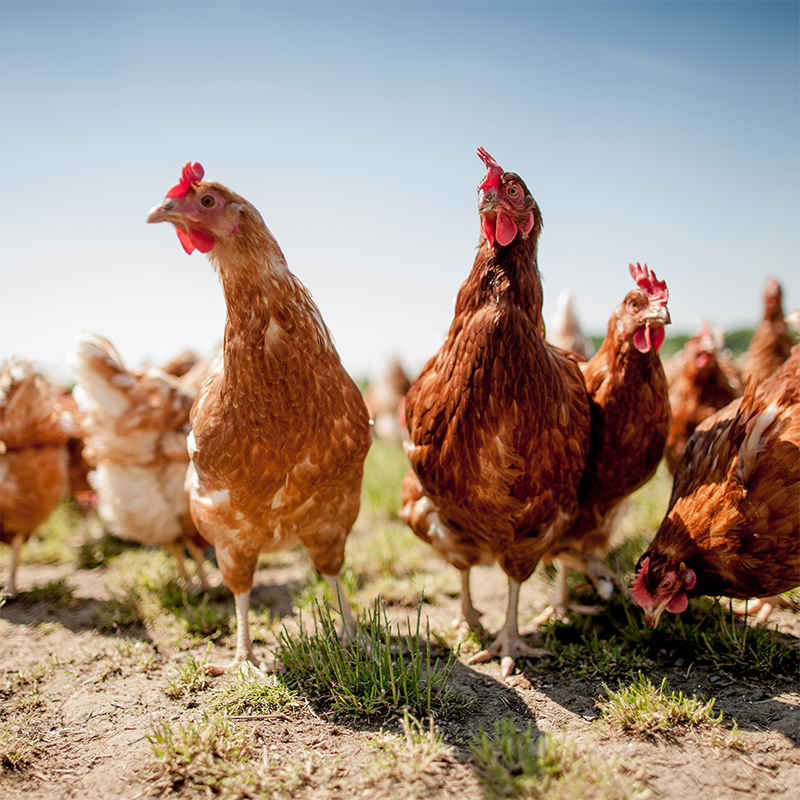
Our solutions for the animal feed industry
Optimal animal feed mixer for cattle, poultry, pigs, etc.
Farm animals must meet high quality criteria: in particular, it must be pure. It must be declared and traceable. The feed must contain exactly the nutrients that the fattening animal needs in the respective growth phase.
The form of administration is also important: the feed should be free-flowing and dust-free. Only then can it be used in automatic feeding systems.
- For example, concentrated feed for dairy cows should have a high crude fibre content to ensure good digestibility and low methane formation.
- Concentrated feed for pigs should contain little phosphorus but the right amino acids.
- Concentrated feed for poultry should contain certain enzymes and highly digestible proteins.
amixon® mixers guarantee the best mixing quality and complete emptying
The multitude of components and the constantly changing recipes require logistical feats from the feed manufacturers. Raw material components whose daily price seems unsuitable or which are not available on the market often have to be replaced by others with comparable nutritional content.
The challenge for the mixer as a value-adding device in the production chain is therefore to achieve ideal mixing qualities that cannot be improved in practice. And all this
- in a short time and
- with variable filling levels
- with minimal energy input and
- best possible wear resistance
- fast and complete emptying within a few seconds
- long service life
- Good accessibility and easy cleaning of the mixing chamber
- Ergonomic accessibility of the mixing chamber
- Easy repair of worn components – preferably by your own, specially trained mechanics.
‘In practice, the mixing quality is synonymous with the homogeneity of a mixture. It describes the ability of a mixing plant to ‘homogeneously mix different quantities of individual components in a defined time’.
Determining the mixing quality of a heterogeneous bulk material is a complex process engineering challenge. There are more than 20 different formulas for defining the mixing quality. Practice-oriented methods have been established for verifying the mixing quality of animal feed. Organic food colouring or microtracers are added to the feed in a ratio of 1:100,000 – which corresponds to 100 grams of active ingredient per tonne. After a defined mixing time, a sufficient number of samples - usually at least ten - with a sufficiently large volume - in practice often 20 g - are taken at various points in the mixing chamber using a sample scoop and analysed. The quality of the mixing quality analysis obtained depends on many parameters, but in particular on the number of samples and the selected sample volume. It is particularly important to divide or portion the sample piles in such a way that segregation is avoided.
