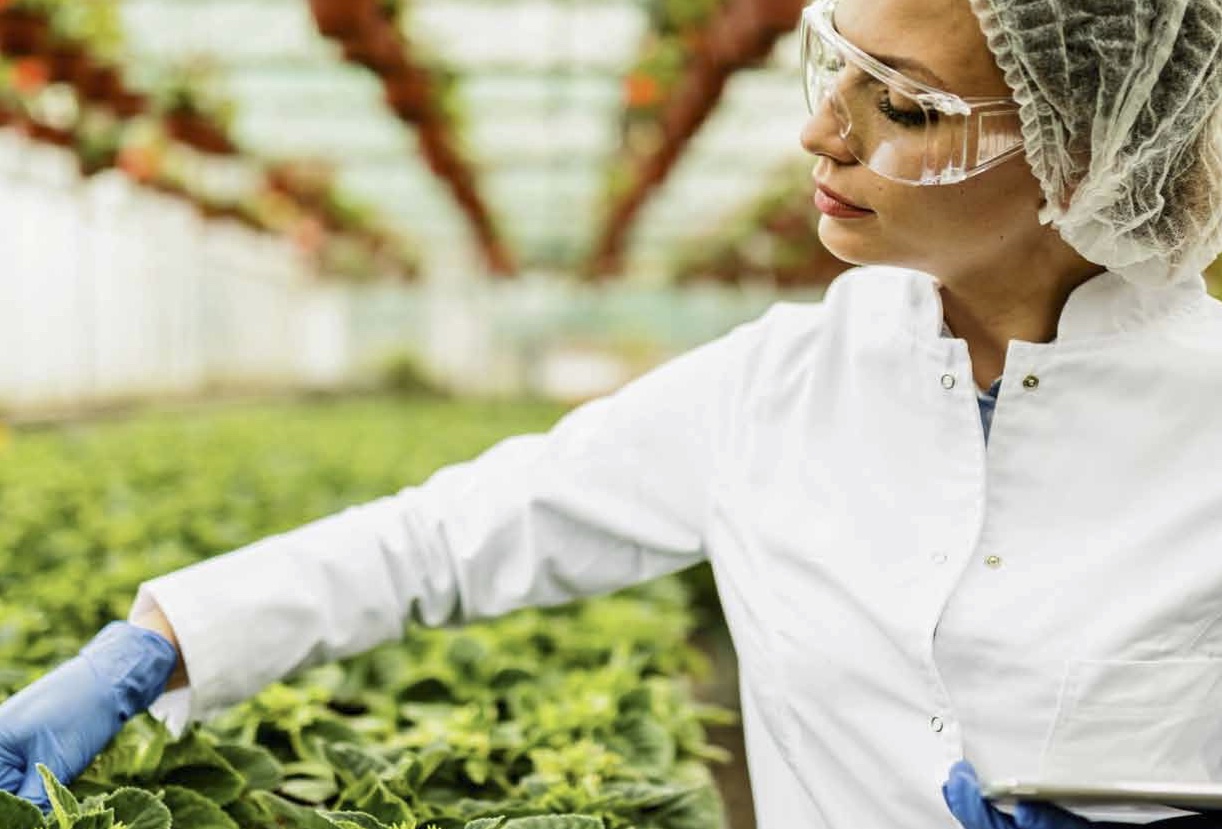
Los productos fitosanitarios actuales son muy eficaces y respetuosos con el medio ambiente.
Productos fitosanitarios (Parte 2)
La producción de productos fitosanitarios requiere plantas de síntesis de alto rendimiento. Las sustancias activas modernas son el resultado de muchos pasos de síntesis. Aunque el producto final no sea tóxico, los productos de las etapas intermedias pueden ser sustancias peligrosas. Salen de la planta de síntesis en forma de sustancias químicas altamente concentradas. Por ello, las instalaciones de proceso deben ser permanentemente estancas a los gases, independientemente de que en ellas haya vacío o sobrepresión. Esto se aplica a todas las fases de síntesis hasta el producto final.
Los productos fitosanitarios actuales son muy eficaces y respetuosos con el medio ambiente. Los reactores de síntesis de amixon GmbH presentan valiosas características en términos de mayor eficiencia y fiabilidad operativa. Esto los hace muy valiosos para la empresa.
La primera parte del artículo trataba de las etapas de síntesis en el proceso de producción de pesticidas y sus soluciones técnicas. En la Parte 2, se examinan en detalle las fases del proceso de secado al vacío y mezclado-enfriado: ¿Cuál es la mejor manera de evitar el estrés térmico en los equipos? ¿Qué papel desempeñan los grados de mezcla y las superficies de intercambio térmico?
