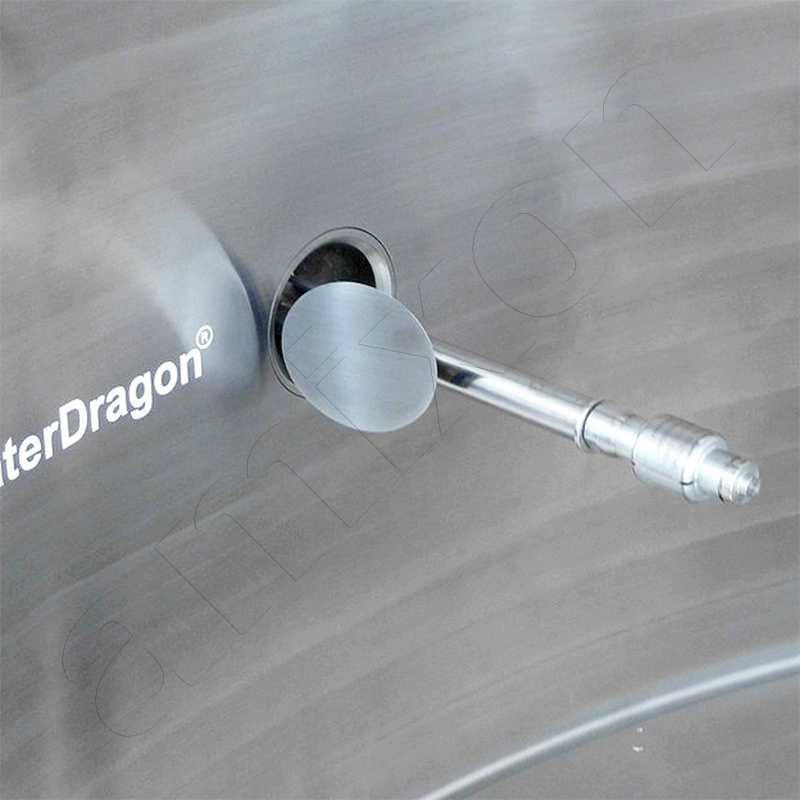
Automatic wet cleaning
Automatic wet cleaning of powder blenders/ mixers, synthesis reactors and vacuum mixer dryers.
Cleaning, especially wet cleaning, is considered an unproductive interruption of the production process. It usually ties up human resources and is therefore expensive. On the other hand, inadequately cleaned processing equipment can endanger human life and destroy manufactured goods. Wet cleaning of a production plant for powdery goods requires a hygienic design of the process equipment. The recommendations and guidelines of GMP, FDA and EHEDG should ideally be implemented.
The challenges are:
- Safe cleaning.
- Safe drying.
- Minimal manpower.
- Automated documentation.
- Fastest possible release for production.
Often, plant components have to be dismantled or opened to allow an automatic wet cleaning to be carried out. For example, it is essential to dismantle textile dust filters beforehand, as only metallic dust filters can be wet-cleaned. Before starting the wet cleaning, the clean gas side of a dust filter must be disconnected from the air handling systems of the building. Simple shut-off valves or slides are not sufficient under any circumstances.
An automated wet cleaning system must have a comprehensive programme to be able to be used safely and economically. Typical questions are:
- Are there different degrees of contamination?
- Is the mixture critical to clean? (e.g. adherent, toxic, allergenic)
- Are there frequent product changes?
- Are there industry-specific requirements?
Mixers, dryers and synthesis reactors are usually large and heavy. Therefore, they can only be cleaned on site. Ideally, wet cleaning and drying should be carried out without dismantling any parts of the system. Washing and drying should be carried out in such a way that contamination of the area around the system with washing liquid is avoided.
A frequently asked question is: Can wet cleaning be done without active cleaning substances?
This is often the aim if the outgoing wash water can be measured online. The cleanliness of the system can be indirectly deduced from the purity of the wash water.
Many food companies successfully clean their equipment with only hot water. This is done in analogy to the ‘Siner's Circle’. The ‘Siner's Circle’ consists of 4 segments and states that the 4 influencing factors can compensate each other.
1) Presence of detergent surfactants, alkalis, acids.
2) Mechanical action of the wash water through flow, pressure and rinsing.
3) Temperature of the wash water up to 85 °C.
4) Duration of the washing process.
WaterDragon®
amixon® has developed a cleaning system called WaterDragon®. It opens into the mixing chamber. Then a lance moves from the outside into the mixing chamber. Three nozzles rotate and the wash water sprays to the back, to the front and to the side. Then drying takes place with the help of large quantities of warm air. After that, all water-carrying parts move back into the housing. Then the system closes hermetically.
WaterDragon® can seal the mixing chamber tightly. It remains sealed even under negative pressure in the mixing chamber. It remains sealed even under overpressure in the mixing chamber. It is also self-draining. After wet cleaning and drying, the housing is also clean and dry.