Evaluation of the process route for newly developed product types
Challenging situations sometimes arise when a completely new product type or process is to be established or when a new mixer is put into operation. The compound feed plant then wants to know how homogeneity develops during the mixing time and how long it has to mix to achieve a sufficiently high mixing quality. To find this out, the following procedure can be adopted: the sampling is repeated as described above after further short mixing times. For example, the first ten samples are taken after about 180 seconds, the second ten samples after a further 30 seconds of mixing time, etc.
In the case of a thoroughly tested mixer, its universal mixing efficiency is considered to be validated. In this respect, it is then sufficient to take the sample during the rotation of the mixing tool with a sampler that has no dead space. This also applies to retention samples.
To achieve a high degree of mixing quality, the particle size distribution also plays a role. Experience has shown that the homogenisation of small components in the base material is most successful when the particle size is between 200 and 500 micrometres. If the particles are considerably smaller, they are more difficult to meter and control, may inadvertently enter the dust collection filters or randomly attach themselves to larger particles, thus making even distribution more difficult.
Calf milk replacer powders are enriched with fat and nutrients
When calves are separated from their mother cows at an advanced age, the mother cow's udder is no longer available for feeding. Special dry milk derivatives are enriched with fat, trace elements and vitamins. The finished mixture is packaged in small containers. The product is then suspended or dissolved in water as needed and is particularly nutritious for the young animal.
In the amixon® double-shaft mixer, 3 m³ of calf milk replacer is enriched with large quantities of fat. Nevertheless, the finished mixture is free-flowing. The discharge fitting is particularly large for fast and thorough emptying.
Avoiding cross-contamination during batch mixing
Batch purity is an extremely important requirement for precision mixing in animal nutrition. For example, micro-ingredients that are good for cows can be harmful for poultry. Therefore, it is essential to prove that cross-contamination has been adequately avoided. The test is carried out in the same way as the test for mixture quality. After a regular mixing batch, another one is mixed – without an active ingredient. When this ‘0’ batch is examined, no active ingredient may be found. The examination can be carried out specifically for the mixer or for the entire system: batch scale, conveyor elements, collection silo, shredder, etc.
The requirement for contamination-free production can only be met if the mixer mixes quickly and precisely. However, it must also empty quickly and completely. amixon® has developed a precision mixer called KoneSlid® for this purpose. It mixes in a matter of seconds and empties itself just as quickly. KoneSlid® mixers work economically and with little wear.
amixon® manufactures precision mixers, reactors, vacuum mixing dryers and fermenters
Inside a cylindrical-conical mixing container, a helical mixing tool rotates. The SinConcave® mixing tool is centrally driven and mounted at the top. The batch is fed in from above and the amixon® apparatus is emptied below the mixing chamber. A dead-space-free shut-off device opens in the cone of the mixing chamber. All parts that come into contact with the product are carefully welded and ground, as is the mixing tool. Blade-like arms support the mixing helix (SinConcave® design).
Optionally, the mixing tool can be heated completely, in which case the mixing shaft, the arms and the mixing helix are double-walled. The thermal fluid maintains the temperature of the entire mixing tool. Steam, water or thermal oil can be used as heat transfer media.
The mixing tool generates a dead-space-free total flow. Sometimes it is necessary to disagglomerate or to distribute liquid additives particularly effectively in the powder. In this case, chopper tools or high-shear blades are used, which release a high power density in the powder in certain areas. It does not matter whether the goods are granular, dusty, fibrous, dry, moist, pasty, liquid, free-flowing or non-free-flowing. The mixing tool is designed so that after about four to five rotations, it has circulated the entire contents once. This flow principle is also referred to as a boiler flow. As a rule, after a few rotations, a homogeneous uniform distribution of all components is present everywhere in the mixing chamber and one speaks of an ideal mixing quality that cannot be improved in practice.
The dead-space-free discharge valve can also be replaced by a horizontal conveyor. Horizontal conveyors are always useful when the product discharge is to be metered.
amixon® fermenters/reactors are used:
- when an organic product is to be sterilised with saturated steam
- in the production of penicillins or
- when enzymatic fermentation is to take place
- when a particularly gentle vacuum drying process is to take place
- when porous bulk materials (pellet extrudates) are to be impregnated pore-deep with higher-viscosity liquids. (Vacuum application removes gas from the pores. The subsequent pressure build-up stabilises the impregnation).
