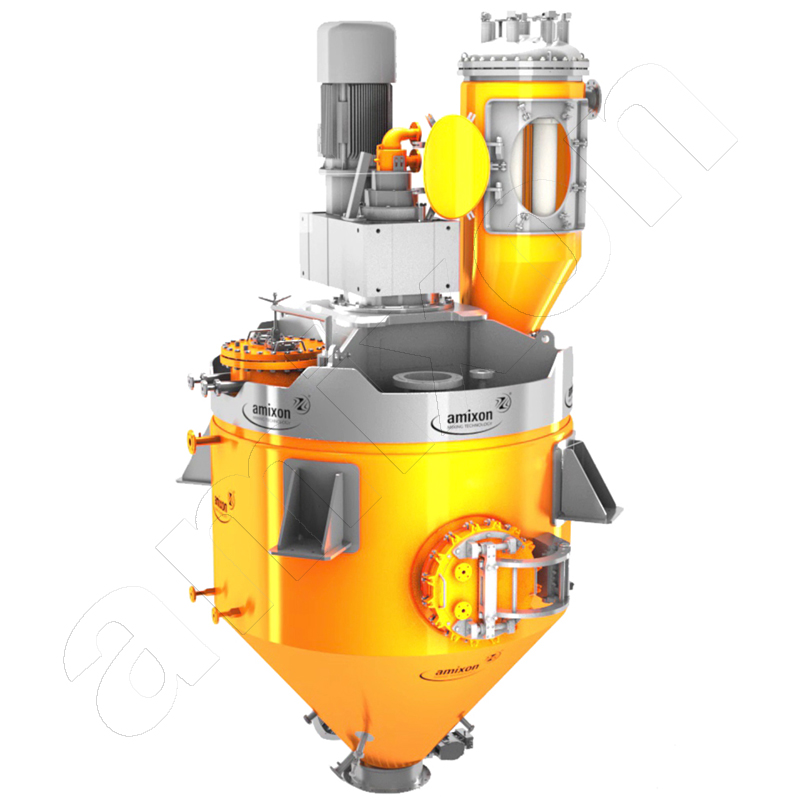
amixon® helps with the dimensioning of large vacuum mixer dryer systems
amixon® vacuum mixing dryers and synthesis reactors are used for almost all types of bulk solids and suspensions. Due to the large specific heat transfer surfaces, amixon® devices are also used as evaporators.
The compact amixon® vacuum dryers are characterized by the following properties:
- outstanding energy efficiency
- very gentle product movement
- large specific heat transfer surface
- very high drying speed
- gentle drying due to targeted vacuum setting
- ideal mixing quality
- particularly hygienic design
- amixon® apparatuses are also used as sterile reactors in the biochemical and pharmaceutical industries.
How can amixon® help with the transfer of laboratory results to technical scale?
When new products or processes are developed, questions of technical implementation must be examined in parallel. Scaling up from a test tube to an industrial plant is not trivial.
The pilot plant is used to define process parameters that lead to similarly good results as those previously achieved by the researchers in the test tube.
amixon® is a manufacturer of process engineering systems and has its own pilot plants. The systems there are fully functional. They are dimensioned in such a way that they can be used to design large-scale industrial plants.
Practically all bulk material mixing/refining and vacuum drying processes can be demonstrated with amixon® in the technical center. The pressure in the mixing chamber can be varied from 5 mbar to 26 bar (absolute pressure). The temperature can be varied from sub-zero to 350°C.
This allows customers to quickly find out how well and quickly a synthesis reaction or vacuum drying process works with their product.
How do you extrapolate from a pilot plant to a large-scale plant?
Difficulties arise when the industrial plant to be set up is 100 times larger than the process machine in the pilot plant. For thermokinetic issues, geometric similarity considerations fail. Practical know-how in the application of thermodynamic calculations helps here.
amixon® helps with extrapolation to process machines that are many times larger than the test plant. The accuracy of our calculation methods has been proven time and time again by amixon®. Namely, whenever the large-scale system in the industrial environment achieves or exceeds the calculated performance.
amixon® is happy to invite customers from near and far to take part in trials and promises them very good results in advance. We can do this thanks to decades of experience.
