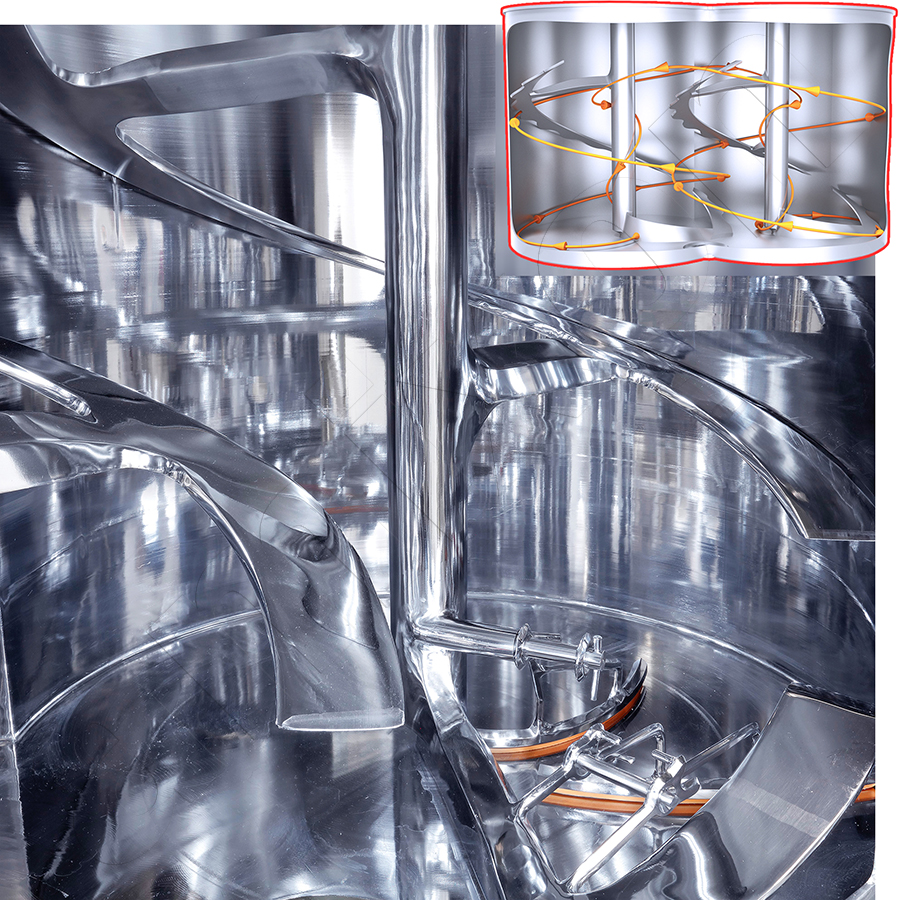
View inside an amixon® twin-shaft mixer.
Twin-shaft mixer from amixon® for baking agents, fat coatings and snack products
Single-shaft and twin-shaft vertical mixers have similar mixing properties. They can ideally and precisely homogenise almost all types of bulk materials. There is only one restriction: the end product must have sufficient flowability. If the end product (whether dusty, dry, moist or wet) can be poured out of a bucket, it can be discharged from the amixon® mixer.
Many users also employ amixon® mixers as vacuum mixing dryers or as synthesis reactors. In such processes, the mixtures can change. They can be as flowable as water or take on highly viscous properties. Such changes in consistency are not a problem if the mixtures are flowable again at the end of the process.
Coating process up 100%
Coating processes for bulk materials are generally challenging and require precise process control. The mixing tools of the mixer work at varying speeds. The liquids are added sequentially, and the mass flows and temperatures must be controlled very precisely.
Solidification hysteresis
Depending on the type of fat, the solidification hysteresis can vary. If suitable fats are cooled quickly (when warm), their viscosity increases only with a considerable delay. This hysteresis can be very useful. The fat coating of the mixture particles is conveniently done at low viscosities but reduced process temperatures.
Cryogenic cooling
After the fat has wetted all the powder particles, the mixture must be cooled as quickly as possible. This must be done during mixing. Unfortunately, cooling of powdery goods by contact heat transfer is much slower than with liquids. For this reason, cryogenic cooling is used.
Either liquid nitrogen (-196 °C) or carbon dioxide snow (-78 °C) is used. In special cases, cryogenic carbon dioxide in pellet form can be used. The feed systems should be well insulated. They must be protected against condensation/icing.
During the shock-like cooling, the flow behaviour of the mixture changes abruptly. The mixing tools and the drive must be designed for this.
Large amounts of gas are produced in the mixing chamber during cooling. These inert gases must be safely removed from the working environment of the personnel. The employees must be instructed about the hazards. Oxygen measuring devices continuously measure the oxygen content in the ambient air. If the oxygen content falls below a certain limit (e.g. below 19 vol.-% or 18 vol.-%), they trigger a visual and acoustic alarm. It may be necessary for personnel to wear cold-protection gloves.
Three-dimensional mixing
amixon® mixers achieve excellent results when it comes to wetting and coating. The function of the mixers is based on the helical mixing tools. They convey the product upwards at the periphery. The mixture then flows downwards in the centres of the mixing chamber. This results in an intensive cross-flow of the product flowing up and down.
This type of ‘vertical mixing’ can be used universally for almost all product consistencies: dry, moist or wet powders and even pastes and doughs. A three-dimensional random distribution is created.
- The mixing process works largely independently of the filling level,
- it works independently of the rotational frequency,
- it works independently of differing component properties such as
- particle size,
- particle shape,
- flow properties,
- liquid content,
- bulk density,
- cohesion,
- adhesion
- viscosity.
For particularly sensitive products or where there is a risk of dust explosion, it is advisable to reduce the speed of the mixing mechanism. amixon mixers can also be operated with slow-rotating mixing tools without any loss of quality.
Mixing tests at the amixon® technical centre
amixon® has more than 30 test mixing machines in Paderborn. This allows us to respond very specifically to customer requests. Mixing tests at the amixon® technical centre offer the user many advantages:
The knowledge gained from the tests ensures that scale-up considerations for large-scale plants are taken into account. This speeds up the commissioning process later on.
Tests provide information for constructive improvements to the large processing equipment. Sometimes events are interpreted differently by the customer than by the amixon® experts. This can increase the knowledge gained.
Well-documented test series provide valuable impetus for improvements to the subsequent process control in the large-scale plant.
© Copyright by amixon GmbH