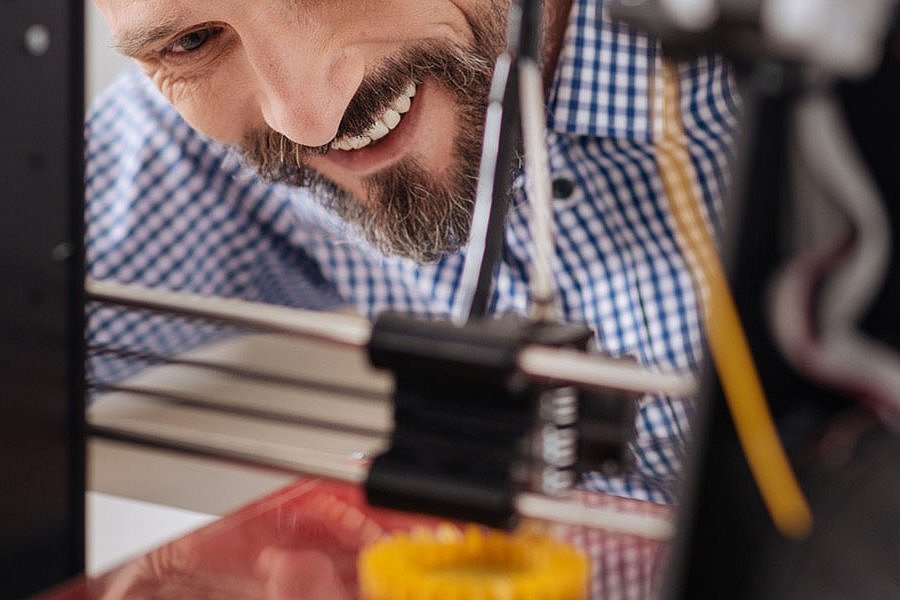
Mixers, vacuum dryers, synthesis reactors perform important functions in powder metallurgy and polymer processing.
Powder processing for additive manufacturing with industrial mixers by amixon®
The terms ‘3D printing’, ‘rapid prototyping’ and ‘additive manufacturing’ essentially mean the same thing. They all refer to the production of three-dimensional components by applying successive layers of material. During application, the layers are fused or sintered together. This manufacturing process is successfully used on an industrial scale for metallic materials, oxide ceramics, plastics and cement-based building materials.
Processes and applications for industrial 3D printing
3D printing is an important additive manufacturing process in Industry 4.0 and, in combination with other additive processes, will revolutionise production methods in the future as a key technology. The process is used whenever three conditions are present:
- A complex geometric structure,
- A small quantity
- A high degree of customisation.
An example: the necessary repair of machines whose spare parts are no longer available. The components, which have previously been designed in three dimensions, are transferred into physical components by directly implementing the data. In contrast to conventional machining processes, no fixtures, castings or product-specific tools are required. Apart from the mechanical and technological properties of the component to be produced, complex structures can also be created that would not be possible using a conventional manufacturing process. As the complexity of the (individual) component geometry increases and the number of units produced decreases, the economic efficiency of the 3D printing process increases.
3D printing applications can be found in many sectors of industry. These include the mechanical engineering and automotive industries, model making and architecture, but also human and dental medicine for the production of prostheses. The process is also suitable for the rapid implementation of intermediate results achieved in structural bionics. This is particularly true when the strength structures of plant fibres have to be transferred to modern load-bearing structures.
The importance of suitable powder preparation for 3D printing processes
At the beginning of the 3D printing process, a powder bed with sufficiently good packing density is applied. Under precisely controlled energy input, particle collectives merge to form target structures. Excess powder is removed and ideally reused for further layer structures. When introducing the powder into the powder bed, it is important that the particle structure, particle size, bulk density and bulk rheology of the powder are as stable as possible. The process steps must be carried out quickly to ensure cost-effective production. The process steps are therefore carried out using pneumatic conveying systems, which are associated with high conveying speeds and thus increased abrasion. The good conditioning of the polymer powders used is therefore of particular importance.
Similar conditions prevail in the selective laser sintering of metal powders.
Here, the powder is added to the powder bed by a doctor blade. The flow properties of the powders have a major influence on the homogeneity of the powder bed and must therefore be as free-flowing as possible. The aim is to achieve spherical particle shapes and a narrow particle size distribution. In addition, agglomerates must be dispersed, as otherwise flat or linear defects may occur in the component.
What is needed: adequate powder processing as the basis for successful industrial 3D printing. To avoid agglomerates and sticking, and to improve the flowability of the powder, precision mixers or mixing systems that work according to the fluidised bed process are particularly suitable.
amixon® powder mixers, vacuum dryers and reactors for powder processing for industrial 3D printing
In powder metallurgy and polymer processing, amixon® powder mixers, vacuum dryers and synthesis reactors perform important functions. The goal: the nano-fine coating of each individual particle. This can only be achieved if the coating material is present as a weak solution or suspension and is mixed into the powder in a micro-fine manner. This means that the powder must be evenly moistened and then dried particularly quickly and gently in order to successfully complete the process of evenly coating all individual particles.
Ideal mixing quality and complete emptying
The amixon® conical mixing dryer and reactor AMT, which enables ideal homogeneous mixing quality and at the same time particularly fast and gentle vacuum drying. Our innovative SinConvex® mixing tool rotates in the centre and creates a total flow of the mixing material. Along the periphery of the mixing container, the powder initially flows upwards in a spiral. Once there, the powder flows downwards again along the mixing shaft due to gravity. The flow process takes place without dead space and at a low rotational frequency. The energy input is therefore low and reliably protects the particle structure of the raw materials. This is particularly important because in some cases very small quantities of extremely light flow aids such as fumed silica are gently and homogeneously mixed into the powders. In practice, the flow aid may float on the powder and thus severely impede the mixing process. However, these additives are only effective if they are gently and homogeneously distributed in the powder, but under no circumstances should they be crushed.
Finally, the walls of the mixing container, the mixing shaft and the arms of the mixing tool are manufactured with a double jacket and a thermal fluid (thermal oil, water or steam) flows through them in a closed circuit. All of this additionally promotes the evaporation of the liquid phase of the mixture.
Cross-contamination must be avoided and segregation-free and complete emptying must be ensured for the benefit of batch control and quality assurance. Thanks to our innovative amixon® ComDisc technology, our powder mixers achieve a residual emptying rate of up to 99.997 per cent. In addition, all our mixing systems are designed to be seamless and are thoroughly cleaned using a damp or wet method. With our WaterDragon® wet cleaning system, all parts that come into contact with the product are cleaned without leaving any residue. This is done autonomously, easily and reliably.
Process development and trials
Test, pilot, start-up. Anyone who develops new products usually also has to develop the appropriate process technology. More than 40 test machines are available at the amixon® technical centre. The test batches can vary from 1 litre to 3000 litres. Almost every device that amixon manufactures is unique: ‘Specifically tailored to the application of the respective customer...’. In the technical centre, we work with our customers to develop ideas and concepts that are then implemented when an amixon machine is ordered.
© Copyright by amixon GmbH