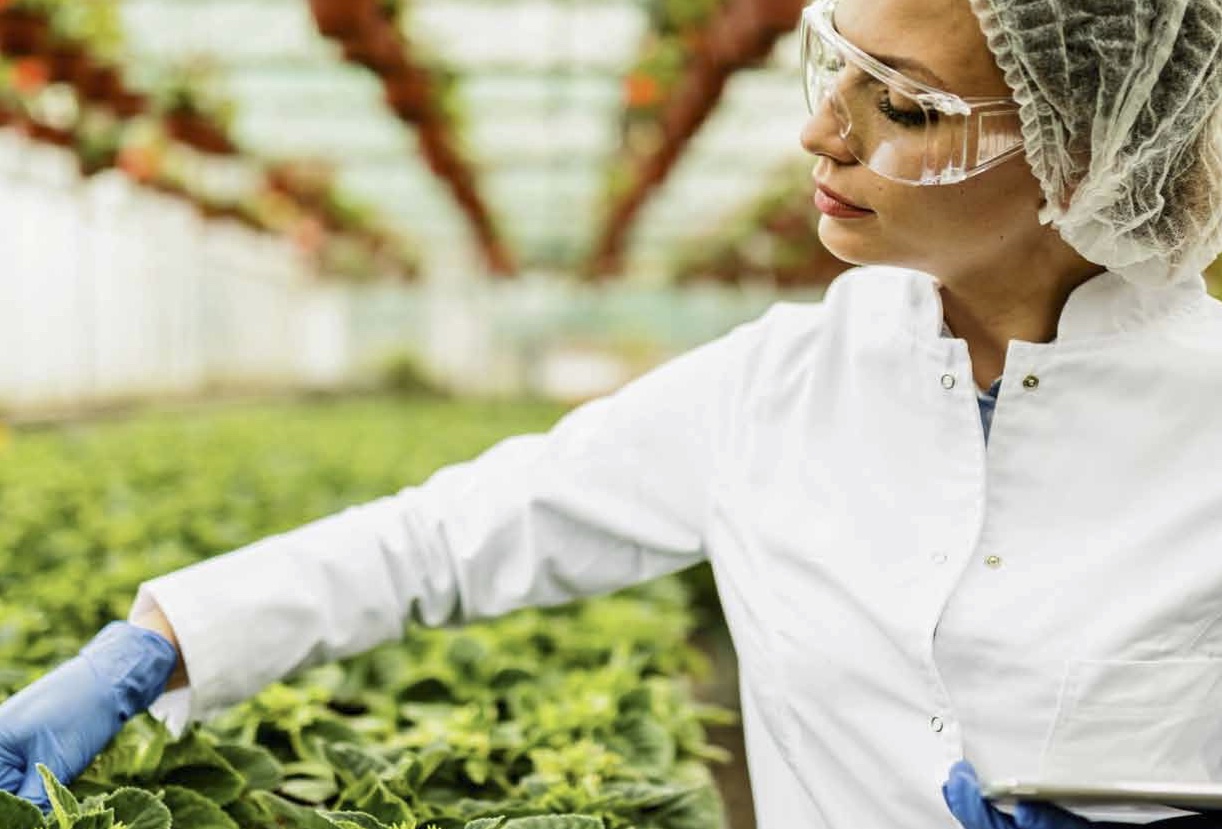
Today's crop protection products are highly effective and environmentally friendly..
Plant protection products (Part 2)
The production of crop protection agents requires high-performance synthesis plants. Modern active substances are the result of many synthesis steps. Even if the final product is non-toxic, the products of the intermediate stages can be hazardous substances. They leave the synthesis plant as highly concentrated chemicals. The process plants must therefore be permanently gas-tight, regardless of whether there is vacuum or overpressure present inside. This applies to all synthesis stages up to the final product.
Today's crop protection products are highly effective and environmentally friendly. Synthesis reactors from amixon GmbH have valuable features in terms of increased efficiency and operational reliability. This makes them very valuable for the plant.
The first part of the article dealt with the synthesis steps in the process of pesticide production and their technical solutions. In Part 2, the vacuum-drying and mixing-cooling process steps are examined in detail: What is the best way to avoid thermal stress in the equipment? What is the role of mixing ratios and heat transfer surfaces?
Paste bunkers/ blenders
If many different devices are interconnected in series in a plant, this is also referred to as a process line. Some equipment on the line may only work in batches, others may only work continuously, and still others may be used for both types of process. Critical points always arise whenever a system change from continuous to batch and vice versa takes place. In this case, the material flow must be collected in buffer vessels. Buffer vessels that can be used for wet goods are called paste bunkers.
Paste bunkers must be able to store wet chemicals in a gas-tight manner, discharge them as required and stop the discharge at any time. The residual emptying must be as high as possible, i.e. complete, regardless of the storage duration and regardless of the flowability of the moist goods. Paste bunkers must also function when the moist materials are time-solidified or behave dilatantly. Paste bunkers should move the mass as little as possible to preserve the grain structure (granulometry).
