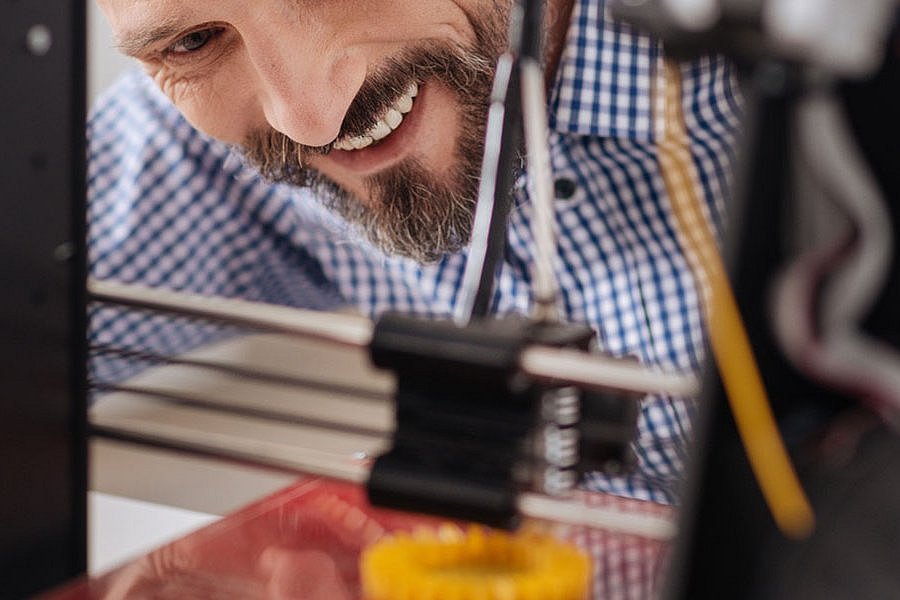
Las mezcladoras, los secadores al vacío y los reactores de síntesis desempeñan funciones importantes en la pulvimetalurgia y el procesamiento de polímeros.
Preparación de polvos para procesos de fabricación aditiva con mezcladoras industriales de amixon®
Los términos «impresión 3D», «prototipado rápido» y «fabricación aditiva» significan esencialmente lo mismo. Se refiere a la producción de componentes tridimensionales mediante la aplicación de capas sucesivas de material. Durante el proceso de aplicación, las capas se funden o sinterizan entre sí. Este proceso de fabricación se utiliza con éxito industrialmente para materiales metálicos, cerámicas oxidadas, plásticos y materiales de construcción cementosos.
Procesos y ámbitos de aplicación de la impresión 3D industrial
La impresión 3D es un importante proceso de fabricación aditiva en la Industria 4.0 y, en combinación con otros procesos aditivos, revolucionará los métodos de producción como tecnología clave en el futuro. El proceso se utiliza siempre que se den tres condiciones:
- Una estructura geométrica compleja,
- Una cantidad pequeña
- Un alto grado de personalización.
Un ejemplo: la reparación necesaria de máquinas cuyas piezas de recambio ya no están disponibles. Los componentes diseñados previamente en tres dimensiones se transforman en componentes físicos mediante la conversión directa de los datos. A diferencia de los procesos de producción de mecanizado convencionales, esto significa que no se necesita ni una plantilla, ni piezas de fundición, ni una herramienta específica para el producto. Además de las propiedades mecánicas y tecnológicas del componente que se va a fabricar, también se pueden crear estructuras complejas que no serían posibles con un proceso de fabricación convencional. A medida que aumenta la complejidad de la geometría del componente (personalizado) y disminuye el número de unidades producidas, aumenta la rentabilidad del proceso de impresión 3D.
Las aplicaciones de la impresión 3D pueden encontrarse en muchas ramas de la industria. Entre ellas se encuentran la ingeniería mecánica y la automoción, la construcción de modelos y la arquitectura, así como la medicina humana y la odontología para la producción de prótesis. El proceso también es adecuado para la rápida realización de resultados intermedios logrados en biónica estructural. Esto es especialmente cierto cuando hay que transferir las estructuras de resistencia de las fibras vegetales a estructuras portantes modernas.
La importancia de una preparación adecuada del polvo en los procesos de impresión 3D
Al principio del proceso de impresión 3D, se dispersa un lecho de polvo con una densidad de empaquetamiento suficientemente buena. Si la entrada de energía se controla con precisión, los colectivos de partículas se fusionan para formar estructuras objetivo. El polvo sobrante se retira y, en el mejor de los casos, se utiliza para otras estructuras de capas. Al introducir el polvo en el lecho de polvo, es importante que la estructura de las partículas, el tamaño de las partículas, la densidad aparente y la reología aparente del polvo sean lo más estables posible. Esto se debe a que los pasos del proceso deben llevarse a cabo rápidamente para garantizar la eficacia de la producción. Por ello, los pasos del proceso se llevan a cabo utilizando transportadores neumáticos de succión, que están asociados a altas velocidades de transporte y, por tanto, a una mayor producción de abrasión. Por lo tanto, es especialmente importante un excelente acondicionamiento de los polvos de polímero utilizados.
