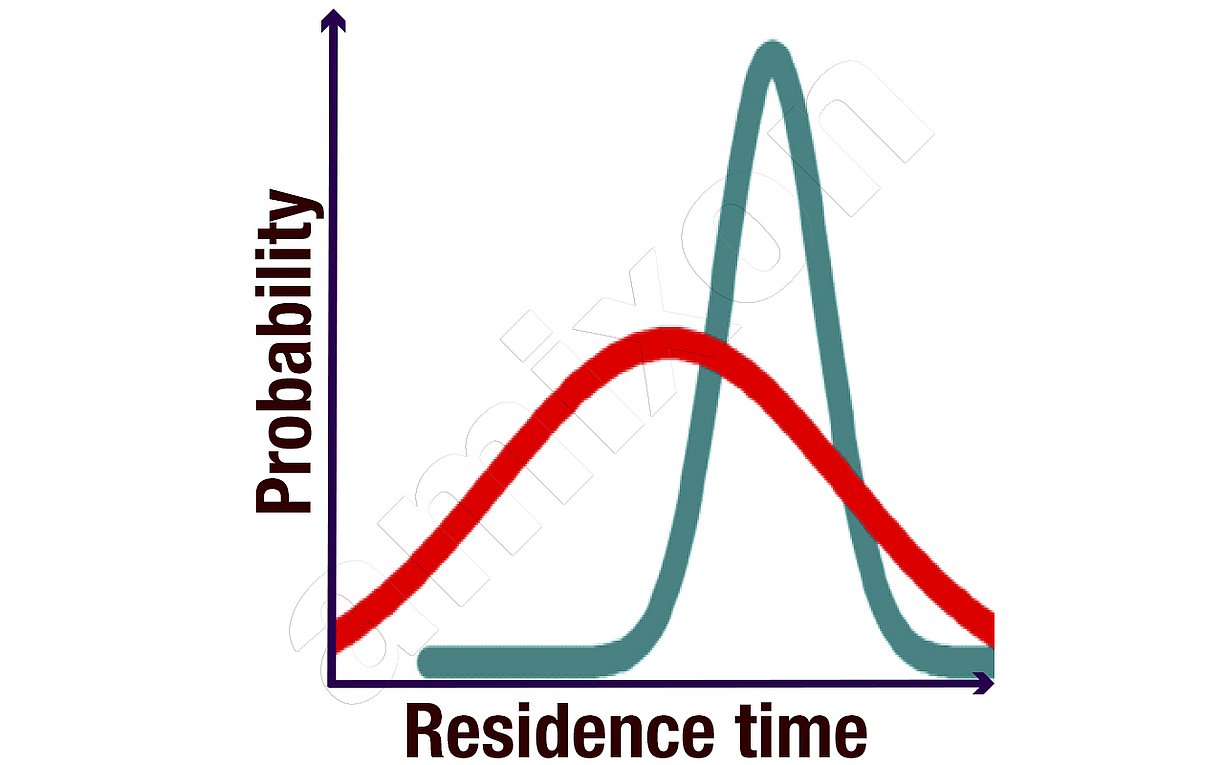
Sur le schéma, la ligne rouge représente la durée de séjour des mélanges dans le cas d’un flux dans une cuve, et la ligne verte, dans le cas d’un flux dans un tube.
Excursus : Mélange de poudres en continu : Flux de tube vs flux de cuve
Dans le secteur industriel, les produits en poudre sont mélangés et mouillés soit par lots, soit en continu.
Dans l'industrie, le mélange de produits en vrac s'effectue par lots ou en continu. Le "mélange" est ici un terme générique désignant une multitude de procédés annexes tels que la désagglomération, le broyage, la coloration, le désengorgement, l'enrobage, le mouillage des liquides, l'agglomération, le tempérage, le mélange-séchage, la réaction de synthèse, le bonding, ....
Veuillez également lire notre article de blog : "Mélange en continu versus mélange par lots" !
