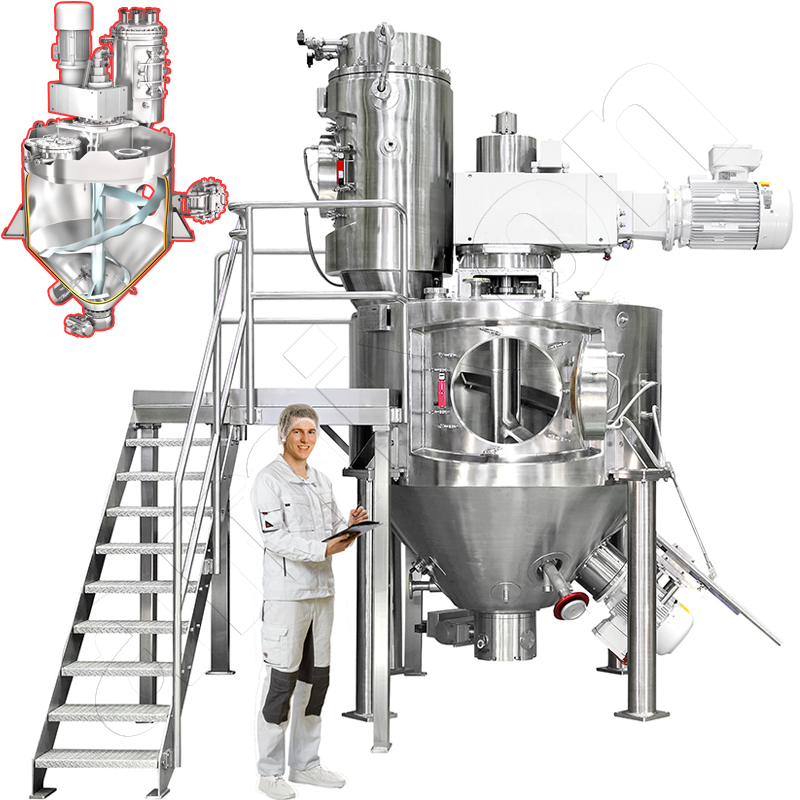
Vakuummischer
Der Druck wird in der physikalischen Einheit Pascal gemessen. 1 Pa = 1 N/m² = 0,01 mbar.
Zuweilen begegnet uns auch die ältere Maßeinheit Torr = 1 mm Hg-Säule = 1,333 mbar.
Die Güte eines Vakuums wird unterteilt in die Bereiche
- 1 bar bis 1 mbar Grobvakuum
- 1 mbar bis 10-3 mbar Feinvakuum
- 10-3 mbar bis 10-7 mbar Hochvakuum
- 10-7 mbar bis 10-10 mbar Ultrahochvakuum
In diesem Glossar verwenden wir den Begriff Vakuum/ Vakuummischer vereinfacht. Gemeint ist gemäß der vorstehenden Tabelle aber nur der Bereich „Grobvakuum“ und in Einzelfällen einen „Teil des Bereichs Feinvakuum“.
Vormerkung:
Wenn wir Schüttgüter auf eine Ebene schütten, entsteht ein kegelförmiger Haufen. Im Ruhezustand liegen die unterschiedlich geformten Partikeln gewissermaßen über- und nebeneinander. Jede Partikel befindet sich im Gleichgewicht. Die Kräfte, die auf eine einzelne Partikel wirken, sind: die Gravitationskraft, die Auflagekraft und die Kontaktkräfte benachbarter Partikel. Die Summe aller Kräfte, die auf die Teilchen wirken, ist Null. Aufgrund ihrer runden Form berühren sich die meisten Partikel nur punktuell. Zwischen den Partikeln gibt es viele Hohlräume. Auch ein einzelnes Partikel kann Hohlräume aufweisen. Man spricht hier von der Porosität eines dispersen Systems. In physikalischen Formeln wird für die Porosität meist der altgriechische Buchstabe für PHI verwendet. Die Porosität ist eine dimensionslose Größe. Sie ist ein Maß dafür, wie viel Gas/Luft in einem Schüttgut vorhanden ist.
Die Umgebungsluft enthält je nach Temperatur und Luftdruck mehr oder weniger Feuchtigkeit in Form von Wasserdampf. Das Wasser lagert sich in mikroskopisch kleinen Kondensatschichten an den Feststoffoberflächen an auch in den Poren der Partikel. Insofern sind Schüttgüter unter atmosphärischen Bedingungen dreiphasige disperse Systeme. Sie bestehen aus Feststoff, Flüssigkeit und Gas.
Die Gefäße von verfahrenstechnischen Maschinen wie Vakuummischer, Rührwerke, Mischer, Reaktoren, Abscheider etc. dürfen nur bis zu einem maximal zulässigen Füllgrad mit Produkt befüllt werden. Oberhalb der Mischgutschicht befindet sich in der Regel Umgebungsluft. Auch dieses Gasvolumen muss im Fall des Evakuierens entfernt werden.
