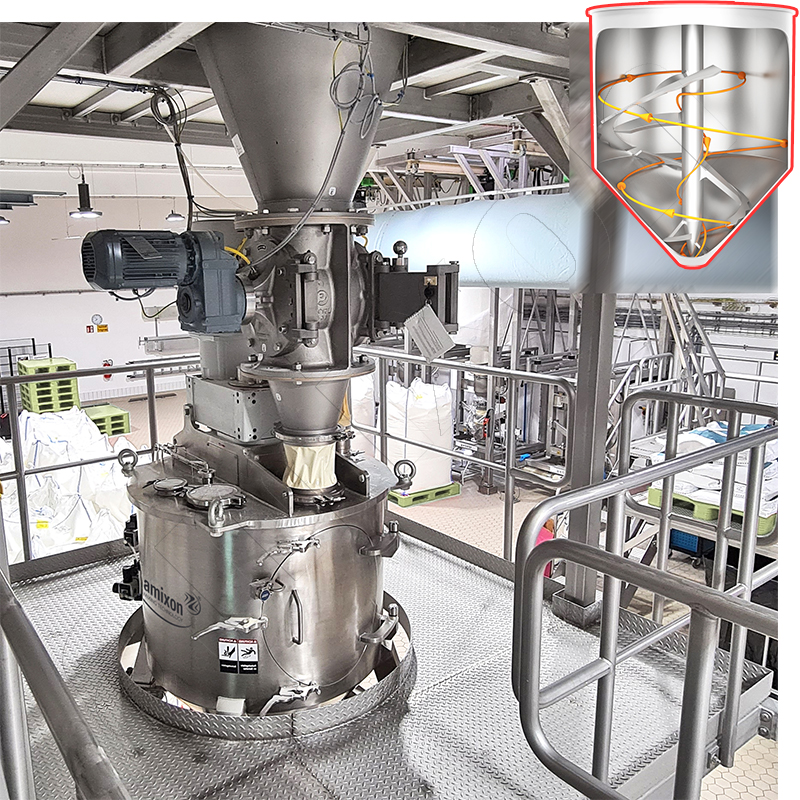
연속 믹서
다른 명칭으로는 연속 믹서 또는 플로우 믹서 또는 온라인 믹서가 있습니다. 연속 믹서 또는 플로우 믹서는 거의 항상 연속 작동에 사용됩니다. 연속 믹서는 상대적으로 크기가 작습니다. 그러나 많은 양의 흐름을 혼합할 수 있습니다. 플로우 믹서는 정밀한 도징 시스템이 필요합니다. 도징 시스템이 잘못 작동하면 이미 얼마나 많은 믹스가 잘못 생산되었는지 파악하기 어렵습니다.
연속 혼합 공정은 혼합 공정에 몇 가지 성분만 관여하고 성분의 구성이 항상 동일한 경우 항상 잘 작동합니다. 예를 들어, 먼지 결합을 목적으로 벌크 재료를 적셔야 하는 경우입니다. 폐기물 소각 재, 동물 사료, 착색된 건축 자재, 세제 등이 이에 해당할 수 있습니다. 벌크 제품을 응집해야 하는 경우 고전적인 "빌드업 과립화"가 수행됩니다. 이를 위해 amixon®은 RMG 링 레이어 혼합 과립기를 제공할 수 있습니다. 이러한 공정은 연속 믹서에서도 이루어집니다. 달성 가능한 혼합 품질은 투약의 정확성과 직접적인 관련이 있습니다. 경우에 따라 연속 믹서는 제약 제품에도 사용됩니다. 이 경우 플로우 믹서는 예를 들어 정제 프레스 위에 배치됩니다.
대부분의 경우 연속 믹서는 수평 스크류 컨베이어와 매우 유사합니다. 한쪽(위에서부터)에서 개별 구성품이 공급됩니다. 다른 쪽에서는 혼합된 제품을 배출합니다(아래쪽). 원칙적으로 혼합은 파이프 흐름에서 이루어집니다.
드물게는 연속 용기 흐름 원리에 따라 작동하는 연속 벌크 재료 혼합기가 있습니다. amixon®은 이러한 시스템을 제공합니다. 이 시스템에는 amixon® AMK라는 명칭이 붙어 있습니다. 두 시스템의 장단점은 amixon 블로그에서 확인할 수 있습니다. amixon® 연속 믹서의 가장 중요한 특징은 다음과 같습니다.
- 시동 중 제품 손실이 없습니다.
- 마지막에 제품 손실이 없습니다.
- 믹서는 자유 유동 분말을 완전히 비울 수 있습니다.
- 동일한 믹서를 정밀 배치 믹서로 사용할 수 있습니다.
연속 혼합 시스템의 장점
- 소형 믹서는 매우 많은 양의 흐름을 혼합할 수 있습니다.
- 믹서는 비교적 간단하고 저렴합니다.
- 높은 신뢰성
- 비용 효율적인 운영
연속 혼합 시스템의 단점:
- 도징 시스템은 비교적 고가입니다. 높은 혼합 품질이 필요한 경우 연속 주입은 중량 측정으로 제어해야 합니다.
- 대부분의 경우, 혼합 공정이 시작될 때 시동 손실이 발생합니다.
- 대부분의 경우 연속 믹서가 완전히 비워지지 않습니다.
- 주입 시스템에 실수가 발생하면 일반적으로 오류를 복구할 수 없습니다. 잘못 혼합된 제품은 폐기해야 합니다.
amixon® 혼합 시스템은 연속 생산 공정에도 통합할 수 있습니다. 이러한 시스템의 혼합 강도는 조정할 수 있습니다: 특정 작업에 따라 제품을 부드럽게 균질화하거나 집중적으로 응집 제거할 수 있습니다. 체류 시간은 혼합 도구의 회전 빈도와 무관하며, 충전 레벨은 사용 가능한 내용물의 10%에서 80%까지 폭넓게 설정할 수 있습니다. 이 공정 장비는 식품 및 화학 산업에서 사용됩니다.