Búnker de solución amortiguadora / búnker de pasta
Si en una planta hay muchos equipos diferentes conectados en serie, también se habla de línea de proceso. Algunos aparatos de la calle sólo funcionan por lotes, otros sólo de forma continua y otros pueden utilizarse para ambos tipos de proceso. Los puntos críticos siempre surgen cuando se produce un cambio de sistema de continuo a discontinuo y viceversa. Allí, el flujo de material debe recogerse en contenedores intermedios. Los depósitos que pueden utilizarse para productos húmedos se denominan depósitos de pasta.
Los depósitos de pasta deben poder almacenar productos químicos húmedos de forma estanca a los gases, descargarlos cuando sea necesario y detener la descarga en cualquier momento. El vaciado residual debe ser lo más alto posible, es decir, completo, independientemente del periodo de almacenamiento y de la fluidez de la solución humectante. Los búnkeres de pasta también deben funcionar cuando los materiales de amortiguación se solidifican con el tiempo o se comportan de forma dilatada. Los búnkeres de pasta deben mover la masa lo menos posible para preservar la estructura del grano (granulometría).
La parte inferior muestra un ejemplo de filtro para la separación sólido-líquido. Si es posible, se utiliza aquí un filtro de funcionamiento continuo, por ejemplo, una centrifugadora peladora. Dependiendo de las propiedades del material, puede ser necesario desmontar la centrifugadora de funcionamiento continuo y sustituirla por un filtro prensa de cámara de funcionamiento discontinuo. La elección del método de filtración depende de la eficacia y del grado de deshumidificación que se pueda conseguir. En este contexto, no se puede prescindir del efecto amortiguador de los aparatos anteriores y posteriores.
Al final de la filtración, el producto se recoge en una tolva. En esta fase, el producto parece un material a granel húmedo y desmenuzable. En realidad, en la mayoría de los casos es pseudoviscosa y su consistencia cambia rápidamente al agitarla. A veces se vuelve pegajosa como la masa de un pastel. A veces es necesario calentar o enfriar, evacuar o cubrir los productos químicos húmedos con gas inerte.
La experiencia ha demostrado que el trayecto de transporte desde la tolva de pasta hasta el secador mezclador de vacío debe ser lo más corto posible. Lo mejor es elegir un tubo de bajada que se ensanche de forma cónica hacia la parte inferior. Si es posible, los racores deben seleccionarse de forma que no ofrezcan ninguna resistencia al flujo cuando estén abiertos.
Secado rápido pero suave
En el caso de algunas sustancias activas, la temperatura no debe ser superior a 35 °C para no poner en peligro la estabilidad de la sustancia activa. La etapa de secado se realiza ventajosamente en el secador mezclador al vacío amixon®. Debido al vacío aplicado, este paso también debe realizarse por lotes. El mezclador sólo se monta y acciona en la parte superior. En el secador amixon®, se calientan todas las piezas que entran en contacto con el producto: toda la cámara de mezcla, el eje de la unidad de mezcla, los brazos de la unidad de mezcla y la hélice. El producto se palea suavemente en tres dimensiones. Durante el proceso de secado, pueden formarse temporalmente grumos. Las cuchillas HighShear desaglomeran los grumos cuando es necesario.
El contenido de humedad puede oscilar entre el 15% y el 40% en masa. Se trata de agua, disolventes o diversas mezclas de líquidos. Este tipo de secado por contacto al vacío presenta cuatro ventajas principales:
- la evaporación de los fluidos se produce a bajas temperaturas
- el proceso de secado es rápido y eficiente desde el punto de vista energético
- el secado tiene lugar en un sistema completamente cerrado
- los fluidos evaporados permanecen prácticamente intactos y son reutilizables
- añadiendo vapor estéril, los residuos del disolvente pueden difundirse fuera
- el secador mezclador tiene buenos índices de vaciado residual.
Las mezcladoras en espiral amixon® pueden tener zonas de intercambio de calor y de caldo muy grandes
Cuanto más baja sea la temperatura de secado, más tiempo durará el proceso de secado. El tiempo de secado puede acortarse de forma respetuosa con el producto si se introduce una cantidad especialmente grande de calor en la mezcla. Cada partícula debe entrar en contacto con las superficies templadas del secador mezclador con la mayor frecuencia posible. Aquí se requiere un flujo tridimensional del material a mezclar a una frecuencia de rotación baja de la mezcladora. Sin embargo, esto supone un reto porque la reología de la mezcla cambia a medida que disminuye el contenido líquido: No es infrecuente tener al principio una suspensión bien fluida y bombeable, que luego se vuelve muy viscosa y pastosa -similar a la goma de mascar- y poco a poco forma grumos grandes y pegajosos. A medida que avanza el secado, éstos se desintegran y al final queda un polvo homogéneo de principio activo.