Es gibt viele Gründe, warum ein Mischraum evakuiert werden muss. Einige davon sind:
- Vermeidung von Oxidation mit Luftsauerstoff,
- Vermeidung von Brand- und Explosionsgefahren,
- Vermeidung der Fluidisierung von Pulvern,
- Beseitigung von Gasüberdruck durch reaktive Gasbildung,
- Reduzierung des Systemdrucks zur Beschleunigung eines Trocknungsprozesses,
- Erzeugung einer intensiven Feststoffreibung zur Beschleunigung der Desagglomeration und der Diffusion innerhalb von Feststoffpartikeln,
- vorübergehende Erhöhung der Schüttdichte,
- Austausch des im Schüttgut enthaltenen Gases (Inertisierung mit Stickstoff oder Kohlendioxid)
- Entgasen von Flüssigkeiten,
- Entfernen von Luft, wenn Pulver pneumatisch in einen Behälter gesaugt oder eingeblasen wird,
- dies ist z.B. auch der Fall, wenn große Mengen Pulver in eine Flüssigkeit eingemischt werden (High-Shear-Mischtechnik mit Rotor-Stator-Konfiguration).
- wenn hochreine Substanzen synthetisiert werden,
- wenn sterile Bedingungen erforderlich sind,
- bei der Steuerung von Fermentationsprozessen,
- wenn disperse Systeme durch Enthalpieabsenkung gekühlt werden sollen,
- bei der Gefriertrocknung,
- wenn hochviskose Flüssigstoffe in Pulverpartikel imprägniert werden sollen
- ......
Die oben genannten Methoden können bei der industriellen Veredelung von Stoffen im Vakuummischer durchgeführt werden. Das ist beispielsweise der Fall für pharmazeutische Produkte, Kosmetika, chemische Wirkstoffe und Lebensmittel.
Um ein Vakuum erzeugen zu können, werden zwei Grundvoraussetzungen benötigt: Einen gasdichten/vakuumfesten Behälter und eine Vakuumpumpe.
Vakuummischer sind universell nutzbar.
Beim Evakuieren eines dispersen Systems wird das Gas in Richtung der Vakuumpumpe beschleunigt. Abhängig von der Gasgeschwindigkeit kann das strömende Gas ungewollt Staubpartikel aus der Schüttung mitreißen. Dies ist in den meisten Fällen unerwünscht. Deshalb werden der Vakuumpumpe Staubfilter vorgeschaltet. Bei der Auslegung von pneumatischen und vakuumtechnischen Systemen sind unter anderem folgende Leistungsparameter aufeinander abzustimmen:
- das Saugvermögen der Pumpe
- der Wirkungsgrad der Pumpe
- die Robustheit der Pumpe
- das effektive Saugvermögen
- die Saugleistung
- die Leitungslänge
- die Gasgeschwindigkeit
- Strömungswiderstand
- Filterfunktion
- Filterfläche
- Filterbelastung
- Filterabreinigung
- Filterkonditionierung
- Rüstzeit für den Fall der Reinigung/ Nassreinigung
- ...
Auch nasse oder feuchte Dispersionen müssen in vielen Fällen im Vakuummischer evakuiert/ vakuumgetrocknet werden. In diesem Fall ist das austretende Gas nicht nur staubig, sondern auch mit Wasserdampf oder Lösemitteldampf kontaminiert. Ein solches Gas wird in der Praxis als Brüden bezeichnet. Es kann nur in einem so genannten Brüdenfilter gereinigt werden. Das Filtergehäuse muss weit über die Taupunkttemperatur der flüssigen Phase aufgeheizt werden. Das gereinigte Gas kann dann optional in einem Wärmetauscher entfeuchtet werden. Die Lösemittel können auf diese Weise zurückgewonnen werden. Der zurückgespülte Staub gelangt zurück in den Vakuummischer.
Vakuummischer Anwendungsbeispiel bei der Herstellung von Nahrungsergänzungsmitteln
Vakuummischern bei der Herstellung von Nahrungsergänzungsmitteln auf der Basis von Proteinpulvermischungen:
Die Nährstoffzusammensetzung einer Eiweißpulvermischung besteht aus den Proteinquellen wie Molke, Kasein oder Soja. Diese werden mit weiteren pulverförmigen Zutaten wie Aminosäuren, Vitaminen, Mineralstoffen und Süßungsmitteln vermischt. Dabei spielt die Vakuumtechnik eine wichtige Rolle, um Oxidation zu vermeiden. Das in Dosen oder Beutel abgefüllte Pulver muss weitgehend frei von Sauerstoff und Feuchtigkeit sein.
Ein Vakuummischer kann hier hilfreich sein, indem die Mischgüter vor der Verpackung/Abfüllung im Mischer vom Luftsauerstoff befreit und anschließend mit einem Gemisch aus Kohlendioxidgas und Stickstoff auf Atmosphärendruck gebracht werden. Diese Maßnahme stabilisiert die Fließeigenschaften und verlängert die Haltbarkeit der Nährstoffzusammensetzung.
Vakuummischer Anwendungsbeispiel in der pharmazeutischen Industrie
Vakuummischer für feste pharmazeutische Wirkstoffe
müssen in anwendungsfreundliche Darreichungsformen wie Kautabletten, Brausetabletten, Schlucktabletten, Kapseln oder Zäpfchen überführt werden.
