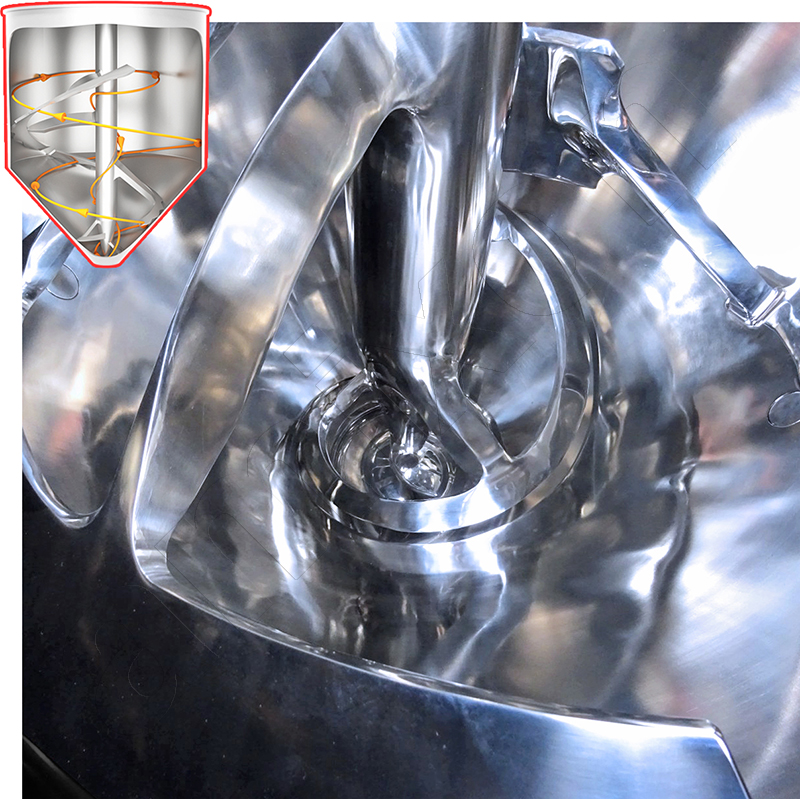
Гигиенический дизайн в производстве детских смесей
Спрос на промышленно производимые детские смеси из сухих производных молока в промышленно развитых и развивающихся странах очень высок, как и требования к качеству и составу используемых порошковых смесей.
Микрокомпоненты, такие как пробиотики, пребиотики, минералы и микроэлементы, включая такие важные элементы, как цинк, медь, селен и хром, должны быть распределены в детской смеси с максимальной точностью и равномерностью. В связи с небольшими дозировками и высокой значимостью для баланса питательных веществ можно использовать только высокоточные смесители.
Процесс смешивания должен быть щадящим: Структура частиц сырья должна быть сохранена. Функциональные ингредиенты в капсулах, например, витамины, пробиотические культуры, должны быть сохранены. Смешанные продукты не должны нагреваться.
Часть 1: Технология смешивания детских смесей на примере вертикального двухвального смесителя HM
Часть 2: технология смешивания amixon® для детских смесей на примере смесителя KoneSlid® KS и смесителя непрерывного действия AMK
Смесители amixon гарантируют сохранение качеств сырья, особенно его мгновенных свойств при растворении в воде:
- Без пыли
- способность к дозированию, текучесть
- отличная дисперсность
- надежная смачиваемость
- быстрое схватывание
- надежное растворение
Смесители amixon® всегда достигают идеального качества смешивания. Независимо от размера частиц, насыпной плотности или текучести.
Кроме того,amixon® гарантирует быстрое и практически без остатка опорожнение порошкового смесителя. Это предотвращает потери продукта и перекрестное загрязнение.
Смесительные системы amixon® отвечают самым высоким гигиеническим стандартам и разработаны в соответствии с действующими рекомендациями по пищевым технологиям (например, EHEDG, FDA, GMP)
© Copyright by amixon GmbH