Condiciones similares prevalecen en la sinterización selectiva por láser a partir de polvo metálico.
El polvo se añade al lecho de polvo mediante una rasqueta. Las propiedades de flujo del polvo tienen una gran influencia en la homogeneidad del lecho de polvo y, por lo tanto, deben ser lo más fluidas posible. El objetivo es conseguir partículas de forma esférica y una distribución de tamaños reducida. Los aglomerados también deben estar dispersos, ya que de lo contrario se producirán defectos planos o lineales en el componente.
Lo que se necesita: una preparación adecuada del polvo como elemento básico para el éxito de la impresión 3D industrial. Las mezcladoras de precisión o los sistemas de mezcla que utilizan el proceso de lecho fluidizado son especialmente adecuados para evitar adherencias y aglomerados y mejorar la fluidez del polvo.
Mezcladores de polvo, secadores de vacío y reactores amixon® para la preparación de polvo para la impresión 3D industrial
Los mezcladores de polvo, secadores al vacío y reactores de síntesis amixon® cumplen importantes funciones en la pulvimetalurgia y el procesamiento de polímeros. El objetivo: el recubrimiento nanofino de cada partícula. Esto sólo puede lograrse si el material de recubrimiento está disponible como solución débil o suspensión y se mezcla microfino en el polvo. Esto significa que el polvo debe humedecerse uniformemente y, a continuación, secarse con especial rapidez y suavidad para completar con éxito el proceso de recubrimiento uniforme de todas las partículas individuales.
Calidad de mezcla ideal y vaciado completo
El secador de cono y reactor de cono amixon®, que permite obtener calidades de mezcla homogéneas ideales y, al mismo tiempo, un secado al vacío especialmente rápido y cuidadoso. Nuestro innovador SinConvex® gira en el centro y genera un flujo total de la mezcla. El polvo fluye inicialmente hacia arriba en espiral a lo largo de la periferia del recipiente de mezcla. Una vez allí, el polvo vuelve a fluir hacia abajo a lo largo del eje mezclador debido a la gravedad. El proceso de flujo tiene lugar sin espacios muertos y con una baja frecuencia de rotación. Por tanto, el aporte de energía es bajo y protege de forma fiable la estructura granulométrica de las materias primas. Esto es especialmente importante, ya que a veces cantidades muy pequeñas de aditivos de flujo extremadamente ligero, como la sílice pirógena, se mezclan homogénea y suavemente con los polvos. En la práctica, puede ocurrir que el antiaglomerante flote en el polvo y obstaculice así masivamente el proceso de mezcla. No obstante, sólo son eficaces si se distribuyen suave y homogéneamente en el polvo, pero nunca se trituran.
Por último, pero no por ello menos importante, las paredes del recipiente de mezcla, el eje mezclador y los brazos de la herramienta mezcladora son de doble pared y tienen un fluido térmico (aceite térmico, agua o vapor) que fluye a través de ellos en un circuito cerrado. Todo ello favorece además la evaporación de la fase líquida de la mezcla.
Debe evitarse la contaminación cruzada y garantizarse un vaciado sin segregación ni residuos en beneficio del control de lotes y la garantía de calidad. Gracias a nuestro innovador
ComDisc®, nuestras mezcladoras de polvo alcanzan una tasa de descarga residual de hasta el 99,997%. Además, todos nuestros sistemas de mezcla están diseñados sin juntas y se someten a una limpieza a fondo en húmedo o mojado. Con nuestro sistema de limpieza en húmedo WaterDragon®, todas las piezas que entran en contacto con el producto se limpian sin dejar residuos, de forma autónoma, fácil y fiable.
Desarrollo de procesos y ensayos
Pruebas, pilotaje, puesta en marcha. Quien desarrolla nuevos productos suele tener que desarrollar también la tecnología de procesos adecuada. En el centro técnico de amixon® disponemos de más de 40 máquinas de ensayo. Los lotes de prueba pueden variar desde 1 litro hasta 3000 litros. Casi todos los aparatos que fabrica amixon son únicos: «Especialmente adaptados a la aplicación del cliente correspondiente...». Junto con nuestros clientes, recogemos ideas y conceptos en el centro técnico, que luego se ponen en práctica cuando se encarga un aparato amixon.
© Copyright by amixon GmbH