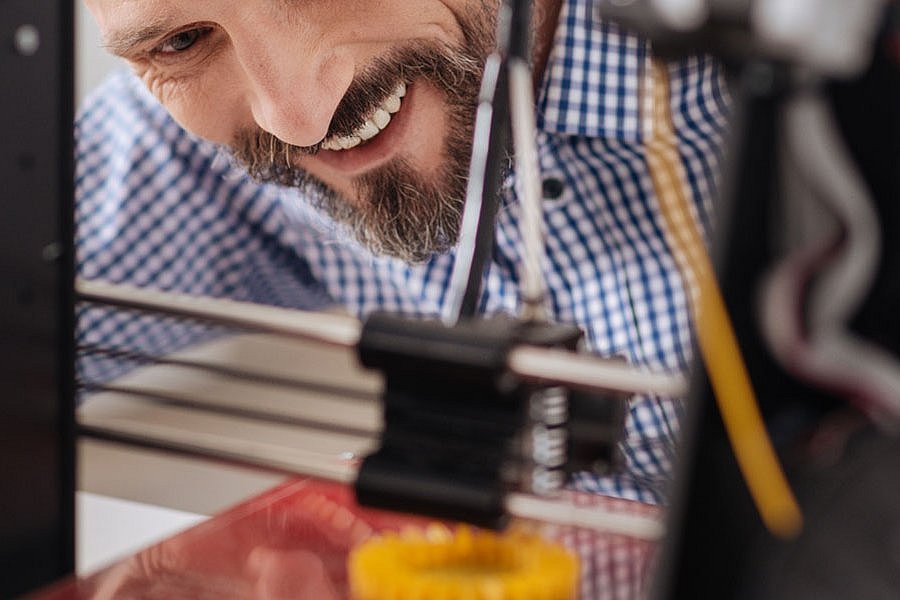
Les mélangeurs, les sécheurs sous vide, les réacteurs de synthèse remplissent des fonctions importantes dans la métallurgie des poudres et dans la préparation des polymères.
Préparation des poudres pour les procédés de fabrication additive avec les mélangeurs industriels amixon®
Les termes « impression 3D », « prototypage rapide » et « fabrication additive » signifient essentiellement la même chose. Il s'agit de la fabrication de pièces tridimensionnelles par l'application de couches successives de matériaux. Pendant l'application, les couches sont fusionnées ou frittées. Ce procédé de fabrication est utilisé avec succès dans l'industrie pour les matériaux métalliques, les céramiques à base d'oxyde, les matières plastiques et les matériaux de construction liés au ciment.
Procédés et domaines d'application pour l'impression 3D industrielle
L'impression 3D est un procédé de fabrication additif important de l'industrie 4.0 qui, en combinaison avec d'autres procédés additifs, révolutionnera à l'avenir les méthodes de production en tant que technologie clé. Le procédé est toujours utilisé lorsque trois conditions sont réunies :
- Une structure géométrique complexe,
- Un faible nombre de pièces
- Un degré élevé de personnalisation.
Un exemple : la réparation nécessaire de machines dont les pièces de rechange ne sont plus disponibles. Les pièces préalablement conçues en trois dimensions sont transformées en composants physiques grâce à la conversion directe des données. Par rapport aux procédés de fabrication traditionnels par enlèvement de copeaux, il n'est donc plus nécessaire de recourir à un dispositif, à des pièces moulées ou à un outil spécifique au produit. Outre les propriétés mécaniques et technologiques du composant à produire, il est en outre possible de créer des structures complexes qui ne seraient pas possibles avec un processus de fabrication conventionnel. La rentabilité du procédé d'impression 3D augmente donc avec la complexité croissante de la géométrie (individuelle) de la pièce et la diminution du nombre de pièces.
Les applications d'impression 3D se retrouvent dans de nombreux secteurs industriels. On peut citer l'industrie mécanique et automobile, la construction de modèles et l'architecture, mais aussi la médecine humaine et dentaire pour la fabrication de prothèses. Le procédé convient également à la mise en œuvre rapide des résultats intermédiaires obtenus en biologie structurelle. Cela est particulièrement vrai lorsque les structures de résistance des fibres végétales doivent être transposées dans des structures porteuses modernes.
L'importance d'une préparation adéquate de la poudre pour les procédés d'impression 3D
Au début du processus d'impression 3D, un lit de poudre avec une densité de tassement suffisamment bonne est dispersé. Si l'apport d'énergie est contrôlé avec précision, des collectifs de particules fusionnent pour former des structures cibles. La poudre en excès est éliminée et, dans l'idéal, utilisée pour d'autres structures en couches. Lors de l'introduction de la poudre dans le lit de poudre, il est important que la structure des particules, la taille des particules, la densité apparente et la rhéologie du produit en vrac de la poudre soient aussi stables que possible. En effet, les étapes de travail doivent être rapides afin de garantir la rentabilité de la production. Les étapes du processus sont donc réalisées à l'aide de transports pneumatiques par aspiration, qui s'accompagnent de vitesses de transport élevées et donc d'une production accrue d'abrasion. L'excellent conditionnement des poudres de polymère utilisées revêt donc une importance particulière.