Concentrate feed mixtures account for up to 14% of livestock feeding
The days when farmers still fed their cattle and pigs entirely with grass, hay, grain, beet and silage from their own production are long gone. Today, the feed produced by the farms themselves serves only as ‘basic feed’. In addition, so-called ‘concentrated feed’ is indispensable. This term refers to all feeds with an increased nutrient concentration and other additives. A distinction is made between straight feeding stuffs and compound feeding stuffs. Straight feeding stuffs with a high nutrient concentration include fats, soybean meal and molasses pulp, a residual product from sugar beet processing.
The term compound feed already refers to the mixture of two straight feeds. But modern compound feeds are in fact highly complex compounds that are composed of several straight feeds and selected additives, thus individually covering the specific, current nutrient requirements of the different animals. A typical compound feed today consists on average of eight to twelve straight feeds and up to 15 additives. The most important single-component feedstuffs in terms of quantity are the various types of grain, such as wheat, barley and corn, followed by rapeseed and soybean meal. Feed additives include minerals, vitamins, amino acids, trace elements and enzymes.
According to current figures from the German Farmers' Association, feed mixtures account for around 14 per cent of livestock feeding in Germany. 54 per cent are basic feed and 32 per cent are straight feed. According to the German Animal Nutrition Association, in 2020 the feed industry produced 24.1 million tonnes of compound feed, 9.8 million tonnes for pigs, 6.9 million tonnes for cattle and 6.4 million tonnes for poultry.
The German animal feed industry is characterised by medium-sized companies. At the end of 2020, there were 287 compound feed manufacturers that generated a turnover of 6.8 billion euros. There is a concentration in northern Germany. In the south, the demand for compound feed is lower because the animal populations are smaller.
Trend towards individual feed mixtures
Even though the industry is dominated by medium-sized companies, mixed feed formulations are being further developed with scientific commitment. A distinction is made not only according to the type of animal, but also according to the intended purpose, development level and performance capacity of the animals. Differences in nutrient requirements, digestive systems and metabolic mechanisms must also be taken into account. After all, it must also taste good to the animals and get from the silo truck to the day silo and from there without segregation to each individual animal. Hence, it is not uncommon for a single manufacturer to offer several hundred different recipes and formulations of mixed feeds.
In cattle farming, there are specifically tailored mixtures for calves, young cattle, dairy cows, fattening bulls and dry cows (cows in the phase between two calvings). In bull fattening, for example, the requirements are: high daily weight gains, a lot of muscle meat, low corpulence, a healthy bovine stomach and few illness-related losses. However, the basic feed usually has too few proteins for rapid muscle building. There is also a deficiency of minerals, vitamins and trace elements in the basic feed. A correspondingly designed mixed feed for bull fattening compensates for these deficiencies.
Modern farmers first have their self-produced basic feed analysed in order to determine the exact concentrations of nutrients (carbohydrates, fats and proteins), minerals (calcium, sodium, magnesium, etc.) and trace elements (zinc, copper, iodine, etc.). The mixed feed composition is then precisely matched to the farm-specific basic feed.
Although the basic feed analysis is initially associated with costs, these are usually quickly amortised, since the individual feeding makes the livestock farm more cost-effective. This is because all unnecessary minerals and trace elements contained in the mixed feed are cost drivers.
