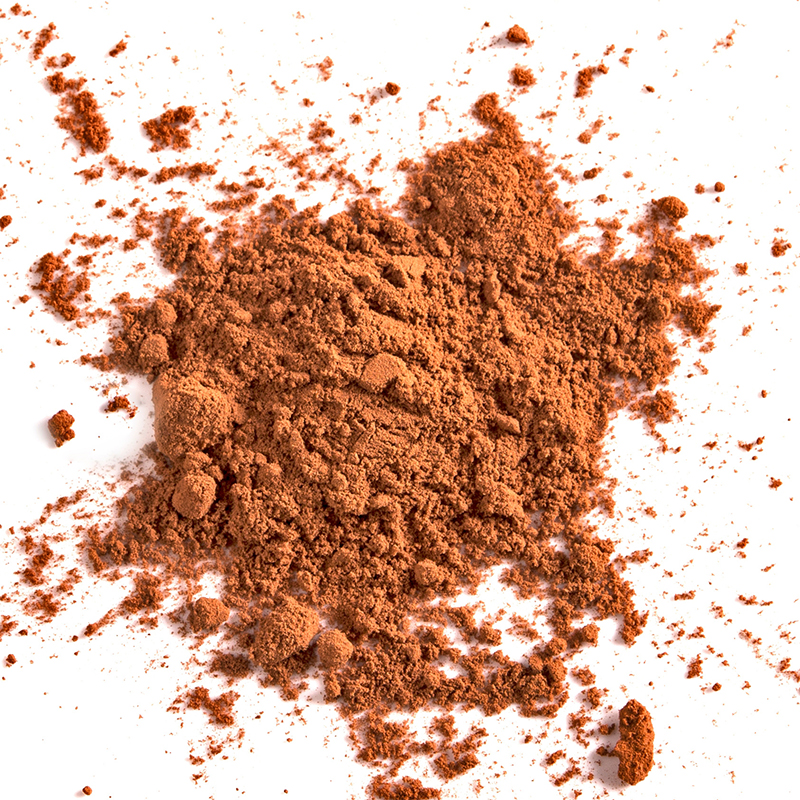
Bulk solids are difficult to describe. More than 30 parameters are used in powder technology. Characterisation of bulk solids includes, for example, properties such as grain shape, grain size distribution, moisture and bulk density. However, dustiness and flow behaviour are also of particular importance.
Distribution of flow aid, anti-caking aid, pouring aid into powder by mixing
The quality of a powder or a powder mixture is first determined by the purity and effectiveness of the ingredients. A powder is more effective the more specific surface area it has; that is, the finer it is ground. This means that the finer it is ground. For example, small quantities of a color pigment should be sufficient to color several tons of facade plaster homogeneously. Small amounts of a spice mixture should be enough to create the meat taste of vegan meatballs.
In addition to the effectiveness of a powder/powder mixture, secondary properties are also important. For example, when the powders are processed industrially. When instant drink mixes such as cappuccino or iced tea are bottled in sachet. When tea is filled into sachets, the filling process takes place at high speed. The powder mixture must be consistently free-flowing and dispensable. In addition, the mixture must be as dust-free as possible, otherwise the sealing of the sachets would not work successfully.
Powders can be made dust-free if they are enlarged to stable agglomerates. Then they usually flow better. Dust can also be reduced by moistening the powders. However, they flow less well the more humid they are. In many cases, liquid components have to be distributed into a mixture. Then each particle should be moistened with a proportional amount of the liquid. Usually, this also worsens the flow behavior of the powder. The liquid phase promotes the adhesion of the particles. Unintentional caking can occur.
The shape of the pouring cone gives first clues
There are many methods to determine the flowability of powders. A particularly simple method can be used for an initial assessment. The height of the bulk cone is determined. The powder flows through a sieve onto a metal cylinder and forms a pouring cone. The bulk cone increases to the point where the force of gravity is greater than the cohesive forces. Then the particles slide off each other. The steepness of the bulk cone provides a measure of the cohesion of the powder. A flat cone indicates good flowability of the powder.
The Jenike shear method is a professional method for measuring flow properties when powders are in multi-axial stress states (silo technology).
Binding mechanisms within particle collectives
If we look at a particle cluster, then gravity first affects each individual particle. In the lower layers, these compaction forces are subsumed according to the height of the bulk material. At the same time, the particles develop adhesion forces with each other. These are van der Waals forces and electrostatic interactions. These interparticulate forces dominate over the shear force when the particles become very small. Also, the presence of moisture increases the effect of interparticular forces.
