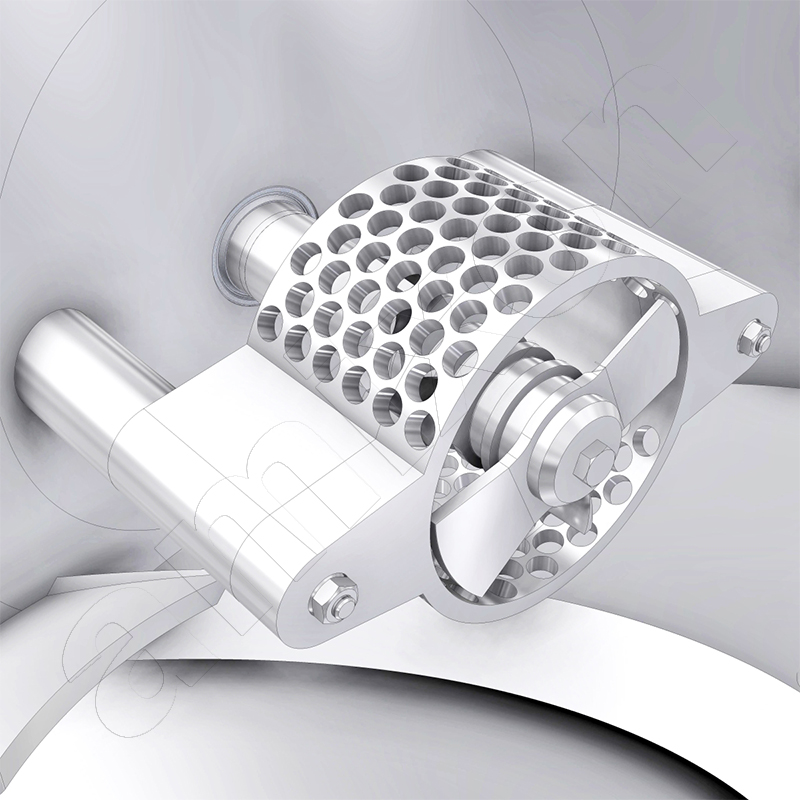
Deagglomeration
In the bulk goods industry, powdery goods are treated / refined / modified. It is fundamentally important to include all particles in the process. This is only possible if the primary particles are present individually, i.e. are not stuck together or clumped with other particles. The smaller the particle diameter of a powder, the stronger the effect of adhesion. This is due to interparticle forces (van der Waals forces, electrostatic attraction, atomic attraction or through liquid bridges). The generic term is agglomeration. Agglomerates are particle assemblies that contain many cavities (pores) due to random bridging. Crystalline substances can be bound together by their flat surfaces adhering to each other. They are then referred to as aggregates. The binding forces within such aggregates can be many times greater than the binding forces within agglomerates.
Deagglomeration means separating the particle structures described above. This can be difficult under certain circumstances. In amixon® mixers, such deagglomeration processes take place frequently. This is often done with the help of fast-rotating whirlers/cutting rotors and high-shear blades. Sometimes rotor-stator systems are also used.
amixon® mixers can effectively deagglomerate bulk materials without changing/damaging the primary particles.
Small amounts of anti-caking agents can be added to the mixing process to prevent re-caking / agglomeration. Their nanostructure coats the surfaces and prevents re-agglomeration/aggregation of the primary particles.
The deagglomeration processing step is important,
- if mixing processes are to achieve maximum homogeneity,
- if active pharmaceutical ingredients are to be effective in their entirety,
- if colour pigments are to achieve a high colour intensity,
- if chemical reactions are to include all particles,
- if .....