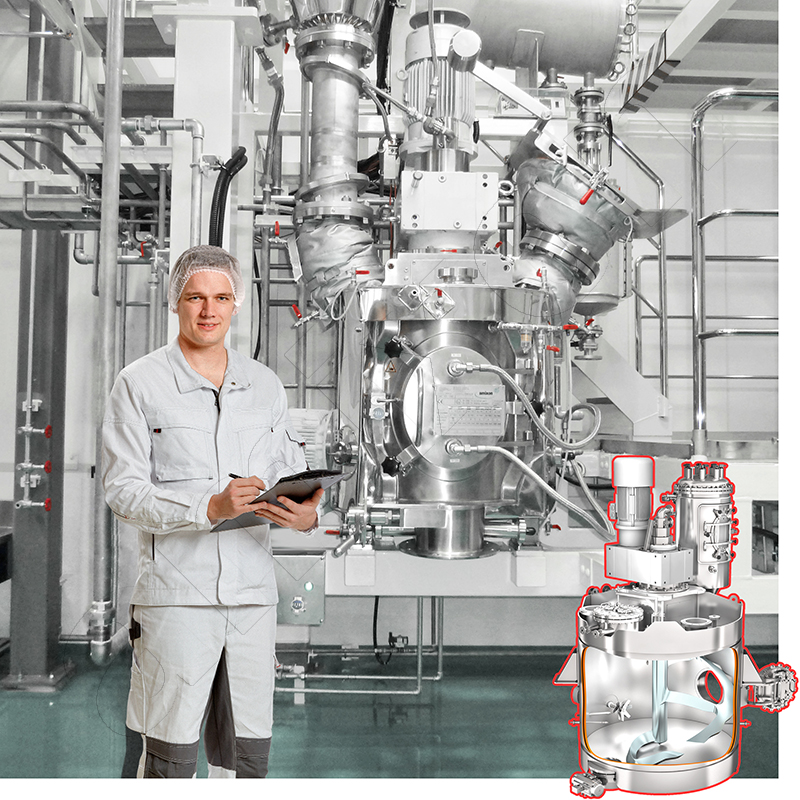
Qualifying
Qualification of a powder mixer in galenics
Consumer rights are generally monitored at national level. This is to ensure that only products that do not pose a risk are placed on the market. In addition, the consumer should also be protected to the extent that declared active ingredients are actually contained. And in the declared quantity.
The powder mixing plants are subject to quality audits. These differ depending on the product category: chemicals, foodstuffs, food supplements, active pharmaceutical ingredients.
The qualification process covers all key aspects:
- Personnel
- Incident management
- Ventilation and air conditioning
- Machines and systems
- Process control systems and controls
- Raw materials
- Auxiliary and operating materials
- Cleaning processes
- Documentation
- Data backup
Example:
In the pharmaceutical industry, uniform distribution of the active ingredients in the individual tablet is important. To achieve this, not only must the mixer be tested for suitability, but also the entire production process, the particle size distribution and the dispersibility/dispersibility of all individual components. Ultimately, it must be proven that the active ingredients do not decompose or change.
Powder mixers are used to evenly distribute the components involved in the formulation. As a rule, these are dispersed solids. However, they may also contain liquid components. These must also be evenly distributed at the end of the mixing process.
A rough preliminary assessment for the certification of the mixing process can be carried out with mixing quality tests.
With the help of mixing quality tests, small components can be quantified if samples of the same size are taken at different points in the mixing chamber.
Creation of a mixing quality curve.
The mean value of the concentration is determined by the composition of the mix. However, it should be confirmed by analysing the samples.
If the mixing process of a new powder mixer is to be evaluated, the following procedure has proved successful: A mix composition of 1:100,000 is defined.
99.999 kg of a powdery mixture is filled into the mixer. One gram of a small, analytically easily detectable component is added. The small component is present as a deagglomerated, dry and nanostructured powder.
A period of time is estimated in which the mixer has achieved the best possible mixing result with a high probability. This period is divided into 10 equal time periods. Each of these time periods represents a stopping point at which the mixer is stopped.
Samples of the same size are taken from 10 different points in the mixing chamber. At the end of the experiment, 100 samples of the same size are available. The mean value represents the ideal case of absolute uniform distribution. The scattering range refers to the analysis results distributed around the mean value.
The standard deviation is statistically more meaningful than the spread. The square of the standard deviation is calculated by squaring the deviations from the mean value. These values are totalled for each breakpoint and divided by the number of 10 samples.
In this case, the mixing time is plotted on the abscissa and the standard deviation on the ordinate. In this way, a "mixing quality curve" is obtained.
Ideally, the plotted points will stabilise around a technically ideal mixing quality. The more measurement results available, the more reliable the statements on the mixing quality. The smaller the individual samples, the greater the scatter range. In the pharmaceutical industry, for example, half of a single tablet can be taken as a sample quantity.