Precision mixer for powder metallurgy
Powder metallurgy is a special field of material science. Fine powders of iron, steel and non-ferrous metals are pressed to form a workpiece. Some methods of powder preparation and processing are similar to the production of high-performance engineering ceramics. A defined metal powder matrix is present with which oxides, borides, carbides and nitrides of the elements aluminum, zirconium and silicon combine.
The mixing / blending process:
On the one hand, the homogeneous distribution of the various powder components is important here. On the other hand, powdered lubricants / pressing aids (stearic acid, zinc stearate) must be homogeneously distributed in the metal powder. Such "metal soaps" reduce the internal friction of the powder coating and enable the uniform distribution of pressure in the die during compression. Pressing pressures can be a thousand bar and more. The particles of the pressing aids are mostly smaller than those of the metal powder and they are extremely light. Their bulk density is often less than one-twentieth of the metal powder bulk density.
The production of finely dispersed metal powders:
The metal powder particles must be sufficiently small and pure, for example 10 to 50 µm. The grinding process can take place in ball mills, impact mills or air jet mills. In most cases, however, the metal powders result from the spraying of molten metal at high pressure. Other processes to produce very fine metal particles also exist: dissolved metal salts are chemically precipitated or elements such as manganese and copper are obtained from electrolysis. If the metal powder has to have nanofine particles, a molten metal is heated under inert conditions until it evaporates and is precipitated as a condensate. Depending on the applied process, the obtained particles have to be deagglomerated, purified or dried.
A mixing challenge
Another mixing challenge involves an upstream process where metal powders must be chemically reduced in the furnace at high temperatures. A sufficient amount of carbon must then be available for each metal powder particle. In practice, this is achieved by coating the metal powders with carbon in the mixer. Large precision mixers / blenders are used here. In this case, the amixon® mixing / blending process also ensures that the finely dispersed carbon in the form of industrial carbon black evenly coats each individual iron particle. By the way: "The bulk density difference of carbon black and of metal powder differs by a factor of 500". This fact suggests that the components are insufficiently blendable or have a tendency to segregate.
Both phenomena are excluded in the amixon® mixer / blender.
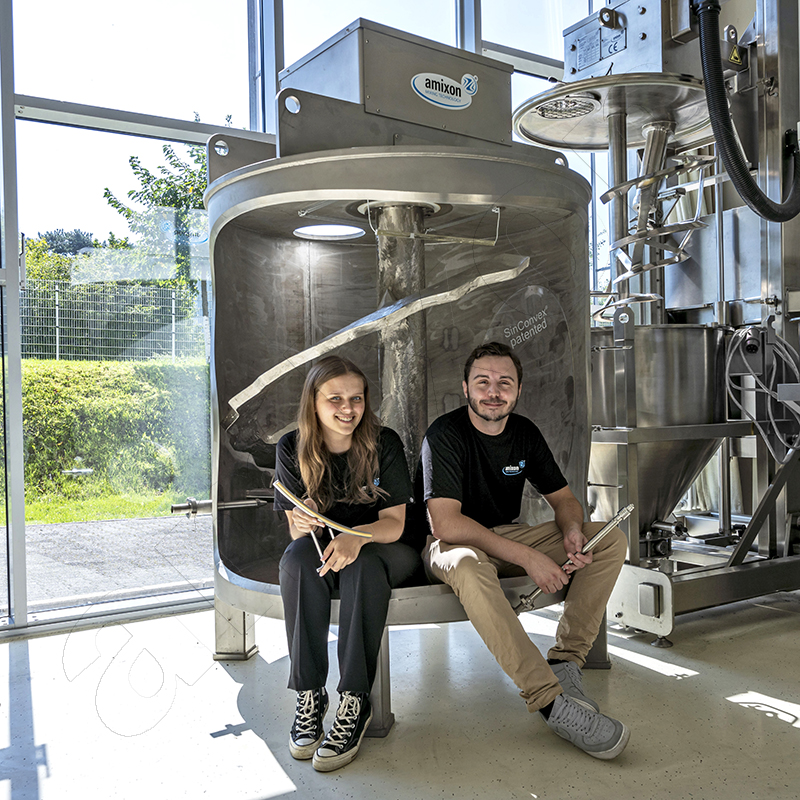
Demonstration object for heavy-duty applications.
In this respect, the mixing process in powder metallurgy is very complex.
amixon® has a lot of industry experience and can ensure ideal mixing grades for powder metallurgy, whether the mixing batch is 30 t or 10 kg. - Optionally, the mixing process can also take place continuously. It is crucial that the heavy, abrasive metal powders do not destroy the mixer and that the mixing process can start with the mixer filled to the maximum. In addition, it is important that the mixer works gently. The mixing process must not change the particle sizes and particle shapes.