The lower part shows an example of a filter for solid-liquid separation. If possible, a continuously operating filter, e.g. a peeler centrifuge, is used here. Depending on the material properties, it may be necessary to dismantle the continuously operating centrifuge and replace it with a discontinuously operating chamber filter press. The choice of the filtration method depends on the efficiency and the achievable degree of dehumidification. In this context, the buffering effect of upstream and downstream equipment is essential.
At the end of the filtration process, the product is collected in a bin. At this stage, the product looks like a moist, crumbly bulk material. In reality, in most cases it is pseudo-viscous and its consistency changes quickly when stirred. Then it sometimes becomes sticky and adhesive like a cake batter. In some cases, it is necessary to heat or cool the wet chemicals, evacuate them or overlay them with inert gas.
Experience has shown that the conveying path from the paste bunker to the vacuum mixer dryer should be as short as possible. It is best to choose a downpipe that widens conically towards the bottom. Wherever possible, valves should be selected in such a way that they present no flow resistance when open.
Fast but gentle drying/ blending
For some active ingredients, the temperature must not exceed 35°C to avoid compromising the stability of the active ingredient. The drying step is preferably carried out in the amixon® vacuum mixer dryer. Due to the vacuum that is applied, this step must also be carried out in a batch process. The mixing tool is only mounted and driven at the top. In the amixon® dryer, all parts that come into contact with the product are heated: the entire mixing chamber, the mixing shaft, the mixing arms and the helix. The product is gently shovelled three-dimensionally. During the drying process, lumps may temporarily form. HighShearBlades deagglomerate the lumps when necessary.
The moisture content can range from 15 to 40 percent by mass. These are either water, solvents or various liquid mixtures. This type of vacuum contact drying has four main advantages:
- the evaporation of the fluids takes place at low temperatures
- the drying process is fast and energy-efficient
- drying takes place in a completely closed system
- the evaporated fluids remain largely intact and are reusable
- by adding sterile steam, the residues of the solvent can diffuse out
- the mixer dryer has good residual emptying rates.
amixon® spiral mixers/ blenders can have very large material and heat exchange surfaces.
The lower the drying temperature, the longer the drying process takes. The drying time can be shortened in a way that is gentle on the product if a particularly large amount of heat is introduced into the mix. Each particle should come into contact with the tempered surfaces of the mixer dryer as often as possible. Three-dimensional material flow at low mixer speed is essential. This is a challenge, however, because the rheology of the mixing goods changes as the liquid content decreases: It is not uncommon to have a well-flowing, pumpable suspension at the beginning, which then becomes highly viscous and pasty - similar to chewing gum - and gradually forms large, sticky lumps. As drying progresses, these lumps break down. The result is a homogeneous powder of the active ingredient.
The heat transfer medium is either fed via half-pipe coils or in the classic double jacket to all surfaces that come into contact with the mixing/drying goods. This also applies to the rotating mixing tool, whose shaft, mixing arms and spiral agitator are equipped with internal thermal fluid channels. The floor and the head area of the mixing chamber are also temperature-controlled.
Uniform temperature control is particularly challenging when the thermal fluid is introduced as steam and then leaves the apparatus as condensate. Then the enthalpy change of the thermal fluid ensures the input of particularly large amounts of heat into the mixing good.
Drying tests are normally carried out on a small scale. In order to extrapolate from such drying results to large dryers of 5 m³, 10 m³ or more, it is important to know the theoretical volume flow of the mixing goods in the mixer dryer. This allows the ratio of the heat exchange areas to the mass of the mixing material to be standardised. amixon has a reliable database and extensive field experience to back up the calculations.
amixon® mixer/ blenders coolers improve production efficiency
After drying, the mixing goods must be cooled before filling. Of course, cooling can also take place in the vacuum mixer dryer. In practice, however, an additional mixer cooler increases production efficiency. For example, an appropriately dimensioned mixer cooler below the vacuum dryer can significantly increase the output of a system. This unit then also handles the portion-wise filling of big bags, containers or even the feeding of automatically operating filling systems.
Batch cooling of large powder masses is not trivial, since
- The cooling surfaces and the dry particles can only touch each other at certain points, which does little to support the heat exchange.
- The thermal conductivity of powders is usually low.
- Any energy introduced by stirring/mixing increases the temperature of the material being mixed, which is actually supposed to be cooled.
- The temperature setback is limited to avoid unwanted condensation.
In order to meet all these requirements, very large heat exchange surfaces must be available and the mixing materials must only be moved with a very low energy input - this is where amixon mixer coolers can fully exploit their design advantages.
Formulation for placing on the market
In the so-called formulation line, the active ingredients are prepared in such a way that they can be safely packaged and labelled in accordance with the regulations of the country of destination. The formulation processes are, for example: Crushing, mixing, deagglomerating, compacting, filling and labelling.
