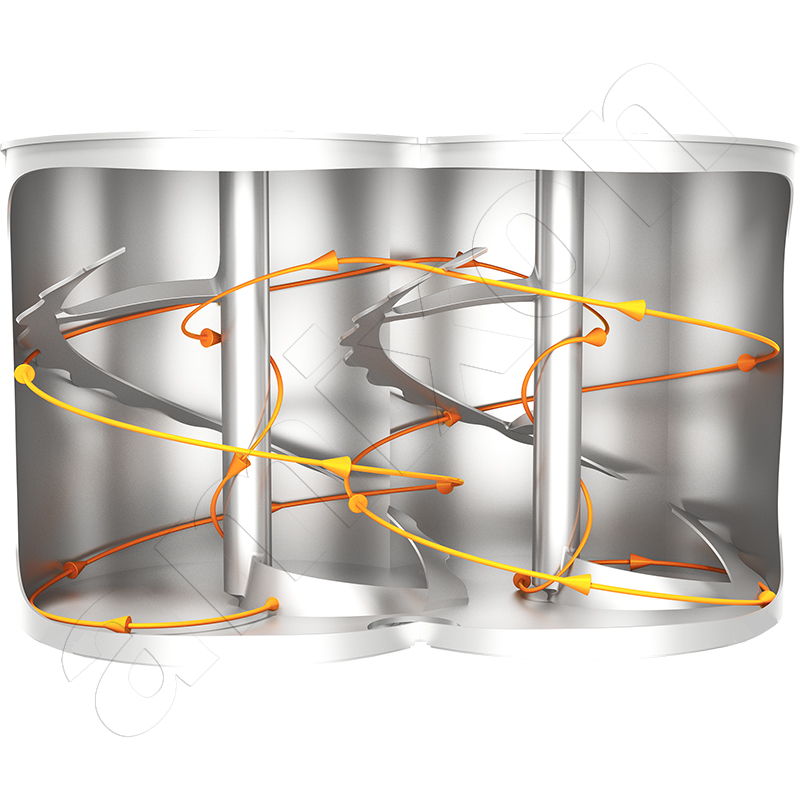
Discover our twin shaft mixer HM
HM twin-shaft mixer for the final homogenization of dietetic products
In this product digression, we will focus on the 10 m³ amixon® HM twin-shaft mixer for the final homogenization of dietetic products. A batch often involves more than 40 different components. This 10 m³ amixon® HM 10 000 mixer is used for the final homogenisation of dietetic products. There are often more than 40 different components involved in a batch.
What are the arguments for using a particularly large amixon® powder mixer for such sensitive mixing materials?
The size of your production mixer should always be matched to the typical order quantities and your internal logistics. If large quantities of the same product are produced regularly, the advantages of a large powder mixer may dominate. A large mixer is particularly advantageous if the formulation contains many different individual components. Each individual raw material must be accurately weighed and transported to the mixer. In the case of a large batch, the number of individual weighings is reduced.
For the purpose of quality assurance, you only need to take one sample of the mix per batch after the mixing process. Only one laboratory analysis is required. The laboratory costs are lower. Only one reserve sample per batch is kept.
The best possible mixing qualities are mandatory for us. In view of this, the question arises as to what range my batch sizes may vary.
The system concept shown here can be used for a wide range of filling levels from approx. 1 to 10 m³. It is possible to mix complex powder mixtures effectively, particularly gently and hygienically! The mixing quality achieved corresponds to an ideal distribution. The mixing quality can not be further improved in practice.
What criteria are used to select the most suitable mixer?
The selection of the powder mixer shown above results from economic considerations. Users report 5 benefits from their experience with amixon® twin shaft mixers:
- The many individual components are filled directly into the mixer from above after weighing. The mixer also serves as a control weighing vessel for all large components.
- The mixing time is only 3 to 9 minutes, depending on the rotation frequency of the mixing tools. The peripheral speed of the mixing tools is optionally only 1 m/s. The particles of the mixed material are not stressed or damaged. The mixing goods remain at the same cool temperature after mixing as before the mixing process.
- After in-factory validation, it is sufficient to take only one product sample from the mixer.
- The mixer empties almost completely except for a few grams of dust. Do you have any questions on the topics of residue-free emptying, batch fidelity and contamination? Then please read
- The contents of the mixer are weighed. It rests on four digital load cells. This large mixer has 4 DosiFlap® discharge valves that operate without dead space. This means that the mix can be filled into big bags or containers at the same time. Four weighing platforms (5) are embedded in the floor. DosiFlap® is controlled by the signals of the floor scales.
Depending on the classification of the mixed products, which are homogenised one after the other in the mixer, cleaning takes place dry or wet. The mixer has four large (1) inspection doors. An inspection door is installed in the housing of each outlet fitting (2).
© Copyright by amixon GmbH