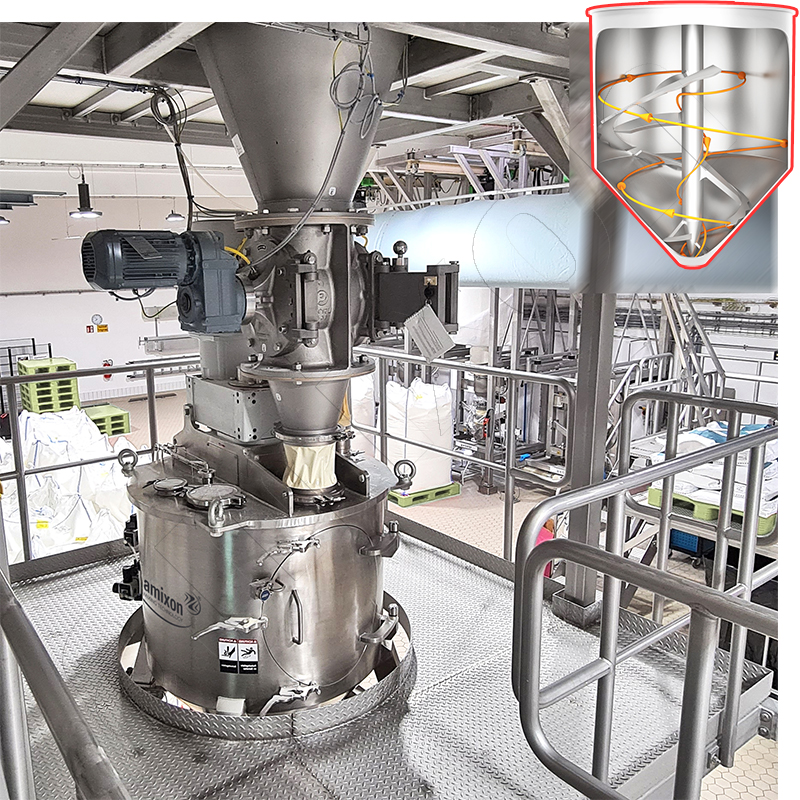
Continuous mixer, flow through mixer, online mixer
Continuous mixing processes always work well when only a few components are involved in the mixing process and when the component composition is always the same. For example, when a bulk material is to be wetted for the purpose of dust binding. This can be ash from waste incineration, it can be a feed, it can be building materials that are dyed, it can also be detergents. If bulk materials are to be agglomerated, then the classic "build-up granulation" is carried out. For this purpose, amixon® can offer the ring-layer mixing granulator RMG. Such processes also take place in the continuous mixer. The achievable mixing quality is directly related to the accuracy of the dosing. Occasionally, continuous mixers are even used for pharmaceutical products. In this case, the flow mixers are arranged above tablet presses, for example.
In most cases, continuous mixers bear a strong resemblance to horizontal screw conveyors. They are fed with the individual components on one side (from above). On the other side, they discharge the mixed goods (downwards). In principle, mixing takes place in the pipe flow.
More rarely, there are continuous bulk material mixers that work according to the principle of continuous boiler flow. amixon® offers such a system. They bear the designation amixon® AMK. The advantages and disadvantages of the two systems are discussed in the amixon blog. The most important features of the amixon® continuous mixers are:
- There is no product loss during start-up
- There is no product loss at the end
- The mixer can discharge free-flowing powders completely
- The same mixer can be used as a precision batch mixer.
Advantages of continuous mixing systems:
- Small mixers can mix very large volume flows
- The mixers are relatively simple and inexpensive
- High reliability
- Cost-effective operation
Disadvantages of continuous mixing systems:
- The dosing systems are relatively expensive. Continuous dosing should be gravimetric - controlled if high mixing qualities are required
- In most cases there are start-up losses when the mixing process starts
- In most cases, the continuous mixer cannot empty completely.
- If the dosing system makes a mistake, then the mistake can usually not be repaired. The incorrectly mixed products must be destroyed.
Mixing systems from amixon® can also be integrated into continuous production processes. The mixing intensity of these systems is adjustable: Depending on the specific task, the products can be both gently homogenised and intensively deagglomerated. The dwell time is independent of the mixing tool rotation frequency; the degree of filling can be set in a wide range from 10 % to 80 % of the useful content. The process equipment is used in the food or chemical industry.