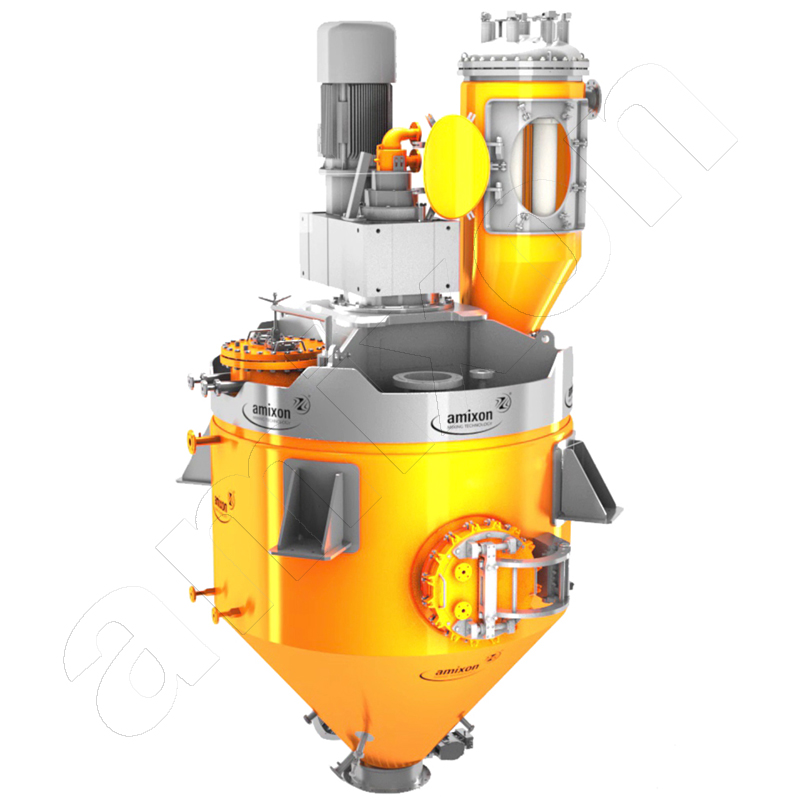
amixon® aide à dimensionner les grandes installations de séchage sous vide mixte
Les mélangeurs-sécheurs sous vide et les réacteurs de synthèse amixon® sont utilisés pour presque tous les types de produits en vrac et de suspensions. En raison des grandes surfaces spécifiques de transfert de chaleur, les appareils amixon® sont également utilisés comme évaporateurs.
Les sécheurs sous vide compacts amixon® se distinguent par les caractéristiques suivantes :
- excellente efficacité énergétique
- mouvement très doux du produit
- grande surface spécifique d'échange de chaleur
- vitesse de séchage très élevée
- qualité de mélange idéale
- design particulièrement hygiénique
- Les appareils amixon® sont également utilisés comme réacteurs stériles en biochimie et en pharmacie.
Comment amixon® peut-il aider à transférer les résultats de laboratoire à l'échelle technique ?
Lorsque de nouveaux produits ou procédés sont développés, les questions de mise en œuvre technique doivent être étudiées en parallèle. Le passage de l'échelle de l'éprouvette à celle de l'installation industrielle n'est pas trivial.
Le centre technique sert à définir des paramètres de processus qui permettent d'obtenir des résultats aussi bons que ceux que les chercheurs ont obtenus auparavant dans l'éprouvette.
amixon® est un fabricant d'installations techniques de procédés et dispose de ses propres Technika. Les installations y sont montées de manière fonctionnelle. Ils sont dimensionnés de manière à permettre la conception d'installations industrielles à grande échelle.
Dans le centre technique, amixon® permet de faire la démonstration de pratiquement tous les procédés de mélange/affinage de produits en vrac et de séchage sous vide. La pression dans la chambre de mélange peut varier de 5 mbar à 26 bar (pression absolue). La température peut varier de moins à 350°C.
