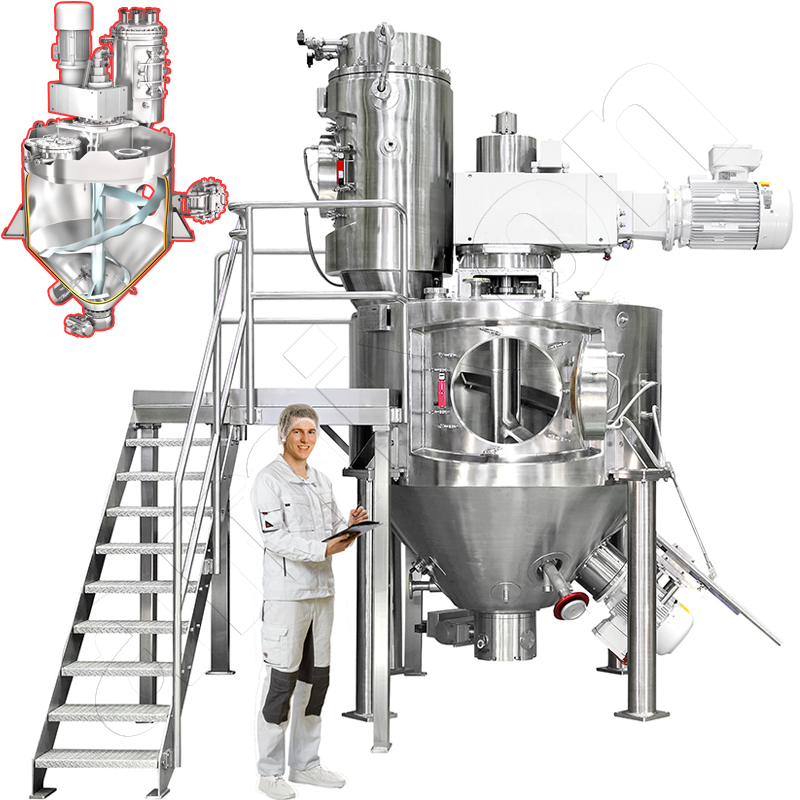
Vacuum Mixer
The pressure is measured in the physical unit Pascal. 1 Pa = 1 N/m² = 0.01 mbar.
Sometimes we also encounter the older unit of measurement Torr = 1 mm Hg column = 1.333 mbar.
The quality of a vacuum is divided into the following ranges
- 1 bar to 1 mbar Rough vacuum
- 1 mbar to 10-3 mbar Fine vacuum
- 10-3 mbar to 10-7 mbar High vacuum
- 10-7 mbar to 10-10 mbar Ultra-high vacuum
In this glossary, we use the term vacuum/vacuum mixer in a simplified way. However, according to the above table, this only refers to the "rough vacuum" range and, in individual cases, a "part of the fine vacuum" range.
Advance notice:
When we pour bulk materials onto a plane, the result is a cone-shaped pile. In the resting state, the differently shaped particles lie, as it were, above and next to each other. Each particle is in equilibrium. The forces acting on a single particle are: the gravitational force, the contact force and the contact forces of neighboring particles. The sum of all forces acting on the particles is zero. Due to their round shape, most particles touch each other only selectively. There are many voids between the particles. Even a single particle can have voids. This is referred to as the porosity of a disperse system. In physical formulas, the ancient Greek letter for PHI is usually used for porosity. Porosity is a dimensionless quantity. It is a measure of how much gas/air is present in a bulk material.
Depending on the temperature and air pressure, the ambient air contains more or less moisture in the form of water vapor. The water accumulates in microscopic condensate layers on the solid surfaces also in the pores of the particles. In this respect, bulk solids under atmospheric conditions are three-phase disperse systems. They consist of solid, liquid and gas.
The vessels of process engineering machines such as vacuum mixers, agitators, mixers, reactors, separators, etc. may only be filled with product up to a maximum permissible filling level. Above the mixed material layer there is usually ambient air. This gas volume must also be removed in the event of evacuation.
There are many reasons why a mixing room may need to be evacuated. Some of them are:
- Avoidance of oxidation with atmospheric oxygen,
- Avoidance of fire and explosion hazards,
- Avoidance of fluidization of powders,
- Elimination of excess gas pressure due to reactive gas formation,
- Reduction of the system pressure to accelerate a drying process,
- Generation of intense solid friction to accelerate deagglomeration and diffusion within solid particles,
- Temporary increase in bulk density,
- Replacement of the gas contained in the bulk material (inerting with nitrogen or carbon dioxide)
- Degassing of liquids,
- Removal of air when powder is pneumatically sucked or blown into a container,
- this is also the case, for example, when large quantities of powder are mixed into a liquid (high-shear mixing technology with rotor-stator configuration).
- when high-purity substances are synthesized,
- when sterile conditions are required,
- in the control of fermentation processes,
- when disperse systems are to be cooled by enthalpy reduction,
- during freeze-drying,
- when highly viscous liquids are to be impregnated into powder particles
- ......
The above methods can be carried out in the industrial finishing of fabrics in the vacuum mixer. This is the case, for example, for pharmaceutical products, cosmetics, chemical agents and foodstuffs.
In order to be able to create a vacuum, two basic requirements are needed: A gas-tight/vacuum-proof container and a vacuum pump.
Vacuum mixers can be used universally.
