6 Futuristic Applications of Powder-Based 3D Printing
These are the key advantages of using amixon® mixers in powder metallurgy. Plant managers report on their experiences ......
Maximum mixing precision – regardless of fill level and speed
- amixon® vertical spiral mixers quickly produce an ideal powder mixture, even at low speeds.
- The mixing quality remains constant, even when the mixer is only partially filled.
- An ‘ideal mixing quality’ means that a further improvement in the uniformity is not technically possible – regardless of the mixing time or other precision mixing systems.
Long service life and low maintenance
- due to the heavy and robust construction
- due to the relatively low speed
- due to the short mixing time
Hygienic design for maximum process reliability
- The spiral mixing tool is only supported and driven at the top, so that no shaft seals are required in the powder chamber.
- All components, including the dead-space-free shut-off valve, are easily visible and easy to clean.
- Large inspection doors with OmgaSeal® seals enable easy maintenance and guarantee a permanently gas-tight seal, even with minimal contact pressure.
Efficient emptying and contamination-free batches
- amixon® mixers enable almost complete emptying, thus avoiding cross-contamination between batches.
Flexible process adaptation with deagglomeration option
- Optionally, amixon® mixers can be equipped with rotor-stator systems or high-shear blades for aggressive deagglomeration and the targeted processing of fine powders.
3D-printed metal components are used in architecture, aerospace and medicine. High-performance components made using the powder bed fusion process are expensive. However, additive manufacturing processes can be cost-effective for small quantities.
Complex components made using the powder melting process
The additive manufacturing of metal parts makes economic sense when complex geometries are involved:
- free-form surfaces and organic structures
- cavities, lattice structures or internal channels (e.g. for cooling turbine blades)
- topology-optimised components with high strength and minimal weight
Additive manufacturing of metal components is also of interest when small quantities are required
- no reproduction moulds are available
- moulding tools are very expensive
- time is of the essence (repairs)
- only a digital drawing of the finished part is available
Powder metallurgy is the technological basis for additive manufacturing with metals. This includes, in particular, the processes for manufacturing metal powder by atomisation, condensation or milling. In contrast to sintered components, no mould is required for additive manufacturing.
The powder processing and mixing process, with its numerous accompanying processes, is crucial for the quality of the end product.
We show you 6 future application areas for 3D printing that will grow as the technology develops.
KoneSlid® mixer for powder metallurgy. 600 litres usable capacity. Extremely fast, gentle mixing and complete discharge - up to 100%.
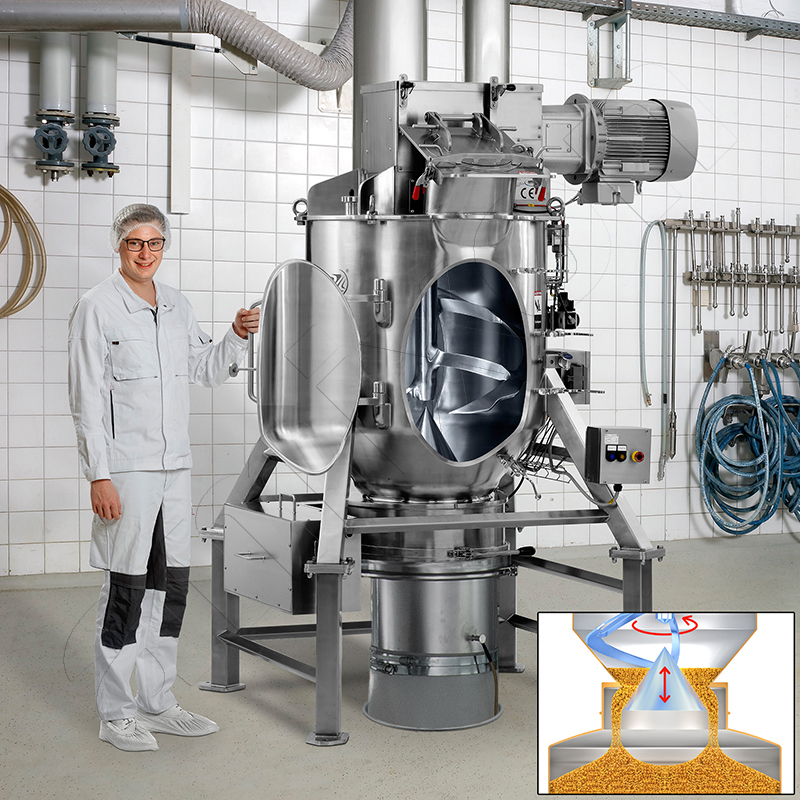
amixon® powder mixers/blenders for additive manufacturing and powder metallurgy
amixon® powder mixers meet the highest quality requirements in powder metallurgy and in additive manufacturing, particularly in the areas of
a) laser melting (LPBF - Laser Powder Bed Fusion)
b) laser deposition welding (DED - Directed Energy Deposition)
- Ideal mixing quality for metal powders: Uniform mixing regardless of particle shape, size, density and flowability. Optimal homogeneity through three-dimensional rearrangement – regardless of filling level and mixing tool speed. Reliable prevention of segregation during the conveying and filling process.