Le client peut ainsi découvrir rapidement à quel point une réaction de synthèse ou un procédé de séchage sous vide fonctionne bien et rapidement avec son produit.
Comment extrapoler d'une installation pilote à une grande installation ?
Des difficultés apparaissent lorsque l'installation industrielle à mettre en place est 100 fois plus grande que la machine de processus dans le centre technique. Pour les questions thermocinétiques, les considérations de similitude géométrique échouent. C'est là que le savoir-faire pratique aide à appliquer les calculs thermodynamiques.
amixon® aide à l'extrapolation sur des machines de process plusieurs fois plus grandes que l'installation expérimentale. Jusqu'à présent, amixon® a pu démontrer à maintes reprises la justesse de nos méthodes de calcul. À savoir, chaque fois que la grande installation dans l'environnement industriel fournit ou dépasse les performances calculées.
amixon® invite volontiers ses clients de près ou de loin à faire des essais et leur promet déjà de très bons résultats. Nous pouvons le faire grâce à des décennies d'expérience.
Les essais de séchage réalisés dans le centre technique d'amixon® sont toujours utiles et permettent d'acquérir un grand nombre de connaissances. amixon® protège les informations partagées avec vous contre les tiers. Ainsi, l'échange d'informations reste toujours confidentiel.
Les essais de séchage diffèrent des essais de mélange classiques. Le temps de traitement est beaucoup plus long. De nombreuses données sont enregistrées pendant le processus de séchage dans le centre technique amixon®. Cette opération est en grande partie automatisée.
Cela laisse suffisamment de temps pour discuter de détails constructifs. Il devrait toujours y avoir une visite détaillée de l'usine. Certains clients en profitent pour faire des essais de mélange pour le processus suivant. D'autres en profitent pour faire des essais d'agglomération.
Comment calculer l'écoulement des poudres dans un mélangeur vertical de type amixon® ?
Les mélangeurs amixon® mélangent en trois dimensions et produisent des qualités de mélange idéales qui ne peuvent pas être améliorées dans la pratique. Pour ce faire, l'hélice de malaxage transporte l'enrobé vers le haut sans espace mort et la force de gravité permet à l'enrobé de s'écouler vers le bas. Le courant produit Iv peut être décrit approximativement comme suit.
Iv : Débit d'une hélice mélangeuse verticale
D/ d : Diamètre extérieur/intérieur de l'hélice
φ : Degré de remplissage
S : Pas de l'hélice
n : Fréquence de rotation
ζ : Coefficient de vitesse
Dans cette mesure, la puissance de mélange spécifique des malaxeurs amixon® est toujours la même, quelle que soit la taille, dans la mesure où les conditions géométriques sont congruentes.
amixon® dispose à Paderborn de différents réacteurs de synthèse/sécheurs-mélangeurs sous vide. Certains ont une chambre de mélange conique. Certaines ont un fond plat.
Y a-t-il des particularités pour les processus qui se déroulent à des températures et des pressions élevées ?
Le centre technique amixon® permet également de réaliser des essais dans des conditions de processus extrêmes :
- Pression du système dans la chambre de traitement jusqu'à 25 bar de surpression : Le transfert de chaleur est influencé par les parois plus épaisses du récipient. D'autre part, les températures dans l'espace de traitement peuvent être modifiées extrêmement rapidement en changeant la pression du système. Si la pression du système est augmentée dans la chambre de traitement, les réactions gaz-solide, par exemple, peuvent être favorisées. Par exemple aussi les processus de diffusion ....
- Chauffage jusqu'à 350°C : Les joints traditionnels en polymères échouent lorsque les températures dépassent 240 °C en permanence. Seuls des systèmes à étanchéité métallique ou des joints en graphite peuvent alors être utilisés.
- vide fin de 1 mbar absolu : Une telle pression absolue exige une étanchéité exceptionnelle de l'appareillage et de tous les tuyaux de raccordement qui communiquent. Cela vaut en particulier pour l'étanchéité de l'arbre du mélangeur.