Particle size and dust content
The more particles are in contact with each other, the greater the interparticulate forces. The adhesive forces increase more and more the finer a bulk material is dispersed. This correlation is significant. This is because the number of particle contacts is inversely proportional to the square of the particle size.
If the ambient air has a relative humidity of 50% or more, then hydrophilic powder particles can accumulate water. This is done in the form of single and multimolecular adsorption layers. When these adsorption layers of several particles (point by point) touch each other, capillary condensation occurs. The water forms liquid bridges and can cause particularly large adhesive forces between the particles. Agglomeration processes can be initiated in this form. If agglomeration is to be avoided, then the distance between the powder particles must be increased. This can be achieved if the powder particles are coated with a flow aid.
What can flow agents do?
They can:
- The flow behavior is improved
- Bonding and lumps are avoided
- The powder appears drier than it is
Two differently acting anti-caking aids:
c. light blue particles are wetted with a blue liquid. A liquid bridge binds two particles together.
d. after adding and mixing in a small amount of flow aid, the liquid is coated. Flow aids and liquid components have no affinity to each other. Both particles are now separated from each other.
e. brown particles are wetted with a turquoise liquid. A liquid bridge binds two particles together.
f. after addition and mixing in of a small amount of flow aid, the wetting liquid is absorbed. Flow aids and liquid components have a very high affinity for each other. Both particles are now separated from each other.
The use of flow additives should only be considered when a powder flows so unreliably,
- if automated powder processing is impeded, o
- when high-performance packaging machines block or
- if the product discharge from silos, big bags or bulk containers blocks
- when a bulk material tends to clump when at rest (time solidification).
Flow aids (another name is also anti-caking aid) are powders with a very low density that are particularly finely dispersed. This makes them extremely productive. Their specific surface area is extremely high. Their specific surface area is large. It can be more than 500 m²/g. Very small quantities can effectively coat powdery goods. Interparticular forces are reduced, fluid bridges disappear and the goods flow as expected.
Flow aids such as magnesium silicate, calcium silicate, silicon dioxide, (other names are also silica gel or silica) are extremely sensitive in terms of pressure and shear. If they are intensively mixed into bulk materials, their non-stick effect is lost. The flow aid must therefore be distributed minimally invasively into the bulk material; with minimal energy input. Nevertheless, the flow aid must coat all particles of the bulk material.
Flow aids are added to the bulk material only in proportions of 0.001 or 0.002 percent by weight. This makes the mixing task challenging.
The distribution of anti-caking agents in bulk materials is very demanding. Several conflicting goals must be overcome:
- If possible, the anti-caking agent should not have to be declared. This is particularly desired in the food industry
- Anti-caking agents should only be used in minimally small dosages; for example only 0.001 percent by weight
- Anti-caking agents are very light powders. They tend to "float" on the powder mixture
- Anti-caking agents are only effective if they are homogeneously distributed in the powder mixture
- The particle structure of the anti-caking agents is complex and extremely sensitive. Flow aids are only effective if they are unstressed i.e . have not been compacted and not sheared.
Gentle mixing - As many particles as possible of the bulk material mixture are coated.
amixon® has dealt with these and similar tasks for many years and has developed particularly effective solutions. amixon® mixers are excellently suited for such mixing tasks. Bulk materials are made flowable by using minimally few anti-caking agents. This also happens when the batches are several cubic meters in size. This demanding process task is performed excellently in amixon® mixers in an optimally gentle manner, within a short mixing time.
amixon® test mixers of various sizes are available: 10 liters, 100 liters, 400 liters, 1000 liters, 2000 liters and 3000 liters.
Dry Liquid
The structure of the particle surface is characterized by the presence of many capillaries. The particles of the flow aid possess an extremely large surface area. In this respect, flow aids can also be used to absorb large quantities (more than a hundred times their own weight) of liquid and also to bind them permanently. This is referred to as "dry liquids". amixon® mixers are particularly suitable for producing dry liquids due to their gentle mode of operation.
Occasionally, "dry liquids" are produced to moisten critical powders and suppress their agglomeration. This method of powder wetting works without liquid spray systems.
Wetting process. Here you can see the liquid at rest in the centre, the dry powder at the edge and the slowly progressing wetting. The wetting behaviour of flow aids is totally different. Within seconds, the entire liquid would be absorbed. (Flash absorption)
© Copyright by amixon GmbH