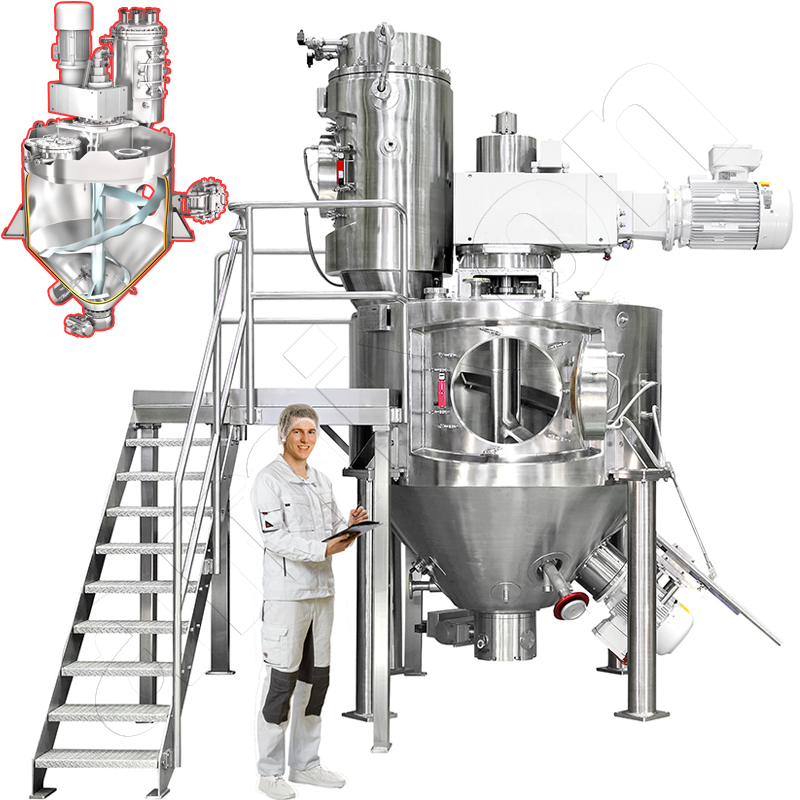
Mélangeur sous vide
La pression est mesurée par l'unité physique Pascal. 1 Pa = 1 N/m² = 0,01 mbar.
On rencontre aussi parfois l'ancienne unité de mesure Torr = 1 mm Hg colonne = 1,333 mbar.
La qualité d'un aspirateur sous vide est divisée en plusieurs catégories
- 1 bar à 1 mbar Aspiration brute
- 1 mbar à 10-3 mbar Aspiration délicate
- 10-3 mbar à 10-7 mbar Aspiration élevée
- 10-7 mbar à 10-10 mbar Aspiration ultra-élevée
Dans ce glossaire, nous utilisons les termes aspiration/mélangeur sous vide de manière simplifiée. Nous ne nous penchons que sur l’aspiration brute et dans certains cas, sur l’aspiration délicate.
Avis préalable :
Lorsqu’on déverse des matériaux en vrac dans un avion, on obtient une pile en forme de cône. À l'état de repos, les particules de forme différente se trouvent pour ainsi dire au-dessus et à côté les unes des autres. Chaque particule est en équilibre. Les forces agissant sur une seule particule sont : la force gravitationnelle, la force de contact et les forces de contact des particules voisines. La somme de toutes les forces agissant sur les particules est nulle. En raison de leur forme ronde, la plupart des particules ne se touchent que de manière sélective. Il y a de nombreux vides entre les particules. Même une seule particule peut présenter des vides. C'est ce que l'on appelle la porosité d'un système dispersé. Dans les formules physiques, la lettre grecque ancienne PHI est généralement utilisée pour la porosité. La porosité est une grandeur sans dimension. Il s'agit d'une mesure de la quantité de gaz/d'air présente dans un matériau en vrac.
En fonction de la température et de la pression atmosphérique, l'air ambiant contient plus ou moins d'humidité sous forme de vapeur d'eau. L'eau s'accumule dans des couches de condensation microscopiques sur les surfaces solides et dans les pores des particules. À cet égard, les solides en vrac dans des conditions atmosphériques sont des systèmes dispersés en trois phases. Ils se composent de solides, de liquides et de gaz.
Les cuves des machines d'ingénierie telles que les mélangeurs sous vide, les agitateurs, les mélangeurs, les réacteurs, les séparateurs, etc. ne peuvent être remplies de produit que jusqu'au niveau de remplissage maximal autorisé. Au-dessus de la couche de matériaux mélangés se trouve généralement l'air ambiant. Ce volume de gaz doit également être aspiré en cas d'évacuation.