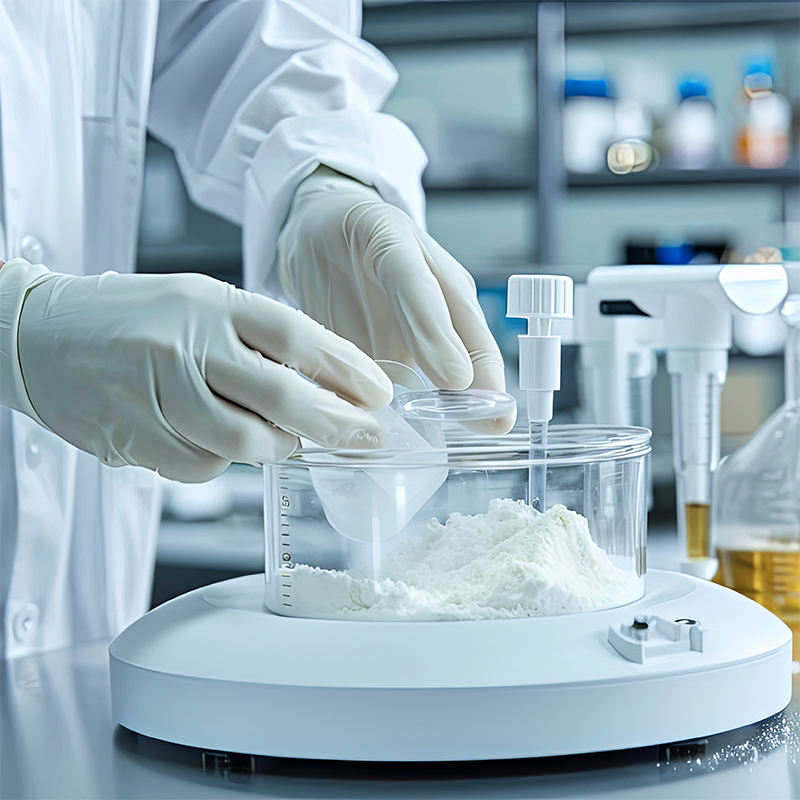
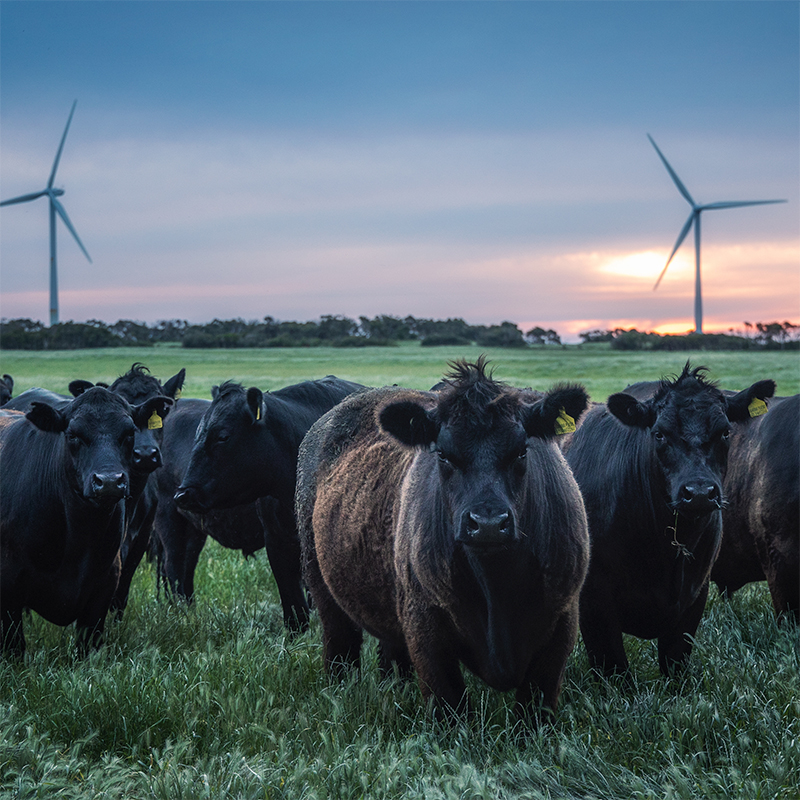
Precisely tailored feed for animal welfare and environmental protection
Flexible, customised feed production also makes it possible to adapt to extreme weather conditions. For example, dairy cows can suffer from heat stress during the summer months. At an outside temperature of 24°C, the animals‘ well-being begins to wane, they eat less and ultimately produce less milk. During a summer heat wave, adding sodium carbonate to the cows’ feed can be helpful.
A finely tuned feed mixture can even contribute to environmental protection. Regular fertilisation of agricultural land is essential for high yields. Slurry is, in principle, a good fertiliser when it is applied correctly and in moderation. But more is not always better. Sometimes its phosphate and nitrogen inputs contaminate our drinking water. Dairy cows need an adequate supply of phosphorus. A phosphorus deficiency leads to reduced feed intake, milk yield and fertility. If there is an oversupply of phosphorus, the dairy cow reacts by increasing its phosphate excretion. Cleverly balanced component compositions also determine the quality of the slurry as fertiliser and help to protect both arable land and groundwater. For example, the feed manufacturer Agravis offers a ration calculation tool called ‘Phokus’ that makes it possible to specifically lower the phosphorus content in feeding.