What can amixon® contribute when powder metallurgy is used?
Gyraton® is ne development of Silo mixer / Silo blender.
A workpiece produced by powder metallurgy is only useful if its microstructure is homogeneous and stable. The homogeneity of the metal powders is of central importance for almost all process steps. amixon® has extensive references
- in metallurgy,
- in the preparation of ceramics
- in carbon chemistry
- in thermal process technology
- in bulk material mixing technology with abrasive solids (under vacuum and overpressure up to 20 bar)
- in the preparation of suspensions
- in chemistry with aggressive chemicals
- when it comes to particularly large mixed batches
In this respect, our process engineers can contribute a lot of know-how if you want to start an investment project.
Feel free to use the test center of amixon®
We recommend that you visit the amixon® test center in Paderborn - if possible with your original mixing goods. The amixon® team is looking forward to your visit. You will experience powder mixing / blending technology at the highest level and gather a lot of detailed knowledge. In addition, we will be happy to show you our modern production facilities.
Application for high performance materials:
Powder metallurgy and "mechanical alloying" are used when the resulting materials have unique properties:
- they permanently withstand high temperatures up to 800 °C (turbine blade, refractory linings)
- they are of extreme hardness (tungsten carbide for machining)
- they are extremely resistant to abrasion (brake discs)
- they are electrically conductive, insulating or act as semiconductors
- they change their size in milliseconds when connected to electric charge (piezo electronics)
- they are sponge-like porous and serve as chemical catalysts
- they are manufactured with defined porosity and serve as plain bearings for high-speed rotating components
- they are particularly well magnetizable. Metallic powders are used for the production of hard and soft magnets. (Induction coils in communications engineering)
- ...
Because the melting temperatures and the densities of the alloying constituents differ greatly, many high-performance materials cannot be produced by melt metallurgy. In addition, many metal components are unable to combine chemically. This makes materials that are produced using powder metallurgy interesting - despite their high cost.
Some expensive components have to be provided in powder form.
These include the elements chromium, iron, cobalt, copper, magnesium, manganese, molybdenum, nickel, niobium, rare earths, tantalum, titanium, vanadium, tungsten, zinc and their derivatives, which must be made available in the purest possible form. The quality of a powder metallurgically produced workpiece is determined by the purity of the input materials and their homogeneous distribution. Producing the smallest possible particles in high purity is extremely challenging.
Mechanical engineering applications
Iron-based powder metallurgy is mainly used for smaller workpieces (up to 4 kg) produced at high speed and in high quantities. Sintered parts are produced by casting metal powders into moulds and pressing them together. The subsequent sintering process shrinks components produced by powder metallurgy in a defined manner. The finished components are characterized by high dimensional accuracy. They have a similar stability to that of cast steel. However, their density is only 93% to 95% of the density of a cast component. Typical machine elements are precision mechanical components such as gears with helical gearing, rocker switches, valve shafts or grooved bushings for the automotive industry. Injection molding can be used for components with complicated geometric shapes. The metal powder is previously mixed with a thermoplastic bonding agent and then plasticized in a kneading machine.
The powder metallurgical production process is reserved for mass-produced products with small dimensions, because the process is expensive. The high costs are caused by several factors:
The manufacture of the wear-resistant component matrix
The component matrix must be enlarged by the shrinkage dimension. Often the question of sufficiently high fatigue strength of the pressing tools is synonymous with the question of wear resistance. The removal/discharge of the produced green compacts must be done without damage. This must take place quickly and efficiently in series production.
In many cases, hot sintering takes place under inert conditions, sometimes even in the absence of gas in a vacuum. If the compression takes place in a water bath, the densification of the metal powders can take place isostatically in a sealed environment. In many cases, the semi-finished products generated in this way are re-compacted in a sintering forge.
Shaping and debinding by chemical decomposition
High-performance presses must apply very high pressure to produce the green compacts. After pressing, the binder is thermally expelled from the green compacts by completing an optimized temperature curve.
The high temperature of hot sintering
The heat treatment extends over several hours. Thus, the atoms of the same and foreign metal particles diffuse. This is only possible if the particles grind and condense closely together. The microstructure formation takes place even though the elements involved are not compatible with each other in terms of melt metallurgy. This is the reason for the special features of the material.
Mechanical rework
Mechanical rework should normally be kept to a minimum.
© Copyright by amixon GmbH