Drying tests in the amixon® technical center are always target-oriented and provide a high level of knowledge. amixon® protects the information shared with you from third parties. This means that the exchange of information always remains confidential.
Drying tests differ from classic mixing tests. The process time is considerably longer. A lot of data is recorded during the drying process in the amixon® technical center. This is largely automated.
This leaves enough time to discuss constructive details. A detailed factory tour should always take place. Some customers use the time to carry out mixing tests for the subsequent process. Others use the time for agglomeration tests.
How can the flow of powders in an amixon® vertical mixer be calculated?
amixon® mixers mix three-dimensionally and produce ideal mixing qualities that cannot be improved in practice. This is achieved by the mixing spiral conveying the mix upwards without any dead space and gravity allowing the mix to flow downwards. The product currentIv can be described approximately as follows.
Iv: Conveying capacity of a vertical mixing spiral
D/ d: Outer/inner diameter of the spiral
φ: Filling degree
S: Pitch of the spiral
n: Rotational frequency
ζ: Speed coefficient
In this respect, the specific mixing capacity of amixon® mixers is always the same regardless of the size, provided that the geometric ratios are congruent.
amixon® has various synthesis reactors/vacuum mixing dryers in Paderborn. Some have a conical mixing chamber. Some have a flat bottom.
Are there any special features of processes that take place at high temperatures and high pressures?
Tests can also be carried out under extreme process conditions in the amixon® technical center:
- System pressure in the process area up to 25 bar overpressure: The thicker container walls influence the heat transfer. On the other hand, the temperatures in the process area can be changed extremely quickly by changing the system pressure. If the system pressure in the process area is increased, gas-solid reactions, for example, can be favoured. For example, diffusion processes ....
- Heating up to 350°C: Conventional polymer seals fail when temperatures permanently exceed 240 °C. Then only metallic sealing systems or graphite gaskets can be used.
- Fine vacuum of 1 mbar absolute: Such absolute pressure requires the apparatus and all communicating connecting lines to be extremely tight. This applies in particular to the sealing of the agitator shaft.
How can the process of vacuum mixed drying be illustrated?
The drying process of a test run can be represented as a diagram as shown here. The time is plotted on the abscissa. Various physical quantities are plotted on the ordinate axis:
- the system pressure in the process chamber,
- the mass of the evaporated liquid,
- the temperature of the mass to be dried and
- the temperatures of the heat transfer medium in the flow and return.
The vacuum mixed dryer is usually filled with the maximum batch volume before the drying process begins. As a rule, the volume of the mixture decreases as drying progresses.
In rare cases, the filling volume remains constant, although the mix becomes drier and lighter. In very rare exceptional cases, there may even be an increase in volume during drying. This increase in volume must be taken into account, as the mixers/dryers must not be overfilled.
How does the heat transfer surface change as the filling level decreases?
The heat transfer surface of the vacuum dryer changes with the fill level. In this case, the mixing chamber consists of a cone with an attached cylinder. In the following derivation, the heat transfer surface is calculated for the case that the filling volume is smaller than the conical part of the mixer dryer. First, the filling height hFK in the cone is calculated:
The heat-transferring surface in the AFcone is only the surface that is in contact with the mix.
If the filling level in the mixing dryer changes during the drying process, the contact surface of the tempered mixing tool also changes. This situation cannot be described as a closed function. amixon® measures the heat exchange surface of the mixing tool in the CAD system for different filling levels. The data is recorded in tabular form and interpolated.
How high is the heat requirement if the vacuum mixed dryer is significantly larger than the test system?
Two indices are introduced below: "R" (reference) for the pilot plant and "T" (target) for the industrial-scale plant. The drying time is the time from the start of evaporation to the end of evaporation. The following idealized conditions are assumed:
- The process conditions in the tester are identical to the process conditions in the large appliance.