Des conditions similaires prévalent également dans le frittage sélectif au laser à partir de poudre métallique.
L'ajout de la poudre dans le lit de poudre se fait ici à l'aide d'une racle. Les propriétés d'écoulement des poudres ont une grande influence sur l'homogénéité du lit de poudre et doivent donc s'écouler le plus librement possible. L'objectif : des formes de particules sphériques et une distribution granulométrique étroite. De plus, les agglomérats doivent être dispersés, sinon des défauts de surface ou linéaires apparaissent dans la pièce.
Ce qui est nécessaire : une préparation adéquate de la poudre comme élément de base pour une impression 3D industrielle réussie. Pour éviter les collages et les agglomérats et pour améliorer la fluidité de la poudre, les mélangeurs de précision ou les installations de mélange qui fonctionnent selon le procédé du lit fluidisé sont particulièrement adaptés.
Mélangeurs de poudres, sécheurs sous vide et réacteurs amixon® pour la préparation des poudres pour l'impression 3D industrielle
Dans la métallurgie des poudres et la préparation des polymères, les mélangeurs de poudre, sécheurs sous vide et réacteurs de synthèse amixon® remplissent des fonctions importantes. L'objectif : l'enrobage nanofin de chaque particule. Cet objectif ne peut être atteint que si le matériau de revêtement se présente sous la forme d'une solution ou d'une suspension faible et qu'il est mélangé de manière microfine à la poudre. En d'autres termes, la poudre doit être humidifiée de manière uniforme, puis séchée particulièrement rapidement et délicatement afin de mener à bien le processus d'enrobage uniforme de toutes les particules individuelles.
Qualité de mélange idéale et vidange complète
Le sécheur à cône et réacteur à cône amixon®, qui permet d'obtenir des qualités de mélange homogènes idéales et en même temps un séchage sous vide particulièrement rapide et doux. Au centre, notre SinConvex® innovant tourne et génère un écoulement total de l'enrobé. Le long de la périphérie de la cuve de mélange, la poudre s'écoule d'abord en spirale vers le haut. Une fois arrivée, la poudre redescend le long de l'arbre de mélange sous l'effet de la gravité. Le processus d'écoulement s'effectue sans espace mort et avec une faible fréquence de rotation. L'apport d'énergie est donc faible et préserve de manière fiable la structure des particules des matières premières. Ceci est particulièrement important dans la mesure où des quantités parfois très faibles d'agents d'écoulement extrêmement légers, comme la silice pyrogénée, sont mélangées de manière homogène et en douceur dans les poudres. Dans la pratique, il peut arriver que l'agent d'écoulement flotte sur la poudre et entrave ainsi massivement le processus de mélange. Néanmoins, ils ne sont efficaces que s'ils sont répartis en douceur et de manière homogène dans la poudre, et en aucun cas broyés.
Enfin, les parois de la cuve de mélange, l'arbre du mélangeur ainsi que les bras de l'outil de mélange sont fabriqués à double enveloppe et sont parcourus par un fluide thermique (huile thermique, eau ou vapeur) en circuit fermé. Tout cela favorise encore plus l'évaporation de la phase liquide de l'enrobé.
La contamination croisée doit être évitée et la vidange sans ségrégation ni résidus doit être garantie pour le bien du contrôle des lots et de l'assurance qualité. Grâce à notre technologie innovante
ComDisc®, nos mélangeurs de poudres atteignent un taux de vidange résiduelle allant jusqu'à 99,997 pour cent. De plus, toutes nos installations de mélange sont conçues sans joints et soumises à un nettoyage humide ou mouillé approfondi. Grâce à notre système de nettoyage humide WaterDragon®, toutes les pièces en contact avec le produit sont nettoyées sans résidus, et ce de manière autonome, simple et fiable.
Développement de procédés et essais
Test, pilotage, mise en service. Qui développe de nouveaux produits doit généralement aussi développer la technique de procédé appropriée. Dans le centre technique d'amixon®, plus de 40 machines d'essai sont disponibles. Les lots d'essai peuvent varier de 1 litre à 3000 litres. Presque chaque appareil qu'amixon fabrique est unique : « Spécialement adapté à l'application de chaque client ... ». Dans le centre technique, nous recueillons avec nos clients des idées et des concepts qui sont ensuite mis en œuvre lorsqu'un appareil amixon est commandé.
© Copyright by amixon GmbH