El medio de transferencia de calor llega a través de serpentines de medio tubo o en la clásica doble camisa a todas las superficies que entran en contacto con el material de mezcla/secado. Esto también se aplica a la herramienta mezcladora giratoria, cuyo eje, brazos mezcladores y agitador en espiral están equipados con guías internas de fluido térmico. El suelo y la zona de la cabeza de la cámara de mezcla también están atemperados.
El control uniforme de la temperatura es especialmente difícil cuando el fluido térmico se introduce como vapor y luego sale del aparato como condensado. Entonces, el cambio de entalpía del fluido térmico garantiza la entrada de cantidades especialmente grandes de calor en la mezcla.
Las pruebas de secado suelen realizarse a pequeña escala. Para extrapolar estos resultados de secado a secadores grandes de 5 m³, 10 m³ o más, es importante conocer el flujo volumétrico teórico del material mezclado en el secador mezclador. Esto permite normalizar la relación entre las superficies de intercambio térmico y la masa de mezcla. En este caso, amixon cuenta con una importante base de datos y una amplia experiencia sobre el terreno para respaldar las proyecciones.
Las mezcladoras-nebulizadoras amixon® mejoran la eficacia de la producción
Tras el secado, las mezclas deben enfriarse antes del llenado. Por supuesto, el enfriamiento también puede tener lugar en la mezcladora-secadora al vacío. En la práctica, sin embargo, un mezclador refrigerador adicional aumenta la eficiencia de la producción. Un mezclador-refrigerador de dimensiones adecuadas situado debajo del secador al vacío puede aumentar considerablemente el rendimiento de un sistema. También se encarga del llenado por porciones de big bags, contenedores o de la alimentación de sistemas de llenado de funcionamiento automático.
El enfriamiento por lotes de grandes masas de polvo no es trivial, ya que
- Las superficies refrigerantes y las partículas secas sólo pueden tocarse en determinados puntos, lo que contribuye poco al intercambio de calor.
- La conductividad térmica de los polvos suele ser baja.
- Cualquier energía introducida por la agitación/mezcla aumenta la temperatura del material que se está mezclando, que en realidad se supone que debe enfriarse.
- La reducción de la temperatura está limitada para evitar condensaciones no deseadas.
Para cumplir todos estos requisitos, se debe disponer de superficies de intercambio de calor muy grandes y los materiales de mezcla sólo se deben mover con un aporte de energía muy bajo: aquí es donde los refrigeradores mezcladores de amixon pueden aprovechar al máximo sus ventajas de diseño.
Formulación para la comercialización
En la denominada línea de formulación, los principios activos se preparan de forma que puedan -según el país de destino- envasarse y etiquetarse correctamente para que lleguen al mercado de forma segura. Los procesos de formulación son, por ejemplo: Triturar, mezclar, desaglomerar, mezclar, compactar, llenar y etiquetar.
Las sustancias activas en polvo deben "diluirse" previamente. Los molinos de chorro de aire micronizan los ingredientes activos tan finamente que se agregan al material portador sin segregarse. Además de las sustancias hidrosolubles, también se puede utilizar bentonita, caolín o polvo de piedra caliza como material de soporte. Los emulsionantes tensioactivos también pueden utilizarse como agentes humectantes o adhesivos. Las proporciones de mezcla son de hasta 1:5000. Conseguir calidades de mezcla ideales en un tiempo especialmente corto es una hazaña que las mezcladoras de precisión modernas pueden realizar hoy en día de forma reproducible. Si a ello se añade el requisito de que la mezcladora de precisión debe vaciarse por completo en pocos segundos, apenas existen alternativas a la mezcladora KoneSlid® de amixon®. El proceso de mezcla y humectación se intensifica gracias a las cuchillas amixon HighShearBlades. Cuanto más precisa sea la mezcla y la descarga de la mezcladora intensiva, más seguro será el proceso.
Una vez mezclados, los productos fitosanitarios en polvo se envasan en pequeños recipientes de forma que el usuario final pueda disolverlos cómodamente en preparados de agua adecuados. En el proceso, se produce una dilución adicional de 1:1.000 y más.
