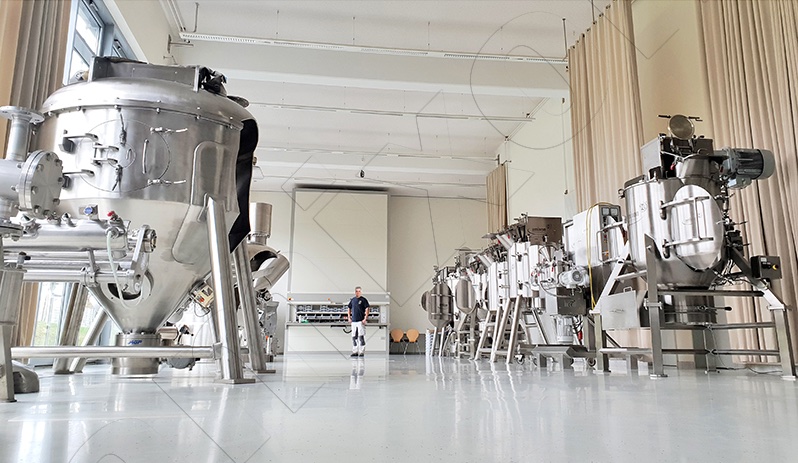
We have over 30 test mixers available in the amixon® Technika. The probability is very high that we will find the ideal solution for your requirement. Then we carry out the test with your original product.
amixon® showroom in Paderborn; two pilot plants are located next door
What do you recommend when powdery substances are modified or newly developed? ... or if a powdery product should be produced with a new process technology? How can you pilot the transition from laboratory scale to industrial scale?
We are approached with these questions from a wide variety of industries. amixon® has already provided process engineering support for many product developments. More than 30 different test machines are available to you in Paderborn alone: Powder mixers, vacuum dryers, synthesis reactors and granulators. This allows you to find optimal solutions.
Your tests can take place on a small scale. It is sufficient if 5-10 liters of mixing goods are available. Mixing tests are particularly meaningful whenever the test batch has the volume of about 400 liters. Mixing qualities, mixing times and technical design parameters can then be calculated by amixon - regardless of whether your production apparatus should later process batches of 400 liters or 10,000 liters.
Assuming the mixing tests on a 400 liter scale were successful, but later the batch size is supposed to be 2000 or 10 000 liters. Can test results be transferred to other sizes?
For complicated mixing tasks, it is advisable to be able to carry out two to three mixing trials with the same product and have 400 liters available for each. With the help of our measurements and our process database, amixon® can then convert a lot of data to larger devices.
Can the tests also be used to determine whether a sensitive powder forms dusty abrasions during mixing? What do you suggest if spray-dried mixes are particularly sensitive to pressure, shear or mechanical conveying. Is it possible that the instant properties of the powder could then be lost during mixing?
Hundreds of amixon® mixers are in use worldwide for precisely these tasks. Therefore, amixon® is aware of the great significance of your question.
The instant properties of spray-dried powders are characterized by particle structure and porosity, settling behavior, complete dispersibility, and prevention of lumps. If these properties change, the powder can become worthless.
If your sprayed products are mixed in an amixon® test mixer, you can be sure that this happens with minimal energy contribution. Your goods are homogenized in a technically ideal way in the amixon® twin-shaft mixer. This happens with ideal gentleness.
Unfortunately, the breakage of particles and the formation of dust during a mixing process cannot be calculated, at best estimated. Only tests can answer the question.
Is amixon able to provide suitably sized mixers on a trial basis?
Yes, we are able to do this. Large mixers are also available in the technical center. This is because only a real-scale trial can answer these quality-relevant questions (particle retention, dust formation, retention of bulk density, retention of instant properties). amixon® places great importance on preventing all risks that can be avoided in advance of a supply contract. This is the only way to guarantee
- that powder properties are maintained with ideal mixing quality and
- that your newly installed mixing plant can be put into operation immediately.
By the way, this test procedure is just as valid for the homogenization of high-quality instant meals, coated powders, or for flakes and sensitive muesli!
Are your statements above also relevant for the amixon synthesis reactors and vacuum dryers?
Yes, this is the case without restriction. The amixon® synthesis reactors and vacuum blade dryers also operate with optimally adapted energy input.
Please follow our invitation to Paderborn. We will be pleased to examine your tasks in the test center of amixon GmbH. We assure you first-class test results in advance. We also promise you a high gain in knowledge. During the plant tour you will see excellent manufacturing quality and depth.
© Copyright by amixon GmbH