Read some statements of various owners of medium-sized animal feed businesses here.
Recipe and process development
When mixing animal feed, the even distribution of the individual components is crucial. This is because each individual animal only receives a minimal fraction of a batch. Ideally, this fraction should have exactly the same composition for each animal on a farm. This also applies to each individual feeding ration, even if some trace elements have only been added in extremely small quantities. Feed mixers should be able to evenly distribute very small proportions by mass in ground grain. In the industry, the requirement for the composition of the mixture is formulated as 1 in 10,000 to 1 in 100,000. This is a requirement, not a measure of the quality of the mixture.
Feedstuffs are bulk products, and feed manufacturers produce them with very small profit margins. In this respect, a further requirement is that the residence time of the mixed materials in the mixer – and even in the plant – should be as short as possible. It is not uncommon for the duration of a mixing batch to be only four to six minutes. During this time, the mixer is loaded with all the components in the formulation, mixed, emptied and the emptying device is closed. Such a short mixing cycle in a 12 m³ mixer requires specific mixing machine features.
The interaction between formulation development, component supply, component weighing, homogenisation of the mixer and the absorption capacity of the downstream units requires a great deal of expertise on the part of the operator. Ultimately, the energy balance must also be right. Every unit used for in-house bulk material logistics and product processing must be supplied with electrical energy. It is subject to wear and tear and makes the compound feed more expensive.
Selection of a suitable mixer
The homogeneity of a mixture is often described by the coefficient of variation (CV):
CV = (σ / μ) × 100 %.
- σ = standard deviation of the concentration of a component
- μ = mean value of the concentration of a component fraction
In practice, an ideal mixing quality can be defined as follows: a precision mixer is used that is best suited for the purpose. This mixer achieves the lowest possible coefficient of variation CV.
The homogeneity achieved with this precision mixer cannot be improved in practice. For many powder mixtures, a target value of CV < 5% can be achieved.
The more heterogeneous the powder composition, the poorer the achievable mixing quality. The sample of the mixture to be analysed should be a fraction of the portion used by the end user.
Precision mixers – whether with horizontally or vertically rotating mixing tools – meet the mixing quality criteria for animal feed mixtures without reservations. However, there are major differences in
- the mixing time,
- the flexibility of the filling level,
- the degree of residue-free emptying,
- the cleanability/accessibility,
- the emptying speed and
- the power requirement of the drive.
In order to select a suitable mixing system, the space requirements of the mixers must be coordinated with the space available on site. amixon® can customise its mixers; from a low, flat version to a slim version when the available footprint is small. In addition, amixon® can also produce any desired size in 100 litre steps. Otherwise, the aforementioned criteria "Requirements for the mixer" apply. Common batch volumes in the animal feed industry range from two to six tonnes (about 4 to 12 m³) and for mineral mixtures one to three tonnes (about 1 to 3 m³).
Factors for a functioning powder moistening in the mixing process
Precise dosing and homogeneous distribution of liquids
Feed mixtures also contain various liquid additives such as fat, water, amino acids, molasses or vitamins – just the right amount that the farm animals need. In addition, the dust particles should be bound and the taste improved.
As a rule, only small quantities of liquid are added to powdered feed. If liquid additives are necessary, it is important that the mixer wets all particles as uniformly as possible.
In this context, it is interesting to note that the porosity of the bulk material increases slightly with a small addition of liquid, the bulk becomes looser and more free-flowing, the volume of the mixture increases slightly, the dust content decreases and the flowability improves marginally. But wetting a mixture with a wide particle size distribution quickly and evenly is no easy task.
Post-treatment below the mixer can shorten the process time
If the cycle times are very short, all liquid additions must be pumped into the mixer correspondingly quickly. After a short mixing time, the amixon® twin-shaft mixer contains a homogeneous product. However, isolated agglomerates (diameter 2 to 5 mm) may still be present. Although these wet agglomerates are homogeneously distributed throughout the mixing chamber, they are not yet completely dispersed in the mixed feed. In order to distribute them completely with the high-speed cutting rotors, the mixing process would have to be extended, even though the mixing quality has already been achieved. In this case, a post-treatment method has established itself as more energy-saving.
