Batch vs. continuous powder mixing
Determining the right powder mixing equipment for your production process
Industrial powder mixing techniques vary greatly depending on the application. While there are many types of mixers and processing methods, all industrial powder mixing processes can be defined as either continuous or batch mixing systems:
- Batch mixer
Ingredients are fed into the mixer, processed until the powder is homogeneous and then discharged as a single batch. Mixing a new batch requires repeating these steps, perhaps with additional intermediate steps to clean the mixer between batches. As batch mixing is a sequential process, output is measured in kilograms per batch or litres per batch.
- Continuous mixers
A continuous stream of ingredients enters the mixer from above. The ingredients are processed as they pass through the mixer and a continuous stream of homogenised powder flows out of the discharge nozzle. Each stage of a continuous flow process takes place continuously and simultaneously within a specified time frame, so its output is measured in kilograms per hour or litres per hour.
When selecting powder processing equipment, many factors can influence whether a batch or continuous process is the better choice. While both continuous and batch mixing have their advantages and disadvantages, and both methods are perfectly legitimate ways to mix powders, one or the other may be better suited to your product or processing environment.
Here you can see two different methods of continuous blending/ mixing / homogenising / deagglomerating / agglomerating / drying / drying / mixing.
Here are the key differences between batch and continuous mixing in powder processing, their respective advantages and disadvantages, and a selection of amixon® mixers suited for these processing methods.
Powder processing in batch mixers
Batch mixing finds application across diverse manufacturing and processing industries to create products in specified amounts or groupings. Common examples of powdery products that are processed in batch mixers include pharmaceuticals, cosmetics, nutritional supplements, and baby formula.
Advantages of batch powder blending/ mixing
In powder/bulk processing, batch mixing systems have the following key advantages over continuous mixers:
- Fine-tune the mixing process - Because each batch can be precisely adjusted, batch mixing is often preferred for products that must undergo stringent quality testing, such as pharmaceutical powders. This flexibility also makes batch mixing ideal for powdered ingredients that are chemically sensitive and tend to change over time.
- Mix multiple formulations with the same equipment - From batch to batch, the same mixer can be used to mix any number of different ingredients and formulations. This can be particularly beneficial when mixing different flavours of the same product, such as muesli or cereal variations.
- Pre-mixing capability - Batch mixers allow a portion of the ingredients to be blended first, before additional ingredients are added. In this way, batch mixers can perform multiple mixing operations, such as intensively deagglomerating additive ingredients before gently homogenising them with the bulk material.
- Traceability of products to a specific batch - After discharge, the final mixed product can be labelled with a batch number. Batch mixing makes it easy to identify which products have been mixed and when, should follow-up be required. Traceability makes batch blending well suited to blending pharmaceuticals or other highly regulated products where documentation of batch integrity is critical.
- Ideal for lower capacity facilities - Batch mixers generally have lower operating and installation costs than continuous mixers. This is particularly true for facilities that don't need to mix large volumes of powder at high speeds.
Disadvantages of batch powder mixing/blending
Compared to continuous mixers, batch mixers have the following limitations and disadvantages:
- Downtime between batches - Downtime is inherent in batch mixing because only one stage of the production process can take place at a time: Filling, mixing, discharging, cleaning. While one stage is in progress, all others must stop.
- Labour intensive - Batch mixing involves multiple steps and changeovers, which can make the powder mixing process more manual than a continuous flow process.
- Increasing output means increasing mixer size - In general, a larger batch mixer is required to achieve a higher batch yield. Smaller facilities may not have the space for a batch mixer large enough to produce the desired kg/hr output.
- Not ideal for large scale production of base row material - as batch mixing processes are generally slower and more labour intensive than continuous flow processes.
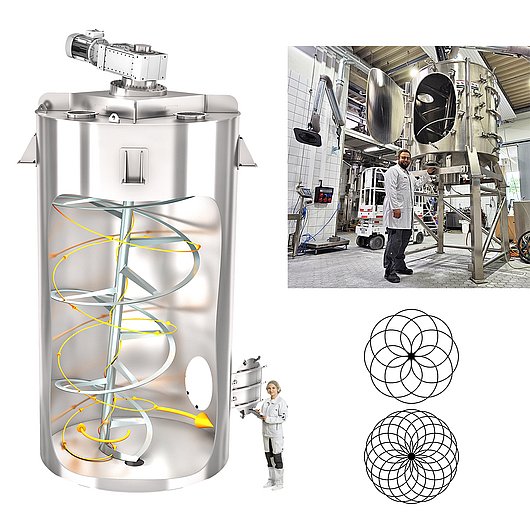
Innovations in powder processing
While batch mixing may be limited in these ways, innovations in powder processing and large batch technology have made tremendous strides in improving cycle times and efficiency. Two important innovations are: KoneSlid® blender and Gyraton® blender. A SpherHelics® blender is also mentioned.
See more innovations in powder processing here.
ComDisc®, a proprietary technology from amixon®, enables batch mixers to be rapidly discharged with a product yield of up to 99.997%. Furthermore, amixon® batch mixers are designed with large inspection doors that give ergonomic access to the mixing chamber, cutting down on cleaning and drying time between batches.