When evacuating a disperse system, the gas is accelerated in the direction of the vacuum pump. Depending on the gas velocity, the flowing gas can unintentionally entrain dust particles from the bed. This is undesirable in most cases. Therefore, dust filters are installed upstream of the vacuum pump. When designing pneumatic and vacuum systems, the following performance parameters, among others, must be coordinated:
- the pumping speed of the pump
- the efficiency of the pump
- the robustness of the pump
- the effective pumping speed
- the suction power
- the line length
- the gas velocity
- Flow resistance
- Filter function
- Filter area
- Filter load
- Filter cleaning
- Filter conditioning
- Set-up time in case of cleaning/wet cleaning
- ...
Wet or moist dispersions must also be evacuated/vacuum dried in the vacuum mixer in many cases. In this case, the escaping gas is not only dusty, but also contaminated with water vapor or solvent vapor. Such a gas is called vapors in practice. It can only be cleaned in a so-called vapor filter. The filter housing must be heated well above the dew point temperature of the liquid phase. The purified gas can then optionally be dehumidified in a heat exchanger. The solvents can be recovered in this way. The back-flushed dust returns to the vacuum mixer.
Vacuum mixer application example in the production of food supplements
Vacuum mixers in the production of food supplements based on protein powder mixtures:
The nutritional composition of a protein powder blend consists of the protein sources such as whey, casein or soy. These are mixed with other powdered ingredients such as amino acids, vitamins, minerals and sweeteners. Vacuum technology plays an important role in this process to prevent oxidation. The powder, which is filled into cans or bags, must be largely free of oxygen and moisture.
A vacuum mixer can be helpful here by removing atmospheric oxygen from the mixed materials prior to packaging/filling in the mixer and then bringing them to atmospheric pressure with a mixture of carbon dioxide gas and nitrogen. This measure stabilizes the flow properties and prolongs the shelf life of the nutrient composition.
Vacuum mixer application example in pharmaceutical industry
Vacuum mixer for solid active pharmaceutical ingredients must be converted into user-friendly dosage forms such as chewable tablets, effervescent tablets, oral tablets, capsules or suppositories, ..... Beforehand, the active ingredients must be diluted with the aid of fillers. This is done in powder mixers. Some active ingredients are extremely finely particulate, so their dusts must be bound. This is done by agglomeration in the fluid bed apparatus or in the vacuum mixer. Agglomeration processes are favored by the presence of liquid binders. The liquid phase must then be dried. The drying process is massively accelerated by applying a vacuum. By lowering the system pressure, the water evaporates well below 100°C. Low drying temperatures are also helpful for thermally sensitive active pharmaceutical ingredients.
Atmospheric oxygen can negatively affect the shelf life of solid drugs. An Inerting process can be performed as described in the previous chapter - with the help of a vacuum mixer.
A typical galenic preparation process is the so-called trituration of active ingredients in order to disperse them particularly uniformly in a powdered filler or excipient. This type of deagglomeration can be effectively supported in the vacuum mixer. The internal maturation of the bulk mixture is increased and undesirable fluidization is reliably avoided.
- If a liquid active ingredient is to be embedded inside filler pellets, a vacuum mixer is useful. Only after a fine vacuum has removed most of the air from the pores of the filler agglomerates is the liquid active ingredient sprayed into the vacuum mixer. The system pressure is then slowly increased to atmospheric pressure. The so-called impregnation can advantageously be carried out using an inert or noble gas.
- Sometimes drugs are administered in liquid form. In this case, it may be necessary to disperse or dissolve powdered active ingredients in the liquid. Many problems can occur when introducing and distributing powders in liquids. Some of these are: undesirable foaming, inhomogeneous distribution of the liquid and solid phases, long process times, encapsulation of powder agglomerates. As mentioned at the beginning, the gas phase is always present if it has not been evacuated beforehand. Here, too, vacuum mixers provide valuable services.
- In special cases, a dusty, finely dispersed active ingredient is to be applied uniformly to the surface of a powdered carrier material. This should be done without the detour of wetland agglomeration. Even such a complicated homogenization process can be conveniently carried out with the help of vacuum mixers.
- Fermentation and synthesis processes are almost always completed in the wet phase. The product is then either evaporated or mechanically dehumidified as an intermediate step. The final drying step can again be carried out conveniently in a heated vacuum mixer.
- Powdered active substance can sublimate. This means that the active ingredient evaporates bypassing the liquid phase. In a vacuum mixer, sublimation can be accelerated to safely discharge the gas as an active ingredient.
Vacuum mixers, which heat the mix during mixing, are far more important. This is achieved by attaching a double jacket to the mixing chamber and the mixing tool. Heat transfer media (water, steam or thermal oil) flow through the double jacket and transfer their heat energy to the mix.
Vacuum mix drying
The residual moisture in the mix is effectively vaporised. The mix dries very quickly and effectively. The vacuum lowers the boiling point. This means that heat-sensitive active ingredients can be dried quickly and economically. This topic is covered in blog posts on this website.
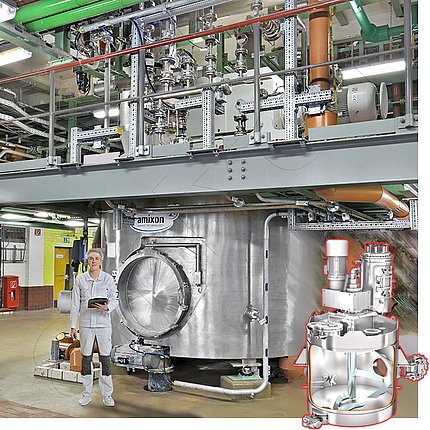
Vaporiser
In some cases, liquids need to be vaporised. This is also done efficiently and effectively by applying heat and vacuum. With amixon technology, you can test all these processes with your mixed products. This topic is also covered in blog posts on this website.