In order to completely crush agglomerates, it makes sense to install a so-called finisher below the mixer. The mixture passes through the finisher continuously at a high flow rate. The specific energy input is minimal. Even in the smallest volume, all liquid components can then be detected in the correct composition.
amixon® is a brand of precision mixers with vertically mounted mixing shafts
Inside a cylindrical mixing vessel, a spiral-shaped mixing tool rotates, which is driven and mounted centrally and only at the top. The mixing materials are fed in from above, and the mixer is emptied from below by opening a flap that closes in a plane with the mixing chamber floor. This is a dead-space-free operating valve, which is opened and closed electropneumatically within a connecting piece. All components that come into contact with the product are carefully welded and polished, as is the mixing tool. Blade-like arms carry the mixing helix, which is manufactured here in a ‘concave shape’.
Optionally, the mixing tool can be heated throughout, in which case the mixing shaft, arms and blades are designed with a double jacket. The thermal fluid maintains the temperature of the entire mixing tool. Steam, water or thermal oil can be used as thermal fluids. The mixing tool generates a space-dominating total flow without dead spaces. Sometimes it is necessary to disagglomerate or to distribute liquid additives particularly effectively in the powder. In such cases, the chopper blades or high-shear blades are used, which partially release a high power density in the powder. It is irrelevant whether the goods are granular, dusty, fibrous, dry, moist, pasty, liquid, or whether they flow well or poorly. The mixing tool is designed so that it has rearranged the entire contents once after about four to five revolutions. This flow principle is also called boiler flow. After a few revolutions, a homogeneous uniform distribution of all components is regularly present throughout the mixing chamber and one speaks of an ideal mixing quality that cannot be improved in practice.
Mineral mixtures with trace elements and vitamins
A special form of feed supplement is the so-called mineral preparations. They are added in small proportions to the compound feed of farm animals. The formulations are specially tailored to the needs of cattle, pigs, horses and poultry. These are mixtures of lime and active ingredients, which optionally contain iron, vitamin C, calcium, zinc, iodine, copper, selenium, chromium, fluorine, potassium, sodium, magnesium or phosphorus. Since they function as minor active ingredient components in mixed feed, they must be particularly homogeneous and easy to distribute. To make them low-dust, they are partially encapsulated or agglomerated. The aim is to achieve a lump- and dust-free product with the highest mixing quality for these products as well.
Regardless of which amixon® mixer is used – a single-shaft mixer or twin-shaft mixer – ideal mixing quality is always achieved. The two mixer types differ only in the mixing time required and the associated energy input.
If the energy input is to be minimised, there is no alternative to the twin-shaft mixer (except for the KoneSlid® mixer). This:
- achieves an ideal mixing quality in a very short time
- dispenses the goods particularly gently with minimal energy input
- has a low and particularly compact design
- can handle varying filling levels
- is particularly accessible and is manufactured to the highest hygienic standards
- is suitable for all types of dry, moist and suspended goods
- ensures particularly good residual emptying
- can optionally be equipped with several discharge nozzles
- Like all amixon® mixers, it has a mixing shaft that is only supported and driven at the top.
Criteria for a mixer (exemplary list), which must be defined and weighted individually for each requirement:
The list is exemplary and should be individually supplemented.
- Strongly varying filling levels do/do not occur
- Gentle mixing of particles required/not required
- Liquid distribution necessary/not necessary even at low filling levels
- Particularly gentle fluid distribution required/....
- Intensive deagglomeration and particularly fast liquid distribution required/....
- Very fast discharge required/....
- Slow or clocked complete discharge desired /....
- Best possible complete discharge/....
- Discharge into several filling machines either optionally or simultaneously desired /....
- Lowest possible energy consumption desired/....
- Special wear protection required/....
- The mixer is also to be used for process and product development and must therefore be highly versatile /....
- Mainly single-product production /....
- Various mixing tasks are to be carried out in quick succession without intermediate cleaning /....
- Large hygienic inspection door: Ergonomic accessibility for quick dry cleaning /....
- Fast wet cleaning and drying must be possible frequently /....
- liquids are to be impregnated in granules/....
- pressure or vacuum tightness of the mixing chamber required/....
- the finished mixture is available in different bulk densities: from .... kg/dm³ to .... kg/dm³
- the mixture is to be tempered in the mixer/....
- gassing (inert gas to improve the minimum durability) is to take place in the mixer/....
- .....
- ....
© Copyright by amixon GmbH