Pour le mélange en continu de produits en vrac/la préparation de poudres, on distingue le flux tubulaire et le flux en cuve. Dans la pratique, il existe également des formes mixtes de ces deux procédés.
Flux dans le tube
Si le mélange s’effectue sous la forme d’un flux dans un tube, les composants introduits en continu sont transportés de droite à gauche. Les outils de mélange transportent et brassent le mélange selon le principe « ce qui entre en premier sort en premier ». L’effet de mélange s’intensifie lorsque les outils individuels se déplacent dans le sens contraire au flux. En conséquence, le niveau de remplissage augmente. Plus le refoulement est important, plus la durée de séjour est longue. L’augmentation du refoulement entraîne également une augmentation de la consommation énergétique.
Flux dans la cuve
Dans le cas d’un flux continu dans cuve, le sens principal du flux est déterminé par la gravité. Un outil de mélange hélicoïdal répartit très efficacement le mélange en le transportant vers le haut. Après seulement huit tours, le mélange obtenu est déjà de très haute qualité. Les composants des matières premières sont dosés en continu dans la cuve de mélange par le haut et s’écoulent sur le lit de mélange totalement homogénéisé. Ceux-ci sont répartis aléatoirement dans la cuve de mélange. Un niveau de remplissage constant de la cuve de mélange doit être défini. Il peut être compris, par exemple, entre 40 % et 80 %. Dans ce contexte, la notion de flux dans la cuve suppose que presque tous les composants sont présents de manière homogénéisée dans la cuve de mélange. Les composants des matières premières sont ajoutés en continu. Ils sont ajoutés dans les bonnes proportions et leur débit volumique est relativement faible. Le mélange est si efficace qu’il devient homogène dans la cuve de mélange après quelques secondes.
Question d’un client : Quel type de mélange en continu faut-il préférer dans industrie de la transformation des matériaux en vrac : le flux dans le tube ou dans la cuve ?
Réponse d’amixon® : Il n’y a pas de réponse universelle à cette question. Les deux systèmes présentent des avantages distincts. Le choix du système dépend donc de l’application.
Il faut toujours privilégier le flux dans le tube :
- lorsque le processus de préparation présente des contraintes de temps, comme en cas de thermorégulation rapide, de granulation par accumulation, d’enrobage, ou lorsque les composants doivent produire une réaction chimique spontanée ;
- lorsque les substances sont peu miscibles, en particulier lorsqu’une désagglomération intensive doit être effectuée pendant le mélange, ou si les additifs liquides sont très visqueux ou bien adhérents ;
- lorsque l’espace vertical disponible est réduit ;
- lorsque les additifs doivent être mélangés l’un après l’autre le long de la chambre de mélange, ce qui peut être le cas si les particules du mélange doivent être enrobées de différentes substances les unes après les autres ;
- etc.
Il faut privilégier le flux dans la cuve :
- lorsque les pertes initiales doivent être évitées lors du démarrage de l’installation de mélange. Les premiers grammes du produit mélangé doivent être homogènes, conformément aux spécifications ;
- lorsque le mélangeur doit compenser au mieux les erreurs de dosage à court terme ;
- lorsque le processus de mélange doit être particulièrement doux ;
- lorsqu’une plus grande durée de séjour est souhaitée ;
- lorsque le même mélangeur doit homogénéiser à la fois de grands et de très petits débits volumiques ;
- lorsque le même mélangeur doit également être utilisé comme mélangeur de lots de précision. Par exemple, le mélangeur conique amixon® peut produire à partir de nombreux petits composants un prémélange qui est ensuite mélangé en continu avec d’autres composants dans ce même mélangeur ;
- etc.
La société amixon GmbH peut réaliser confortablement pour vous les procédés de mélange en continu présentés ci-dessus. Venez nous rendre visite avec vos produits dans notre centre technique de Paderborn. Nous vous ferons volontiers une démonstration des procédés de mélange !
© Copyright by amixon GmbH