Il existe de nombreuses raisons pour lesquelles une salle de mélange doit être évacuée. En voici quelques-unes :
- Éviter l'oxydation par l'oxygène atmosphérique,
- Éviter les risques d'incendie et d'explosion,
- Éviter la fluidification des poudres,
- Éliminer la surpression de gaz due à la formation de gaz réactifs,
- Réduire la pression du système pour accélérer le processus de séchage,
- Générer une friction solide intense pour accélérer la désagglomération et la diffusion au sein des particules solides,
- Augmenter temporairement la densité apparente,
- Remplacer le gaz contenu dans le matériau en vrac (inertage à l'azote ou au dioxyde de carbone)
- Dégazer les liquides,
- Éliminer l'air lorsque la poudre est aspirée ou soufflée pneumatiquement dans un récipient,
- c'est également le cas, par exemple, lorsque de grandes quantités de poudre sont mélangées à un liquide (technologie de mélange à haut cisaillement avec configuration rotor-stator).
- lorsque des substances de haute pureté sont synthétisées,
- lorsque des conditions stériles sont requises,
- dans le contrôle des processus de fermentation,
- lorsque les systèmes dispersés doivent être refroidis par réduction d'enthalpie,
- pendant la lyophilisation,
- lorsque des liquides très visqueux doivent être imprégnés dans des particules de poudre
- ......
Les méthodes ci-dessus peuvent être appliquées à la finition industrielle des tissus dans le mélangeur sous vide. C'est le cas, par exemple, pour les produits pharmaceutiques, les cosmétiques, les agents chimiques et les denrées alimentaires.
Pour pouvoir créer un vide, deux conditions de base sont nécessaires : Un récipient étanche au gaz et au vide et une pompe à vide.
Les mélangeurs sous vide peuvent être utilisés de manière universelle.
Lors de la mise sous vide d'un système de dispersion, le gaz est aspiré en direction de la pompe à vide. En fonction de la vitesse d’aspiration, le gaz en circulation peut involontairement entraîner des particules de poussière du lit. Cela n'est pas souhaitable dans la plupart des cas. C'est pourquoi des filtres à poussière sont installés en amont de la pompe à vide. Lors de la conception de systèmes pneumatiques et à vide, les paramètres de performance suivants, entre autres, doivent être coordonnés :
- la vitesse de pompage
- l'efficacité de la pompe
- la robustesse de la pompe
- la vitesse de pompage effective
- la puissance d'aspiration
- la longueur de la ligne
- la vitesse du gaz
- la résistance à l'écoulement
- la fonction du filtre
- la zone de filtrage
- la charge du filtre
- le nettoyage du filtre
- le conditionnement des filtres
- le temps de préparation en cas de nettoyage / nettoyage humide
- ...
Dans de nombreux cas, les dispersions humides ou mouillées doivent également être évacuées/séchées sous vide dans le mélangeur sous vide. Dans ce cas, le gaz qui s'échappe est non seulement poussiéreux, mais aussi contaminé par de la vapeur d'eau ou de la vapeur de solvant. Dans la pratique, ce gaz est appelé "vapeur". Il ne peut être nettoyé que dans ce que l'on appelle un filtre à vapeur. Le boîtier du filtre doit être chauffé bien au-dessus de la température du point de rosée de la phase liquide. Le gaz purifié peut ensuite être déshumidifié dans un échangeur de chaleur. Les solvants peuvent être récupérés de cette manière. La poussière refoulée retourne dans le mélangeur sous vide.
Exemple d'application d'un mélangeur sous vide dans la production de compléments alimentaires
Mélangeurs sous vide pour la production de compléments alimentaires à base de mélanges de protéines en poudre :
La composition nutritionnelle d'un mélange de protéines en poudre comprend des sources de protéines telles que le lactosérum, la caséine ou le soja. Ceux-ci sont mélangés à d'autres ingrédients en poudre tels que des acides aminés, des vitamines, des minéraux et des édulcorants. La mise sous vide joue un rôle important dans ce processus pour éviter l'oxydation. La poudre, qui est introduite dans des boîtes ou des sacs, doit être largement exempte d'oxygène et d'humidité.
Un mélangeur sous vide peut être utile ici, car il élimine l'oxygène atmosphérique des matériaux mélangés avant l'emballage/le remplissage dans le mélangeur, puis les ramène à la pression atmosphérique avec un mélange de dioxyde de carbone et d'azote. Cette mesure stabilise les propriétés d'écoulement et prolonge la durée de conservation de la composition nutritive.