- Evaporation takes place at a constant temperature.
- Evaporation takes place at a constant system pressure.
- The heat transfer coefficient is the same in both apparatuses.
- The average temperature difference between the heating medium and the mix is the same.
The heat flow QR of the test system can be determined from the enthalpy of vaporization hv at saturation pressureps. The heat flow through the heated contact surfaceAT of the large dryer can thus be calculated as follows.
How long does the drying process take in the large-scale plant?
Assuming that the density rho of the moist product in the reference plant and in the large-scale plant is the same, the mass of the product in the large-scale plant can be calculated if the filling level PHI is known.
The mass mT to be evaporated in the large-scale plant is fT1 at the end and fT2 at the beginning of the drying process.
The drying time in the large-scale system is then
How large should the heating system for the large dryer be?
The following diagram shows the individual consumption points. Each consumer must be sufficiently supplied with the extrapolated thermal energy. The design factor S is used to calculate the heat flow in the heating system. This is based on the heat flow Qvap required for evaporation.
The mass flow of the heat transfer medium Qvap results from the specific heat capacity cp, the inlet temperature of the heat transfer medium T1,heat and the outlet temperature of the heat transfer medium T2,heat. The thermal fluid must be distributed in such a way that all consumers are adequately supplied. This means that all areas of the process chamber must be heated evenly. Condensation must be avoided. The wet goods must be heated to the extent that steam energy is dissipated. The temperature of the mix corresponds to the evaporation temperature of the applied vacuum.
How large should the vapor filter for the large dryer be?
Estimation of the required filter area based on the permissible filter load fs
With the volume flow dV/dt, the mass flow dm/dt and the density ro of the steam.
The velocity of the dust-laden raw gas v is
The filter surface load fs is defined in the unit [m³/h/m²].
How large should the condenser for the large dryer be?
The vaporized vapour is cleaned in the vapour filter and liquefied in the condenser. The heat flow Qkond must be dissipated. The cooled condensation surface Akond is used for this purpose.
The mass flow of the cooling medium mcool is calculated taking into account the heat transfer coefficient and the mean temperature difference:
When determining the K value, the design of the capacitor and the expected fouling factor must be taken into account.
A straight line idealises the mass flow of the condensate.
What is the intention when the measured condensate mass flow is averaged by a straight line? This rough approximation allows a comparison with a continuously operated parallel flow heat exchanger. The effects of changing process parameters can be calculated with a very good approximation..
How long does the drying process take in the large-scale system if the temperature of the thermal fluid is changed?
.... if the drying system is operated with a warmer or colder heat transfer medium. This consideration is analogous to the operation of a parallel flow heat exchanger:
T2,heat can only be iterated numerically.
This allows an interesting curve to be approximated. It makes it possible to estimate the drying times at different temperatures of the heat transfer medium.
Why does it take longer to cool down dry powder than to heat up wet powder?
When estimating the DELTA tT cooling time, it is assumed that the same conditions prevail in the test facility and in the large dryer. This applies both to the heat transfer coefficient and to the mean temperature difference between the heat transfer medium and the product temperature.
The product in the large-scale plant is to be cooled to the same final temperature as was tested in the pilot plant.
What is striking about the mix cooling in this diagram?
A typical cooling curve is shown below. The cooling of dry powder takes longer than the heating of wet powder. There are two explanations for this:
- A liquid conducts heat much better than most solids.
- The liquid film surrounding a moist particle can wet the heat transfer surface. This promotes heat transfer. In contrast, a dry particle only touches the tempered surface at a few points.
In this case, the dryer was heated with a very high temperature difference. The thermal oil was initially approx. 120°C hot. In this case, the entire thermal oil storage tank must first be cooled in the system flow. This results in the cooling of the drying powder with a pronounced hysteresis.
If water were used as the heat transfer medium, the cooling process would be accelerated.
© Copyright by amixon GmbH