Zuvor müssen die Wirkstoffe mit Hilfe von Füllstoffen verdünnt werden. Dies geschieht in Pulvermischern. Manche Wirkstoffe sind extrem feinpartikulär, so dass ihre Stäube gebunden werden müssen. Dies geschieht durch Agglomeration im Wirbelschichtapparat oder im Vakuummischer. Agglomerationsvorgänge werden durch die Anwesenheit von flüssigen Bindemitteln begünstigt. Anschließend muss die flüssige Phase getrocknet werden. Der Trocknungsprozess wird durch das Anlegen eines Vakuums massiv beschleunigt. Durch die Absenkung des Systemdrucks verdampft das Wasser weit unter 100°C. Niedrige Trocknungstemperaturen sind auch bei thermisch empfindlichen pharmazeutischen Wirkstoffen hilfreich.
Luftsauerstoff kann die Haltbarkeit von festen Arzneimitteln negativ beeinflussen. Ein Inertisierungssprozess kann wie im vorhergehenden Kapitel beschrieben - mit Hilfe eines Vakuummischers - durchgeführt werden.
- Ein typischer galenischer Aufbereitungsprozess ist das sogenannte Verreiben von Wirkstoffen, um sie besonders gleichmäßig in einem pulverförmigen Füll- oder Hilfsstoff zu dispergieren. Diese Art der Desagglomeration kann im Vakuummischer wirkungsvoll unterstützt werden. Die innere Reifung der Schüttgutmischung wird erhöht und eine unerwünschte Fluidisierung sicher vermieden.
- Soll ein flüssiger Wirkstoff in das Innere von Füllstoffpellets eingebettet werden, ist ein Vakuummischer sinnvoll. Erst nachdem durch ein Feinvakuum der größte Teil der Luft aus den Poren der Füllstoffagglomerate entfernt wurde, wird der flüssige Wirkstoff in den Vakuummischer eingesprüht. Anschließend wird der Systemdruck langsam auf Atmosphärendruck erhöht. Das sogenannte Imprägnieren kann vorteilhaft unter Verwendung eines Inert- oder Edelgases erfolgen.
- Manchmal werden Arzneimittel in flüssiger Form verabreicht. In diesem Fall kann es erforderlich sein, pulverförmige Wirkstoffe in der Flüssigkeit zu dispergieren oder aufzulösen. Beim Einbringen und Verteilen von Pulvern in Flüssigkeiten können viele Probleme auftreten. Einige davon sind: unerwünschte Schaumbildung, inhomogene Verteilung der flüssigen und festen Phase, lange Prozesszeiten, Verkapselung von Pulveragglomeraten. Wie eingangs erwähnt, ist die Gasphase immer vorhanden, wenn sie nicht vorher evakuiert wurde. Auch hier leisten Vakuummischer wertvolle Dienste.
- In besonderen Fällen soll ein staubförmiger, feindisperser Wirkstoff gleichmäßig auf die Oberfläche eines pulverförmigen Trägermaterials aufgebracht werden. Dies soll ohne den Umweg der Feuchtagglomeration geschehen. Auch ein solch komplizierter Homogenisierungsprozess ist mit Hilfe von Vakuummischern komfortabel durchführbar.
- Fermentations- und Syntheseprozesse werden fast immer in der Nassphase abgeschlossen. Anschließend wird das Produkt entweder eingedampft oder als Zwischenschritt mechanisch entfeuchtet. Der abschließende Trocknungsschritt kann wiederum komfortabel in einem beheizten Vakuummischer erfolgen.
- Pulverförmiger Wirkstoff kann sublimieren. Das bedeutet, dass der Wirkstoff unter Umgehung der flüssigen Phase verdampft. In einem Vakuummischer kann die Sublimation beschleunigt werden, um das Gas als Wirkstoff sicher auszutragen.
Die weitaus größere Bedeutung haben Vakuummischer, die das Mischgut während des Mischens erwärmen. Dies geschieht durch Anbringen eines Doppelmantels am Mischraum und am Mischwerkzeug. Im Doppelmantel strömen Wärmeträger (Wasser, Dampf oder Thermalöl) und geben ihre Wärmeenergie an das Mischgut ab.
Vakuum-Mischtrocknung
Die Restfeuchte des Mischgut es wird effektiv verdampft. Das Mischgut trocknet sehr schnell und effektiv. Durch das Vakuum sinkt der Siedepunkt. Dadurch können wärmeempfindliche Wirkstoffe schnell und wirtschaftlich getrocknet werden. Dieses Thema wird in Blogbeiträgen auf dieser Homepage behandelt.
Eindampfer/ Verdampfer
In manchen Fällen müssen Flüssigkeiten verdampft werden. Auch dies geschieht effizient und effektiv durch Wärmezufuhr und Vakuum. Mit der amixon-Technologie können Sie all diese Prozesse mit Ihren Mischgütern testen. Auch dieses Thema wird in Blog-Beiträgen auf dieser Homepage behandelt.