Exemple d'application d'un mélangeur sous vide dans l'industrie pharmaceutique
Mélangeur sous vide pour les ingrédients pharmaceutiques actifs solides
Les mélanges doivent être convertis en formes posologiques faciles à utiliser, telles que des comprimés à croquer, des comprimés effervescents, des comprimés oraux, des gélules ou des suppositoires, ...... Au préalable, les principes actifs doivent être dilués à l'aide de produits de remplissage. Cette opération s'effectue dans des mélangeurs de poudre. Certains ingrédients actifs sont extrêmement fins et leurs poussières doivent donc être liées. Cela se fait par agglomération dans l'appareil à lit fluidisé ou dans le mélangeur sous vide. Les processus d'agglomération sont favorisés par la présence de liants liquides. La phase liquide doit ensuite être séchée. Le processus de séchage est massivement accéléré par l'application d'un vide. En abaissant la pression du système, l'eau s'évapore bien en dessous de 100°C. Les basses températures de séchage sont également utiles pour les ingrédients pharmaceutiques actifs thermosensibles.
L'oxygène atmosphérique peut avoir un effet négatif sur la durée de conservation des médicaments solides. Un processus d'inertage peut être réalisé comme décrit dans le point précédent - à l'aide d'un mélangeur sous vide.
- Un processus de préparation galénique typique est la trituration des ingrédients actifs afin de les disperser de manière particulièrement uniforme dans un excipient en poudre. Ce type de désagglomération peut être efficacement pris en charge par le mélangeur sous vide. La maturation interne du mélange en vrac est accrue et la fluidification indésirable est évitée de manière fiable.
- Si un ingrédient actif liquide doit être incorporé dans des granulés de remplissage, un mélangeur sous vide est utile. Ce n'est qu'après qu'une aspiration délicate a éliminé la majeure partie de l'air des pores des agglomérats de charge que l'ingrédient actif liquide est pulvérisé dans le mélangeur sous vide. La pression du système est ensuite lentement augmentée jusqu'à la pression atmosphérique. L'imprégnation peut avantageusement être réalisée à l'aide d'un gaz inerte ou noble.
- Les médicaments sont parfois administrés sous forme liquide. Dans ce cas, il peut être nécessaire de disperser ou de dissoudre les ingrédients actifs en poudre dans le liquide. De nombreux problèmes peuvent survenir lors de l'introduction et de la distribution de poudres dans des liquides. En voici quelque-uns: moussage indésirable, distribution inhomogène des phases liquide et solide, temps de traitement longs, encapsulation d'agglomérats de poudre. Comme mentionné au début, la phase gazeuse est toujours présente si elle n'a pas été évacuée au préalable. Ici aussi, les mélangeurs sous vide rendent de précieux services.
- Dans des cas particuliers, un ingrédient actif poussiéreux et finement dispersé doit être appliqué uniformément à la surface d'un support en poudre. Cela devrait se faire sans le détour de l'agglomération des zones humides. Même un processus d'homogénéisation aussi complexe peut être facilement réalisé à l'aide de mélangeurs sous vide.
- Les processus de fermentation et de synthèse sont presque toujours achevés en phase humide. Le produit est ensuite évaporé ou déshumidifié mécaniquement lors d'une étape intermédiaire. L'étape finale de séchage peut à nouveau être réalisée de manière pratique dans un mélangeur sous vide chauffé.
- La substance active en poudre peut se sublimer. Cela signifie que l'ingrédient actif s'évapore en contournant la phase liquide. Dans un mélangeur sous vide, la sublimation peut être accélérée afin d'évacuer en toute sécurité le gaz en tant qu'ingrédient actif.
Les malaxeurs sous vide, qui réchauffent l'enrobé pendant le malaxage, sont de loin les plus importants. Cela se fait en plaçant une double enveloppe sur la chambre de mélange et sur l'outil de mélange. Des fluides caloporteurs (eau, vapeur ou huile thermique) circulent dans la double enveloppe et transmettent leur énergie thermique à l'objet à mélanger.
Séchage sous vide des mélanges
L'humidité résiduelle de l'enrobé est efficacement évaporée. L'enrobé sèche très rapidement et efficacement. Grâce au vide, le point d'ébullition baisse. Les substances actives sensibles à la chaleur peuvent ainsi être séchées rapidement et de manière économique. Ce sujet est traité dans des articles de blog sur ce site.
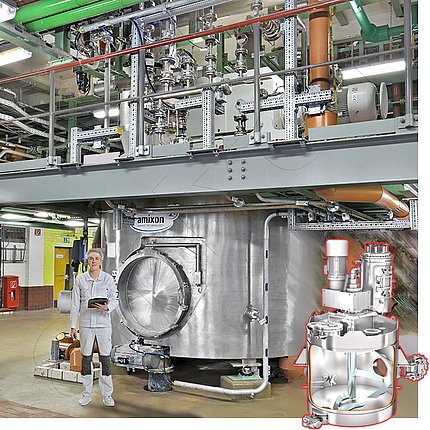
Évaporateur
Dans certains cas, les liquides doivent être évaporés. Cela se fait également de manière efficace et efficiente grâce à l'apport de chaleur et au vide. La technologie amixon vous permet de tester tous ces processus avec vos enrobés. Ce sujet est également traité dans des articles de blog sur ce site.