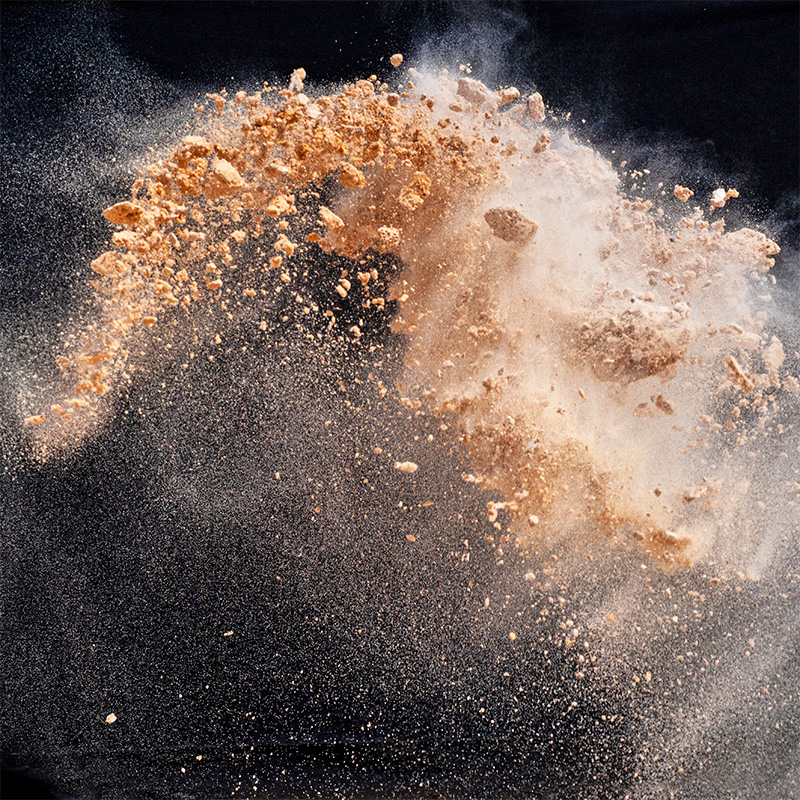
Here amixon® explains that the appearance and behavior of the individual particles can be changed depending on the type of mixing process.
Powder mixing and accompanying procedures
The process technology of ‘powder mixing’ is always associated with a wide range of side/concomitant effects. This can be seen under the microscope when examining the individual mixture particles. Certain side effects are often desirable. In this case, the mixing system and process must be well coordinated. Sometimes side effects are undesirable. In this case, gentle mixing is advisable.
The side operations/side effects are referred to differently in some industries, although the basic physical operation is identical. The design of the mixing system and the mode of operation are decisive for the type of side effects.
amixon® manufactures a wide variety of vertical precision powder mixers for almost all industries. amixon® is ideally placed to produce or eliminate the side effects desired by the customer.
amixon® manufactures a unique portfolio of a wide variety of precision mixers/vacuum mixer dryers and synthesis reactors. More than 30 amixon® devices are available for testing. Our process devices achieve top performance across all industries – worldwide!
Basic process powder mixing
The mixing of powders is a basic operation that has been practised since time immemorial. One is inclined to view powder mixing as a trivial operation. On closer inspection, however, one realises that many accompanying effects occur simultaneously and even in opposite directions during powder mixing, such as
- deagglomeration
- spherisation
- grinding
- wetting
- encapsulation
- separation
- agglomeration,
- drying
- reaction
- crystallisation
The process engineering objectives of the InfoCube are of varying importance in the different industries:
- In the pharmaceutical industry, the focus is on the synthesis of active ingredients and vacuum drying.
- In powder galenics, crushing and agglomeration are important.
- In the food industry, flexibility and hygiene are important, but above all gentle mixing.
- In the fine chemicals and plastics industries, it is important to control the reaction environment during synthesis.
- Powder metallurgy: Nanoparticles are often used as coating substances and must completely envelop the active ingredient particles.
Some processes are carried out in batches, others continuously. However, all types of mixers from the amixon® production line are used across all industries.
Process parameters and preparation steps
At the end of a mixing process, the result should be a homogeneous powder mixture that meets the expectations. With the help of the process parameters named below, the targeted processing step can be navigated:
- Material composition/recipe
- promoting or avoiding particulate interactions (chemical, physical)
- particle sizes
- temperature
- presence of liquid substances
- method of liquid injection
- pressure level
- type of flow generation
- sequence and timing for the addition of ingredients
- turbulence intensity of mixing
- mixing time
- .... many more
KoneSlid® Mixer
Powder blending and accompanying processes are important topics in the production of pharmaceuticals, nutrients, active chemical ingredients and high-performance materials. With trials in the amixon® technical center, we make valuable contributions to your problem solutions.
amixon® can help you save time and money. Forty years ago we started to manufacture vertical spiral mixers. Since then, we have established amixon® helical mixers with vertical mixer shafts in almost every industry. amixon® is a trendsetter in this sector. In addition, amixon® process machines are trendsetters in the following areas
- ideal mixing qualities
- gentle mixing
- residue-free emptying
- trend-setting sanitary design
Discharge takes only a few seconds
Ideal mixing qualities are achieved very quickly in the KoneSlid® mixer. Then the conically shaped closing element moves downwards. Free-flowing mixing goods are completely discharged within a few seconds. The degree of discharge is almost 100%.
This discharge fitting is permanently gas-tight. It can also be used as a dosing device. The tests at the amixontest center explain many details better than a written text.
© Copyright by amixon GmbH