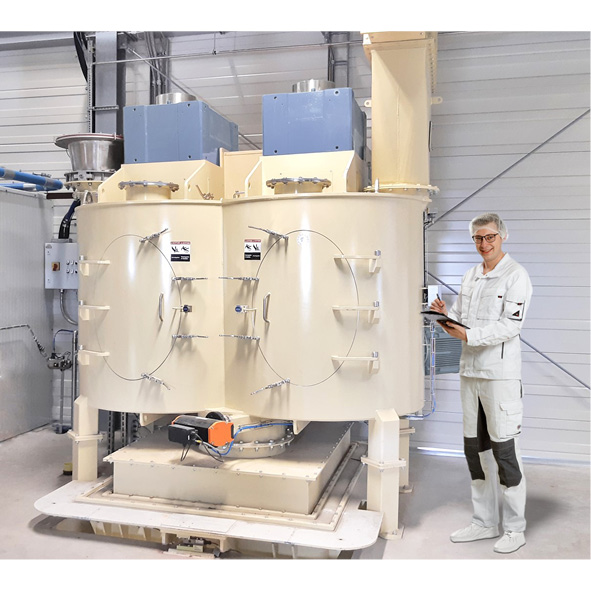
This 4 m³ amixon® twin-shaft mixer is equipped with a particularly large discharge device. A batch cycle takes only 5 minutes (filling, mixing, discharge and closing the discharge fitting).
Feed mixer for milk replacement feed, milk replacer
Milk replacement feed is produced for calves, but also for other farm animals. Dry milk and whey powder are enriched with nutrient additives so that the young animal can be weaned earlier from the mother.
A milk replacer must be easily digestible for the young animal. Its formula is therefore adapted to the age and the stage of development of the digestive organs.
The mixing task is ambitious. The powdered milk derivatives must be gently homogenized so that they can be quickly dissolved in water by the user - as instant products. In particular, the nutrient additives must be finely distributed in the powder. In some cases, fats are also added to increase the energy content.
An ideally conditioned milk replacer must essentially meet the following criteria:
- The trace elements and vitamins must be ideally distributed. This is similar to the production of infant formula.
- The fat must be ideally finely distributed.
- The mixing process should be fast and gentle; the powder must remain cold, no heat toning should be detectable.
- The powder should remain free-flowing .
- The powder should not clump when stacked in a big bag, sack or pouch.
- Atmospheric oxygen should optionally be replaced by inert gases in order to extend the shelf life. For more information on the topic of inerting, click here.
- The powder can also be impregnated.
- In this respect, the young animal should be quickly accustomed to normal feed and compound feed.
amixon® mixers are particularly well suited for this mixing task. The mixers are designed in an outstandingly hygienic manner. The mixing process is carried out gently. Optionally, the mixer can be manufactured vacuum-proof.
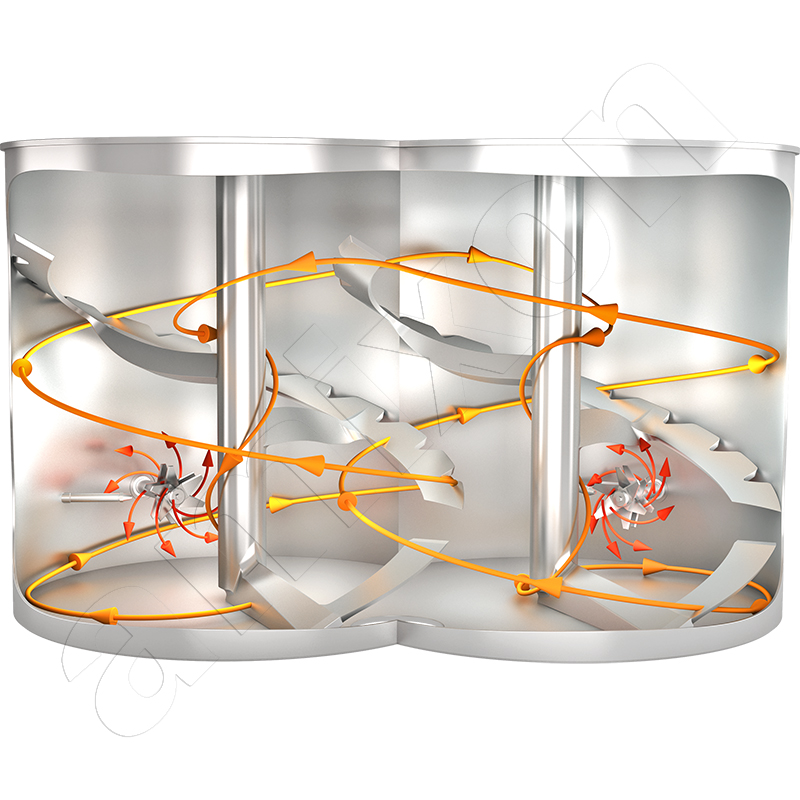
Mixing process in the amixon® twin shaft mixer. In the peripheral area of the mixing chamber, the upward flow is dominant. Inside the mixing chamber, the downward flow prevails. Shovel-shaped mixer elements realize the cross-flow of the mixing goods. In addition, high-speed rotating agitators can be installed. They realize the deagglomeration.
Trials with amixon® trial mixers
Even seemingly simple mixing tasks can be complicated. Practical examples show that the following must not happen:
- The bulk density changes.
- The pourability deteriorates.
- The mix heats up during mixing.
- The mixing quality is insufficient.
- The solubility of the powder is worse after the mixing process than before.
- The mix tends to clump and cake.
- The end product does not meet the end user's specifications.
- ....
Let the amixon® experts advise you in our technical centre. We can carry out mixing tests for you on a small and large scale. On request, amixon® can provide you with a test mixer (up to 3 m³) on loan.
amixon® guarantees you an optimally prepared end product!
This eliminates process-related risks. You already know all the quality characteristics of your future sales product before placing the order.
© Copyright by amixon GmbH