Powder processing equipment for 3D printing materials
Mixing, vacuum drying, and reacting equipment plays a crucial role in the production and reconditioning of materials for powder-based 3D printing. In order to 3D print durable, high-performance components for industry, metal powders must have a narrow particle size distribution and excellent rheology and morphology.
In order to condition these sensitive materials, producers of metal powders for additive manufacturing require sophisticated processing technology. 3-in-1 powder mixers, reactors, and vacuum dryers from amixon® can perform all necessary conditioning processes in a single machine, helping to reduce processing time and hinder material degradation.
Powder bed fusion calls for high-quality powders
The quality of the powders used in powder bed fusion is key in ensuring the 3D printing process goes smoothly and that the finished product performs as intended. Especially in critical applications, ceramic and metal powders for PBF must meet specific standards as to their physical and chemical properties:
- High flowability & spreadability - for quick and precise dispensing with minimal force needed for even distribution.
- Free of agglomerates & cohesion - material fines are highly hygroscopic. Clumps in the powders can lead to significant quality issues in the 3D-printed component.
- Chemically stable - atmospheric moisture, oxidation, and heat from mixing or conveyance can cause premature or inadequate fusion.
- Additive blend uniformity - extremely light and sensitive coating and flow additives must be homogeneously integrated.
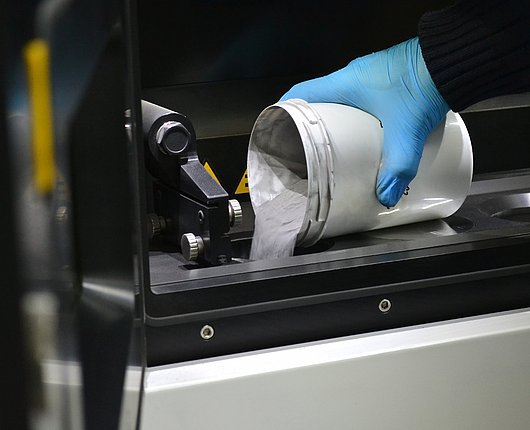
High-performance mixers for metal powder conditioning
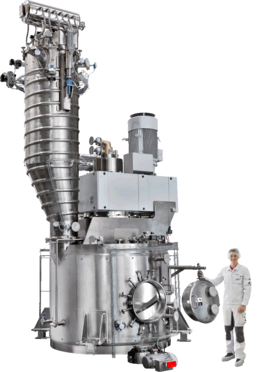
amixon® 3-in-1 mixers, reactors, and vacuum dryers excel in challenging applications like metal powder production for 3D printing. The following specifications make amixon®mixers ideal for cost-effective metal powder processing:
- Complete discharge without segregation - The innovative design of the mixing chamber enables discharge up to 99.997%, increasing batch yields by ensuring no valuable material fines are left behind. Furthermore, complete discharging helps to reliably separate each batch in order to avoid the intermixing of powders with different particle sizes.
- Gentle yet thorough deagglomeration and homogenization - Agglomerates are eliminated at a low rotary frequency by means of a vertically-mounted helical mixing blade and deadspace-free mixing chamber. As a vacuum- and pressure-tight operation, oxygen and nitrogen levels within the finished powders can be significantly reduced.
- Uniform integration of flow additives - A three-dimensional mixing current envelopes nanoscopic flow additives, homogeneously integrating them into the bulk powders. Innovative discharging mechanisms ensure no segregation after mixing.
- Multi-step processes for particle coating - A range of processing functions makes it possible to wet, coat, dry, and mix metal powders in the same device. The pressurized mixing vessel reduces both the processing time and the heat necessary to achieve the desired results.
Learn more about amixon® mixers & 3D printing powders
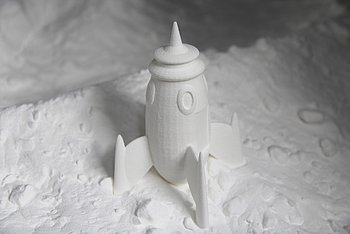
Powder processing for additive manufacturing with plastic, ceramic, and metallic materials
Read about the unique challenges of powder processing for additive manufacturing in this technical article from Diploma Engineer Ludger Hilleke, Technical Lead at amixon GmbH.
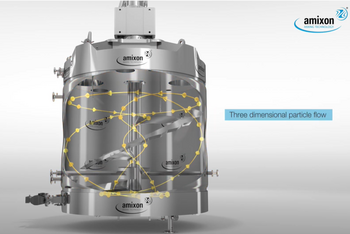
See amixon® 3-in-1 mixers, reactors, and vacuum dryers in action
Get a peek inside the mixing chamber, where a three-dimensional current is generated to gently yet thoroughly homogenize the mixing goods. All contact surfaces are heatable.
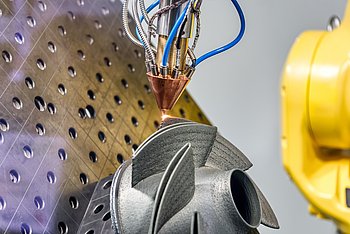
Mixing equipment and the economics of powder production for 3D printing
The latest whitepaper from amixon GmbH examines common obstacles to cost-effective 3D printing via powder bed fusion, and explores how sophisticated mixing technology can bring down the price for both powder producers and end-users.