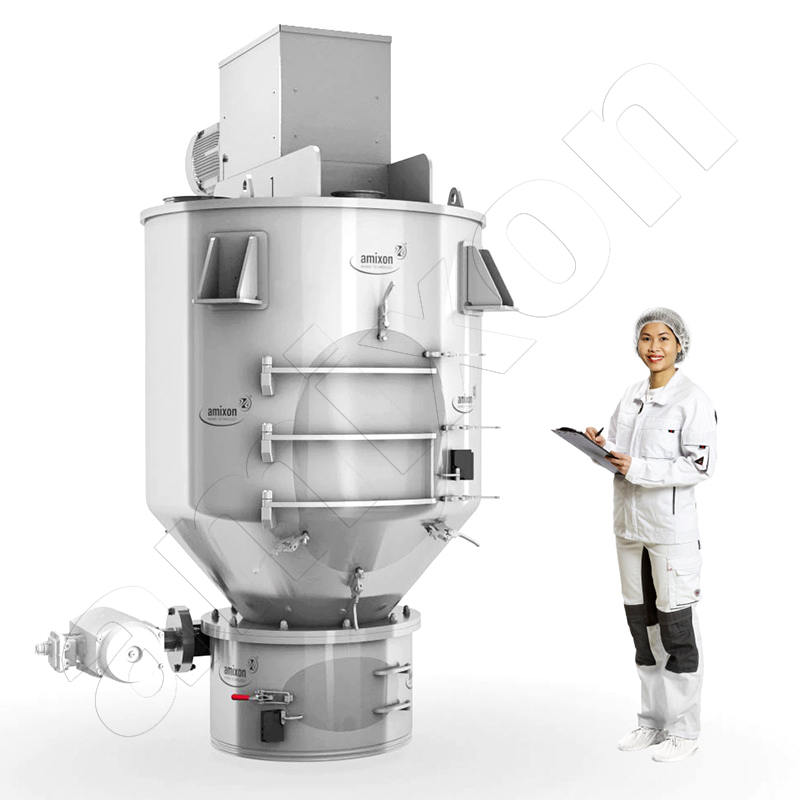
The amixon® KoneSlid® mixer for the powder preparation of sensitive bulk goods.
FAQ - KoneSlid® powder mixer by amixon®: why and what it is suitable for
What prompted you to develop such a conical powder mixer, type KS?
This mixer type was developed for the mixing of particularly sensitive components. These include the goods resulting from freeze-drying or produced in the spray tower and agglomerator. These are primarily instant nutrients or agglomerated medicinal ingredients with excellent instant properties. Ideally, these goods would be packaged directly from the plant; in sachets, in bags, in foil pouches, folding cartons or in cans.
Are we talking about mixed products whose ingredients must not be heated?
Yes, that's exactly what it's about. Often there are components that must not be exposed to the thermal treatment of a spray tower or an agglomerator, such as vitamin B2, probiotics, prebiotics, omega-3 fatty acid or omega-6 fatty acid, then a final mixing process after the spraying process is unavoidable. During mixing, these substances must be agitated only very gently – nearly unnoticeable.
In these cases, however, the very highest mixing quality is essential. Is this not a conflict of aims - on the one hand to mix homogeneously, on the other hand to maintain the particles in their existing granulometry? The process of discharge from the mixer can also stress the mixed materials. Especially if the mixed materials are to be discharged from the mixer quickly and without residue?
It may seem illogical, but it is possible to homogenize such mixing goods adequately and discharge them without residue.
This is done by three-dimensional rearrangement. A specifically shaped mixing spiral rotates at low rotational frequency and conveys the goods upwards in the periphery of the mixing chamber. The goods flow downward in the center. In the process, they are returned to the outside by the inner cone. The ideal mixing quality is achieved after only a few revolutions. The homogeneity corresponds to the best possible distribution and can no longer be improved in practice.
Is it true that a high mixing quality is only achieved when the mixing tool rotates at high speed?
This may be true for other mixing systems. For the mixer type presented here, the opposite is true. The entire content of the mixing chamber is completely conveyed and rearranged once after about 4-5 revolutions. This happens independently of the rotation frequency. As a rule, the ideal mixing quality is achieved after 8 to 20 revolutions. Then the conical closing element lowers and the goods flow out within a few seconds.
Is it then not irrelevant whether the mixing tool performs the mixing process with a lower or higher rotational frequency?
The consideration is indeed obvious. However, it must be borne in mind that the phenomena of wear and abrasion do not develop linearly with the relative speed. Often they even develop quadratically. This is the case when the mixing tool agitates the particles and when the particles flow relative to each other and rub against each other and "round off". Fine particles can then be produced. In this respect, the slow rotational movement of the mixing tool helix is of great importance.
Is there any other reason for using a vertical mixer of this type?
Yes, there undoubtedly are. It is the mundane things that can dominate everyday operations, for example when it comes to discharging residual material. The better a mixer discharges, the more effectively the mixing operation works. For the mixer described here, this means practically:
- virtually no product carry-over due to residual mix
- optional metering or emptying of the mixed goods within seconds
- virtually no mix residues that have to be disposed of when a recipe change has to be carried out
- All raw materials used are converted into high-quality selling goods.
- Sustainability is becoming increasingly important with regard to our resources and consumer acceptance!
There are practically no sources of contamination. The mixing tool is driven and supported only at the top. The high-quality PTFE lip seal only seals against dust and is subject to virtually no wear. A classic lip seal air purge can be provided, but need not be. In this respect, hardly any dust is generated in the mixing chamber.
We would also like to mention at this point that it is much more motivating for the plant operator to operate a plant with excellent ergonomic visibility. As a rule, he will enjoy using and maintaining it. This makes sense in view of the long service life of these mixers. They often operate for more than 30 years.
KoneSlid mixers can be installed directly above filling lines. They operate either continuously or in batches, accurately and extremely fast. They can be installed as end-of-the-line mixers at the end of a process chain above the filling machine.
Trials with your original products eliminate doubts and uncertainty. Come to our technical center in Paderborn and bring your mixed products with you. Cone mixers in various sizes are available here for your use. If you wish, you can also borrow our test machines. We recommend this procedure whenever a freshly produced powder changes in the course of the storage time.
© Copyright by amixon GmbH