Powder mixing equipment for pharmaceutical production
Following the extraction of the active ingredient, the process steps formulation and powder preparation are quality-determining for the galenics.
Highly concentrated active ingredients must be precisely and homogeneously distributed in suitable fillers. The end product is a pharmaceutical preparation that has defined active ingredient concentrations. The active ingredients have to release in the patient's body as intended in order to take effect. During production, all those parameters that can positively or negatively influence the mixing process, must be controlled. Neglecting quality assurance measures can lead to insufficient distribution or even segregation of active ingredients in the powder.
A good understanding of mixing processes, relevant parameters, material properties, particle technology, environmental conditions and the design of the mixing system are of great relevance. amixon® is aware of this responsibility and is available to you as a strong partner for your pharmaceutical industrial mixer.
In this sense, precise pharmaceutical powder mixing is imperative in order to ensure the health and safety of consumers. With amixon®, pharmaceutical manufacturers find state-of-the-art mixing technology matched with comprehensive validation and regulatory expertise.
We take seriously our responsibility to help bring pharmaceuticals to market that can save and improve lives.
The role of powder blenders and mixers in pharmaceutical production
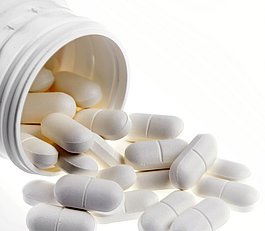
Mixing equipment has a key role to play in medication manufacturing, as this processing step is decisive to the resulting batch quality.
In order to create safe and hygienic medications that contain precise amounts of active ingredients, pharmaceutical mixing equipment must be easy to sanitize and flexibly configurable in order to create batches with uniform homogeneity, purity, particle size distribution, and stability.
Here are some of the key features of amixon® powder mixers that make them indispensable for pharmaceutical production:
- Homogenous batches at varying filling levels ranging from 5 to 100 percent
- Gentle yet thorough mixing preserves delicate particle structure
- Mixtures are dust-free, with excellent sinkability and solubility characteristics.
- amixon® pharmaceutical mixers are built to comply with the strictest hygiene regulations
- Equipped with innovative technologies for better processing, discharge, and cleaning
Mixer compliance in the pharmaceutical manufacturing process
Pharmaceutical manufacturers are subject to incredibly stringent regulatory oversight. Not only must the entire pharmaceutical production process be validated, verified, and inspected, but processing equipment must be flexible enough to be meticulously fine-tuned.
All amixon® mixing equipment is designed according to EHEDG, FDA, and GMP standards, facilitating the health and safety certification process for your pharmaceutical production facilities.
Our pharmaceutical powder mixers are equipped with innovative hygienic design features and technologies to facilitate complete discharge and easy sanitation:
- ComDisc® technology achieves 99.997% discharge, leaving virtually no product behind in the mixer
- CleverCut® inspection doors grant easy, ergonomic access to the mixing chamber
- WaterDragon® built-in, automated wet-cleaning system simplifies sterilize-in-place processes
With global testing centers located in Europe, North America, and throughout Asia, our processing and validation experts are always on-hand to help you ensure the highest performance and quality standards.
Together, we can develop a pharmaceutical powder mixer that meets all of your processing requirements.