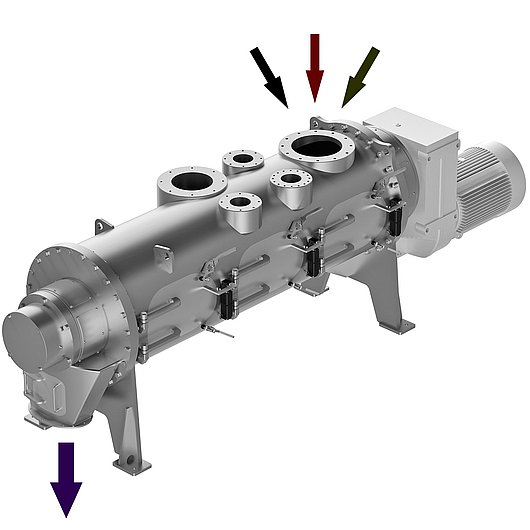
Powder processing in continuous mixers
Continuous mixing is preferred in large-scale powder processing applications requiring that a single blend is produced at a rapid rate. Many dry and powdery food products are mixed in continuous flow processes, from instant beverage granules to assorted snack foods. Granulators and powder agglomerators are common examples of mixing equipment that typically operate continuously.
Advantages of continuous powder mixing
In powder processing, continuous mixing systems have the following key advantages over batch mixers:
- Greater efficiency - In a continuous process, every stage of mixing, from loading to mixing to discharging, takes place simultaneously and without interruption. Continuous powder mixing eliminates both downtime between batches and the manual labour required for changeovers.
- High output in a compact size - Compared to a batch mixer of similar volume, continuous powder mixers can produce much higher volumes of mixed product in a given time. Even processing facilities with severe space limitations can mix large volumes of powder using a continuous mixer.
- Less resource-intensive to operate - In addition to their smaller size, continuous powder mixers generally require less power and manual labour than a batch mixer would to process the same volume of mixed goods.
- Automation-friendly - Continuous mixers are ideal for automated production environments as their operation can be programmed and monitored using IoT technology.
- Minimised segregation and product loss - Because the product is discharged from a continuous mixer in a continuous flow, less product is lost to residue and segregation.
Disadvantages of continuous powder mixing
Compared with batch mixers, continuous mixers have the following limitations and disadvantages:
- Limited precision – Especially if many ingredients are to be blended, continuous powder mixing processes may not be capable of mixing exact formulations requiring strict blend uniformity. This makes continuous mixers unsuitable for many critical applications, such as mixing pharmaceutical powders or fine ceramics.
- Reduced flexibility –Continuous powder mixers are usually programmed for one specific formulation and their settings cannot be quickly changed to process different formulas or volatile materials. This lack of flexibility makes continuous mixing less than ideal for processing chemically sensitive powders or variable products.
- Extensive ongoing maintenance –Continuous mixers are part of an ecosystem of processing equipment, and so any malfunction can bring the entire production line to a halt. Meticulous calibration and ongoing maintenance are crucial to preventing stoppage.
- Require a robust sampling and testing procedure – Keeping track of the quality of powders mixed in continuous flow processes can be a complicated endeavor, because contaminants or variations in blend uniformity cannot be traced back to a single batch. In industries where consumer safety is a concern, a robust quality assurance program would be needed.
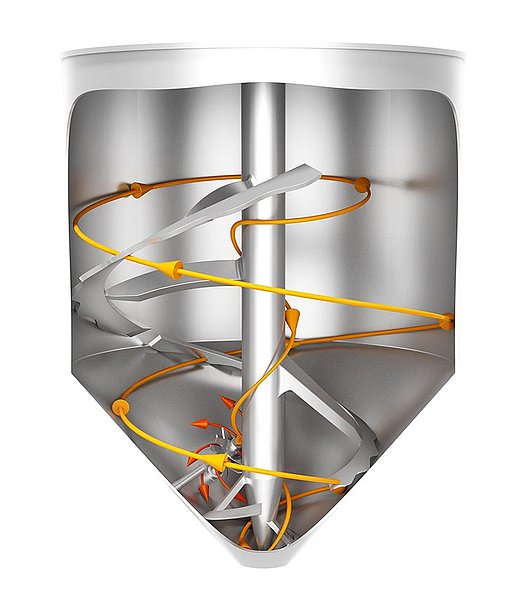
Batch and continuous powder mixer models
amixon® mixing technologists have engineered a conical powder mixer with a spiral mixing blade capable of operating either as a batch mixer or a continuous mixer. The AM batch mixer and AMK continuous mixer both initiate a three-dimensional flow within the mixing goods and can be programmed for a range of mixing intensities from gentle homogenization to intensive deagglomeration.
Whether your process requires a continuous mixer or a batch mixer, the amixon® team of engineers collaborates with you to determine and calibrate the precise filling levels, mixing retention, and cycle times for your powder mixing equipment.
The result is a powder mixer that is expertly customized to both your product and your workflow.