Active substances in powder form must first be "diluted". Air jet mills micronise the active ingredients so finely that they aggregate with the carrier material without segregation. Besides water-soluble substances, bentonite, kaolin or limestone powder can also be used as a carrier material. Surface-active emulsifiers can also be used as wetting or adhesive agents. The mixing ratios are up to 1:5000. Achieving ideal mixing qualities in a particularly short time is a performance that modern precision mixers can achieve reproducibly today. If the requirement is then added that the precision mixer must be completely emptied within a few seconds, there are hardly any alternatives to the KoneSlid® mixer from amixon®. The mixing and wetting process is intensified by the amixon HighShearBlades. The more precisely the intensive mixer mixes and discharges, the safer the process.
After mixing, the powdered plant protection products are filled into small containers in such a way that they can be conveniently dissolved by the end user in suitable water preparations. In the process, a further dilution of 1:1,000 and more takes place.
The KoneSlid® mixer/ blender ...
... is a vertical precision mixer whose helical mixing tool is only supported and driven from above. The mixing tool is ideally aligned with the cylindrical-conical mixing chamber. The special feature is the likewise conically shaped displacer element at the bottom of the mixer. The displacement element benefits the dead-space-free flow of the mixing goods during mixing and it causes the extremely fast residual emptying of the mixed material when it moves a few centimetres downwards.
The formulation lines are operated on a campaign basis. This is followed by thorough wet cleaning. The KoneSlid® mixer can also perform this wet cleaning and drying automatically thanks to built-in Washing-in-Place orbital cleaners. The wet cleaner is then blown out with compressed air and dried.
The KoneSlid® mixer has several large inspection doors for easy maintenance.
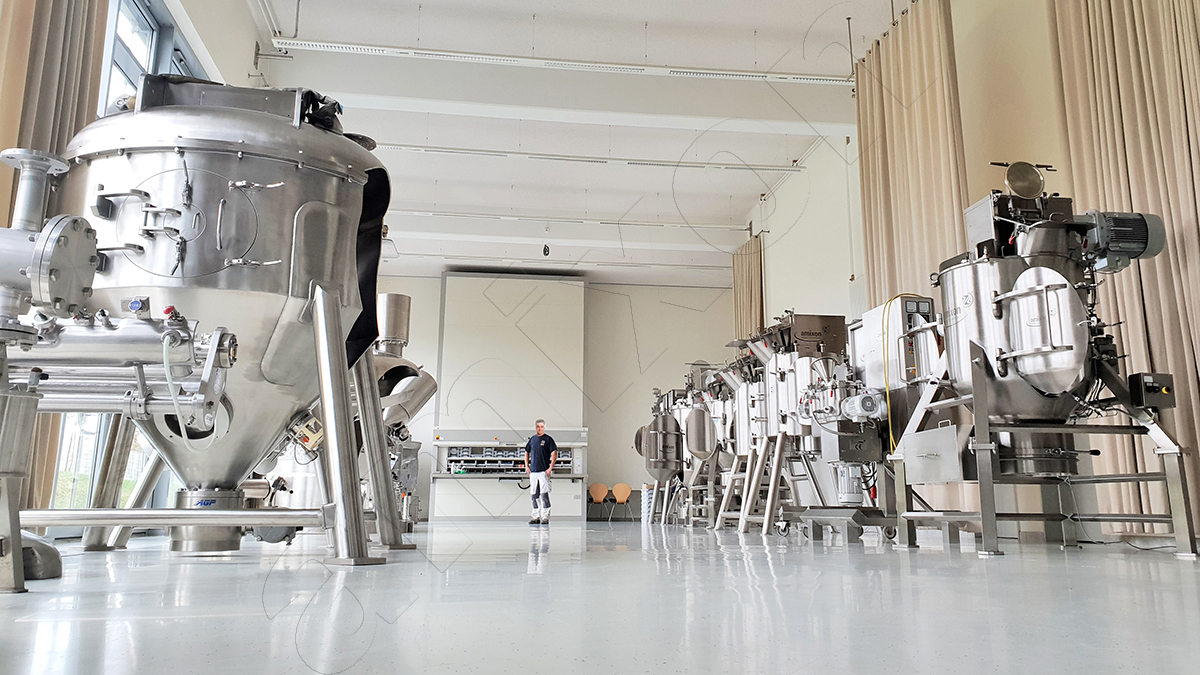
The amixon® test centre has more than 30 different test machines available for trials.
Process development and process optimisation
The development of new crop protection products is a lengthy and costly process, as explained above. It takes about ten years of intensive development work before a plant protection product can be approved and launched on the market. Promising new substances are sought in the laboratory and tested in model trials. The amixon® test centre is open to you. Do not hesitate to contact us even with difficult tasks. In the vast majority of cases we can answer you with good results.
© Copyright by amixon GmbH