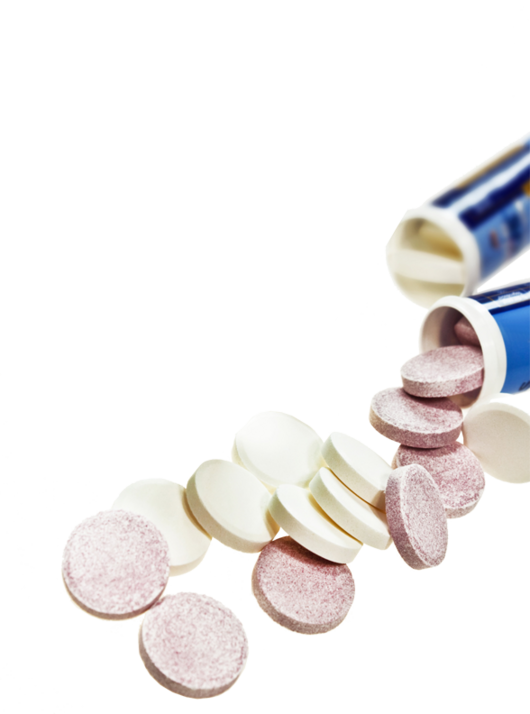
Our pharmaceutical powder mixers
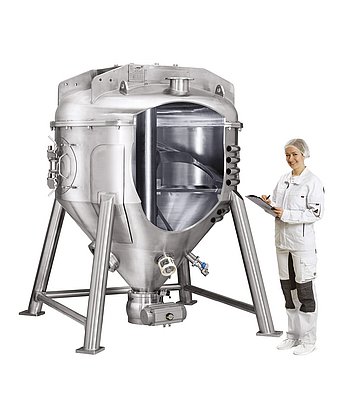
Vacuum Dryer & Mix-Reactor AMT
Many active ingredients become less effective when exposed to excess heat. And due to their toxicity, certain synthetic substances must be processed under airtight conditions.
The 3-in1 AMT vacuum dryer, mixer, and reactor from amixon® makes it possible to successfully process these sensitive ingredients. Because of their pressurized chambers, amixon® vacuum dryers are capable of reducing the flashpoint of a watery suspension from 212°F (or 100°C, the normal boiling point of water) to just 95°F (35°C).
Furthermore, every component of the machine is jacketed for thermal transfer, from the helical mixing blade, to the mixing arms, to the mixing shaft. This vacuum- and pressure-tight vessel is ideal for mixing and drying processes as well as for reacting.
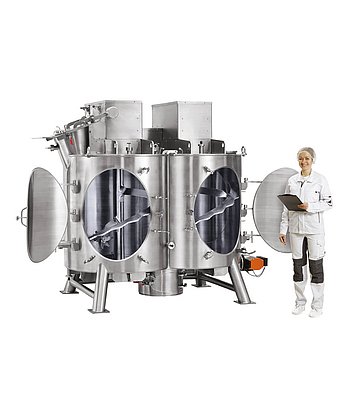
Vertical Twin Shaft Mixer HM
Blend uniformity is key in pharmaceutical production, as under- or over-concentrations of active ingredients can severely impact the safety and/or efficacy of a medication. The vertical twin-shaft mixer HM from amixon® is an ideal pharmaceutical powder mixer in this regard, making it possible to gently and precisely blend ingredients of varying sizes and shapes in record time.
The twin-shaft mixer HM offers unique advantages over more basic mixing machines, including ease of operation, quick and thorough cleaning, and a wide-range of processing capabilities. The mixer consists of two conjoined vessels, each outfitted with a helical mixing blade. The dual mixing shafts rotate simultaneously, generating a powerful three-dimensional current within the dry ingredients.
In as few as 20 to 90 rotations, the contents of the vessel have achieved a homogeneity that is virtually impossible to improve. The mixing process is at once gentle and energy efficient, creating homogenous, dust-free pharmaceutical blends with ideal dispersibility, wettability, and solubility.
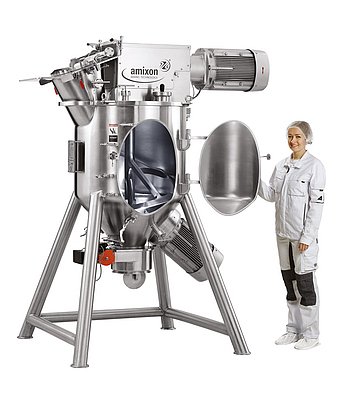
Conical Ribbon Blender AM
Excellent results in short mixing cycles: the AM conical ribbon blender is a versatile powder mixing machine with a number of key features ideal for medication manufacturing. The mixing vessel is free of dead space, making it operable at filling levels as low as 5%.
The helical ribbon blade generates a three-dimensional current within the mixing goods, conveying the particles upwards along the periphery and downwards along the center.
Shovel-like mixing arms comb through the powders, creating additional radial flows within the mixing goods. Regardless of the flowability characteristics of the initial ingredients, the AM ribbon blender can create an ideal mixing flow using minimal energy input.