Comment illustrer clairement le déroulement d'un séchage mixte sous vide ?
Le déroulement du séchage d'une expérience peut être représenté sous forme de diagramme, comme indiqué ici. L'heure est inscrite en abscisse. Différentes grandeurs physiques sont portées sur l'axe des ordonnées :
- La pression du système dans l'espace de traitement,
- la masse du liquide déshydraté,
- la température de la masse à sécher et
- les températures du fluide caloporteur dans les circuits aller et retour.
Le mélangeur-sécheur sous vide est généralement rempli avec le volume maximal de la charge avant le début du processus de séchage. En règle générale, le volume du mélange diminue au fur et à mesure que le séchage progresse.
Dans de rares cas, le volume de remplissage reste constant, bien que l'enrobé soit plus sec et plus léger. Dans de très rares cas exceptionnels, il peut même y avoir une augmentation de volume pendant le séchage. Cette augmentation de volume doit être prise en compte, car les mélangeurs/sécheurs ne doivent pas être exploités à l'excès.
Comment la surface de transfert de chaleur varie-t-elle lorsque le taux de remplissage diminue ?
La surface d'échange thermique du séchoir sous vide varie en fonction du niveau de remplissage. Dans ce cas, la chambre de mélange est constituée d'un cône sur lequel est monté un cylindre. Dans la dérivation suivante, la surface d'échange de chaleur est calculée dans le cas où le volume de remplissage est inférieur à la partie conique du mélangeur-sécheur. Tout d'abord, la hauteur de remplissage hFK dans le cône est calculée :
La surface transmettant la chaleur dans le cône AF est uniquement la surface en contact avec l'enrobé.
Si le taux de remplissage du mélangeur-sécheur change pendant le processus de séchage, la surface de contact de l'outil de mélange tempéré change également. Cet état de fait ne peut pas être décrit comme une fonction fermée. amixon® mesure la surface d'échange thermique de l'outil de mélange dans le système CAO pour différents degrés de remplissage. Les données sont saisies sous forme de tableau et interpolées.
Quel est le besoin en chaleur si le mélangeur-sécheur sous vide est beaucoup plus grand que l'installation expérimentale ?
Deux indices sont introduits ci-dessous : "R" (référence) pour l'installation pilote et "T" (cible) pour l'installation à grande échelle. Le temps de séchage est le temps qui s'écoule entre le début et la fin de l'évaporation. Les conditions idéalisées suivantes sont supposées :
- Les conditions de processus dans l'appareil de contrôle sont identiques à celles du grand appareil.
- L'évaporation se fait à température constante.
- L'évaporation se fait à pression constante du système.
- Le coefficient de transfert de chaleur est le même dans les deux appareils.
- La différence de température moyenne entre le milieu chauffant et l'enrobé est la même.
L'enthalpie d'évaporation hv à la pression de saturation ps permet de déterminer le flux de chaleur QR de l'installation expérimentale. Ainsi, le flux de chaleur à travers la surface de contact chaufféeAT du grand séchoir peut être calculé comme suit.
Combien de temps dure le processus de séchage dans la grande installation ?
En supposant que la densité RO du produit humide est la même dans l'installation de référence et dans la grande installation, la masse du produit dans la grande installation peut être calculée si le taux de remplissage PHI est connu.
La masse mT à évaporer dans la grande installation est de fT1 à la fin du séchage et de fT2 au début du séchage pour les degrés d'humidité.
Le temps de séchage dans la grande installation est alors de
Quelle est la taille de l'installation de chauffage nécessaire pour le grand séchoir ?
Le diagramme suivant montre les différents points de consommation. Chaque consommateur doit être suffisamment alimenté par l'énergie thermique extrapolée. Le facteur de conception S permet de calculer le flux de chaleur dans l'installation de chauffage. La base est le flux de chaleur Qvap nécessaire à l'évaporation.