- Optimisation of powder properties: amixon® guarantees the uniform distribution of all alloying elements.
- amixon® can coat/modify your mixing particles (also with nano-dispersed additives). This improves flowability and reduces segregation. The result is a homogeneous powder bed with uniform packing density.
amixon® mixers/blenders/drying mixers/synthesis reactors
- amixon® mixers/blenders also perform special applications: degassing, evaporation and drying of low-volatile media. This takes place in the vacuum-tight, temperature-controlled amixon® mixer. Subsequently, inerting of the powder mixture with inert gases is recommended.
- High-purity alloys: amixon® mixers can be provided with ceramic linings. This avoids metallic contamination of the mixture.
- amixon® mixers are pharmaceutically hygienic. They offer the highest process reliability and optimum powder quality for demanding additive manufacturing processes.
In the pilot plant of amixon GmbH, 4 mixers/vacuum dryers/synthesis reactors with 5 specific properties are available:
- Parts in contact with the product made of alloy 59
- Reaction temperature up to 350°C
- Reaction pressure up to 25 bar
- Product-contacting components coated with oxide ceramic
Fields of application for additive manufacturing processes
1. Packaging
More than 28% of the waste produced annually consists of containers and packaging. 3D printing is playing an increasingly important role in the development of sustainable packaging. Additive manufacturing enables the production of particularly lightweight structures that would not be possible using conventional packaging production methods (such as injection moulding). From protective covers to carrier systems: weight can be reduced by up to 30%.
2. luxury goods
From delicate cutlery to individual jewellery: 3D printing is also used in the luxury goods segment. This is a market that is predestined for additive manufacturing, as it offers the possibility of producing customised designs based on precious metals. 3D printing of these luxury goods serves as a proof of concept and paves the way for future applications in the mass market.
3. species protection
3D printing technology allows for unique structures. This is a major advantage for species protection, as weather-resistant components for any application can be produced quickly and flexibly.
Coral structures from the 3D printer are integrated into damaged ocean reefs to promote their growth and increase their area. Additive manufacturing makes components possible that can be easily positioned on the seabed. Structures that are of great interest to reef conservationists around the world.
amixon® always has more than 30 precision mixers available for testing
4. Batteries
Improved batteries are a pioneering future technology and powder bed fusion is making its contribution. Polymer powder bed fusion has been tested in the production of complex, three-dimensional lithium-iron batteries.
And as they develop, 3D-printed batteries will create completely new possibilities for the electronics industry. Today, electronics are designed for standard batteries. In the future, however, 3D printing will make it possible to integrate circuit boards into the structure of the device.
5. sports equipment
3D printing has long been used in prosthetic medicine. It is therefore not surprising that manufacturers of sportswear and sports medical products have also recognised the potential of additive manufacturing.
Whether it's shoe insoles with high shock absorption, airy bicycle helmets or custom-made golf clubs, powder bed fusion can be used to develop components that benefit the performance and health of the athlete.
The quantities of powder required are constantly increasing
6. pest control & disease prevention
Monitoring populations of disease vectors – such as mosquitoes – is crucial to protecting public health. However, logistical and financial hurdles are visibly complicating these efforts. For example, when malaria is endemic in a remote region and financial resources are lacking.
As part of an experiment, infectious disease experts in Essex (GB) used open-source designs to produce mosquito light traps in a 3D printer and place them in swamps. These light traps ultimately proved to be not only just as effective as the originals used in the field, but also 60% cheaper to produce and significantly lighter in weight.
With the knowledge gained, scientists are focusing on the expansion of vector surveillance programmes in particularly remote areas. The ultimate goal is to obtain more valid data that will help in the fight against infectious diseases.
amixon® offers a uniquely broad range of precision mixtures for metallic and ceramic high-performance materials. It makes no difference whether the powder components are micro- or nanostructured. Talk to us. We will be happy to advise you and carry out trials in the amixon® technical centre.
© Copyright by amixon GmbH