El mezclador KoneSlid®...
... es una mezcladora de precisión vertical cuya herramienta de mezcla helicoidal sólo se apoya y se acciona desde arriba. La herramienta de mezcla está adaptada de forma óptima a la cámara de mezcla cilíndrico-cónica. La característica especial es el cuerpo desplazador de forma igualmente cónica situado en la parte inferior de la mezcladora. El cuerpo de desplazamiento favorece el flujo sin espacios muertos del material mezclado durante la mezcla y provoca el vaciado residual extremadamente rápido del material mezclado cuando se desplaza unos centímetros hacia abajo.
Las líneas de formulación funcionan por campañas. A continuación, se realiza una limpieza en húmedo a fondo. La mezcladora KoneSlid® también puede realizar esta limpieza en húmedo y el secado de forma automática gracias a los limpiadores orbitales Washing-in-Place incorporados. A continuación, el limpiador húmedo se sopla con aire comprimido y se seca.
El mezclador KoneSlid® es fácil de mantener gracias a varias puertas de inspección de gran tamaño.
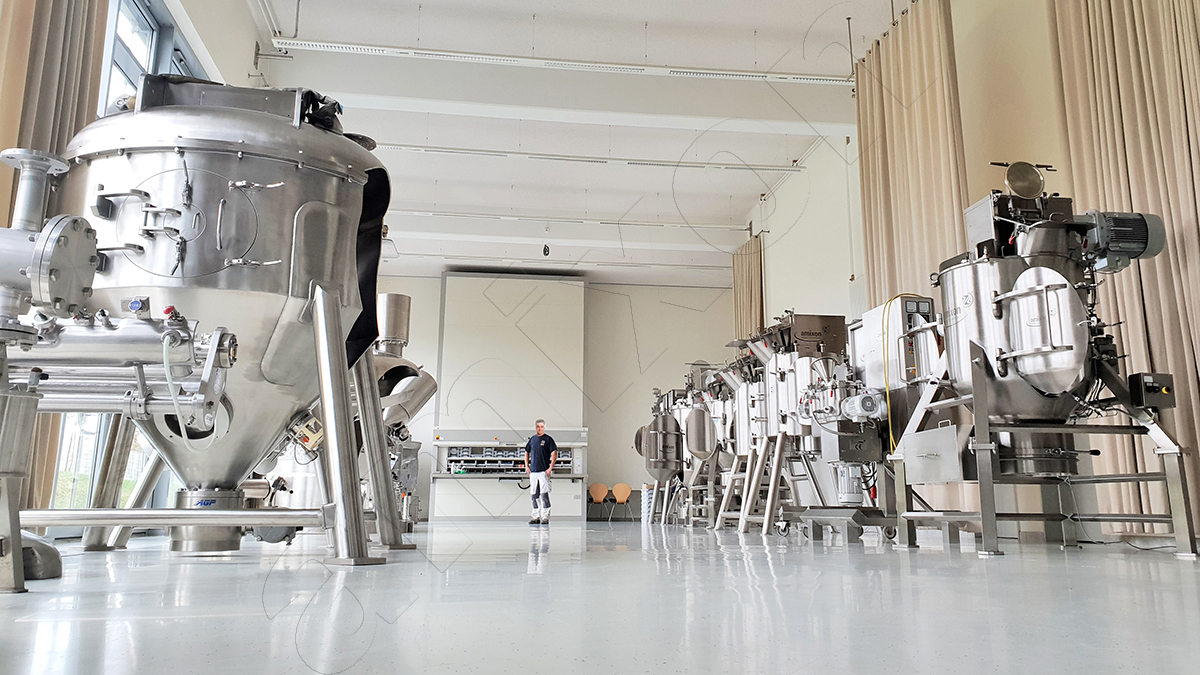
El centro técnico de amixon® dispone de más de 30 máquinas de ensayo diferentes para realizar pruebas.
Desarrollo y optimización de procesos
Ya se ha explicado que el desarrollo de nuevos productos fitosanitarios es largo y costoso. Se necesitan unos diez años de intenso trabajo de desarrollo antes de que un producto fitosanitario pueda ser aprobado y lanzado al mercado. Se buscan nuevas sustancias prometedoras en el laboratorio y se prueban en ensayos con modelos. El centro técnico amixon® está a su disposición. No dude en ponerse en contacto con nosotros incluso para tareas difíciles. En la inmensa mayoría de los casos podemos responderle con buenos resultados.
© Copyright by amixon GmbH