Le débit massique du fluide caloporteur Qvap résulte de la capacité thermique spécifique cp, de la température d'entrée du fluide caloporteur T1,heat et de la température de sortie du fluide caloporteur T2,heat. Le thermofluide doit être réparti de manière à ce que tous les consommateurs soient suffisamment alimentés. Cela signifie que toutes les zones de l'espace de traitement doivent être chauffées de manière uniforme. La condensation doit être évitée. Le produit humide doit être réchauffé dans la mesure où l'énergie de la vapeur est évacuée. La température de l'enrobé correspond à la température d'évaporation du vide appliqué.
Quelle est la taille du filtre à vapeur pour le grand séchoir ?
Estimation de la surface filtrante nécessaire sur la base de la charge admissible du filtre fs
Avec le débit volumique dV/dt, le débit massique dm/dt et la densité ro de la vapeur.
La vitesse du gaz brut chargé de poussières v est de
La charge de la surface filtrante fs est définie en [m³/h/m²].
Quelle est la taille du condenseur pour le grand séchoir ?
La buée évaporée est nettoyée dans le filtre à buées et liquéfiée dans le condenseur. Le flux de chaleur Qkond doit alors être évacué. La surface de condensation refroidie Akond sert à cela.
Le débit massique du fluide de refroidissement mcool est calculé en tenant compte du coefficient de transfert de chaleur et de la différence de température moyenne :
Lors de la détermination de la valeur K, il faut tenir compte du type de construction du condenseur et du facteur d'encrassement auquel on peut s'attendre.
Une droite idéalise le débit massique du condensat.
Quelle est l'intention lorsque le débit massique mesuré du condensat est moyenné par une droite ? Cette approximation grossière permet une comparaison avec un échangeur de chaleur à flux parallèle fonctionnant en continu. Les effets de la modification des paramètres du processus peuvent être calculés avec une très bonne approximation.
Combien de temps dure le processus de séchage dans la grande installation si la température du fluide thermique est modifiée ?
.... lorsque l'installation de séchage fonctionne avec un fluide caloporteur plus chaud ou plus froid. Cette considération se fait par analogie avec le fonctionnement d'un échangeur de chaleur à flux parallèle :
T2,heat ne peut être itéré que numériquement.
Une courbe intéressante peut ainsi être approchée. Elle permet d'estimer les temps de séchage à différentes températures du fluide caloporteur.
Pourquoi est-il plus long de refroidir une poudre sèche que de réchauffer une poudre humide ?
Pour estimer le temps de refroidissement DELTA tT, on part du principe que les conditions sont les mêmes dans l'installation expérimentale et dans le grand séchoir. Cela vaut aussi bien pour le coefficient de transfert de chaleur que pour la différence de température moyenne entre le fluide caloporteur et la température du produit.
Le produit dans la grande installation doit être refroidi à la même température finale que celle testée dans l'installation expérimentale.
Que remarque-t-on sur ce diagramme lors du refroidissement de l'enrobé ?
Un déroulement typique du refroidissement est représenté ci-dessous. Le refroidissement d'une poudre sèche prend plus de temps que le chauffage d'une poudre humide. Il y a deux explications à cela :
- Un liquide conduit beaucoup mieux la chaleur que la plupart des solides.
- Le film liquide qui entoure une particule humide peut mouiller la paroi qui transmet la chaleur. Cela favorise le transfert de chaleur. En revanche, une particule sèche ne touche que ponctuellement la surface tempérée.
Dans le cas présent, le séchoir a été chauffé avec une différence de température très élevée. L'huile thermique était au départ à environ 120°C. Dans ce cas, il faut d'abord refroidir l'ensemble de l'accumulateur d'huile thermique dans l'aller de l'installation. Ainsi, le refroidissement de la poudre sèche s'effectue avec une hystérésis marquée.
Si l'on utilisait de l'eau comme fluide caloporteur, le processus de refroidissement se déroulerait de manière accélérée.
© Copyright by amixon GmbH