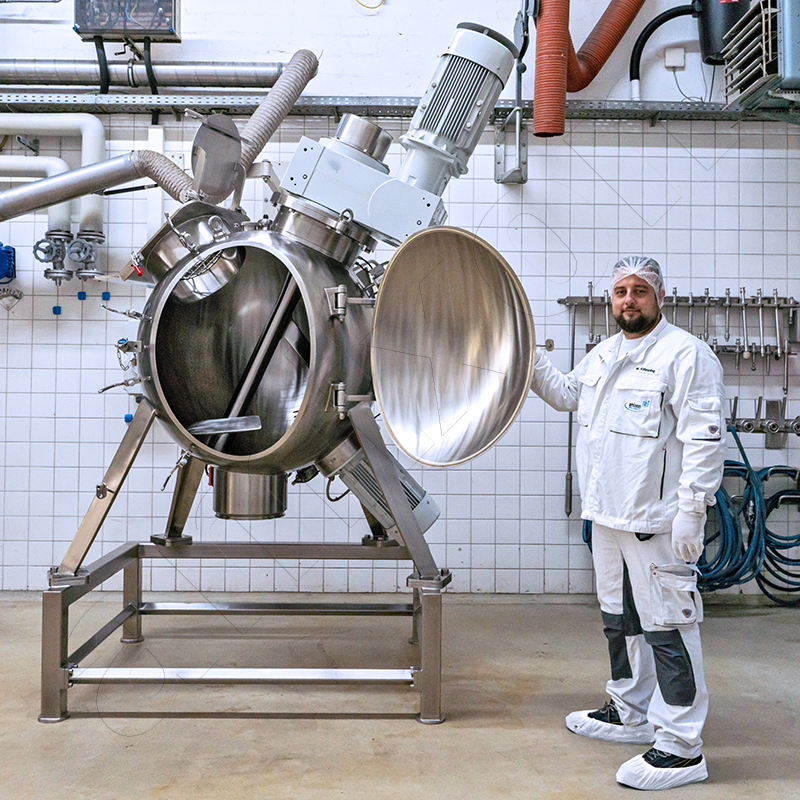
Ball mixer
Ball mixers are mixing machines that can be used to homogenise or mix dry, moist or wet powders. They can also mix liquids. They are generally used for batch mixing processes. The interior of the ball forms the so-called mixing chamber. A mixing tool rotates in this chamber and layers the material to be mixed in three dimensions. This flow process results in very high mixing efficiency when the axis of rotation of the mixing tool is neither horizontal nor vertical. The best mixing effect is achieved with an inclined arrangement. Ball mixers can also be used as synthesis reactors or vacuum mixing dryers. In this case, the ball is double-walled. A heat transfer medium flows through the double jacket. This allows for material and heat exchange.
Ball mixers are equipped with at least one rotating mixing tool. This guarantees that the entire batch is thoroughly mixed. Additional mixing tools can be provided as an option. These are usually fast-rotating chopper or knife cutting tools. These have a smaller effective diameter and cause deagglomeration during the mixing process. They generate friction and impact effects. This breaks up lumps and agglomerates.
They are also very effective when powders need to be moistened or coated, or when this is necessary for all particles. Their power input is approximately 3.5 times the square of the rotational speed.
Ball mixer manufacturers have established various designs on the market. Some manufacturers mount the mixing shaft at an angle above the ball, others at an angle below it. Others mount the mixing shaft at an angle below the ball. Still others mount the mixing shaft at an angle above and the additional deagglomeration tool at an angle below. Some manufacturers mount both the main mixing tool and the deagglomeration tool above the ball.
Main mixing tools in ball mixers
Manufacturers of sphere mixers have established different tool geometries. Some have designed the main mixing tool as a spatially curved anchor. Others use helical spirals. Still others use shovel-like tools. It is crucial that the mixing tools rotating in the ball always have the same distance from the ball wall, regardless of their position. This distance must also be maintained when mixing heavy or adhesive materials. In this respect, the mixing tools must be particularly dimensionally stable.
Filling with material
The components to be mixed are fed into the mixing chamber from above. This requires at least one filling nozzle. Some ball mixers also have several filling openings. The shut-off valve can be designed as a rotary flap, flat slide or ball segment slide. Unlike the discharge valve, the filling valve does not have to be dead space-free. There is also a vent connection on the top of the ball.
Discharge of the mixture
There is a shut-off valve at the bottom of the spherical mixing chamber. When closed, this should have the shape of a ball cut-out. Only this design is free of dead space. This means that every volume fraction in the ball is mixed thoroughly – even directly above the shut-off valve.
Cleaning and inspection of the mixing chamber
Some ball mixers have two hemispheres that can be opened for inspection. Other manufacturers install round or oval inspection doors in the mixing chamber. These must also be free of dead space. The OmgaSeal® design has proven particularly effective. Rotating tank washing nozzles are installed in the mixing chamber for wet cleaning. There are also designs in which the wet cleaning devices remain permanently in the mixer.
Question: What are the advantages of the ball as a mixing vessel?
The volume of a ball with radius r can be calculated using the following formula:
V = 4/3 ⋅ r³ ⋅ π
The surface area of a sphere with radius r can be calculated using the following formula:
O = 4 ⋅ r² ⋅ π
When comparing different rotationally symmetrical bodies, the sphere has the smallest specific surface area. This suggests that a spherical mixing chamber is easier to clean than a cylindrical or conical mixing chamber. On the other hand, it can be assumed that a conical mixing chamber is better at removing powdery mixing residues than a sphere. Manufacturers strive to produce their mixed goods as free of contamination as possible. In this context, the complete emptying of a mixing plant is becoming increasingly important.
If a spherical mixer is filled with water and you want to calculate the volume of water depending on the fill level, the following formula applies approximately:
V(𝑧) = π ⋅ z2⋅ (3 ⋅ r – 𝑧) /3
V: Water volume
z: Fill level
r: Inner radius of the hollow ball
Since the presence of the mixing tool is ignored, the formula only provides an approximate value. The actual water volume is slightly lower.
Cleaning and inspection of the mixing tool
Cleaning the dynamically moving mixing tool is a particularly important aspect. This part of the ball mixer is much more complex than the mixing chamber. Special requirements therefore apply here. Its design must meet the flow requirements of a mixing blade. It must also comply with EHEDG hygiene requirements.
The mixing tool must have a simple geometry.
- The mixing tool must promote the flow of the mixed materials and prevent compaction effects.
- This must apply equally to finely dispersed powders and to flaky or agglomerated bulk materials.
- This also applies to dry, fluidisable materials and to moist, free-flowing powders.
- The mixing tool must have as small a surface area as possible.
- It must be designed so that all areas are easily and ergonomically accessible.
The optimum mixer design can be found for every mixing task. We recommend visiting amixon®, where you can try out the available test mixers (cylindrical, spherical, conical, cycloidal).
- amixon® offers you first-class options for mixing, moistening, drying and discharging your most diverse mixed goods.
- amixon® recommends not only carrying out mixing tests, but also demonstrating the cleaning of the mixer after the test.
Depending on the type of material being mixed and the industry, appropriate cleaning regimes must be used. This applies to:
- dry cleaning
- cleaning with damp cloths
- manual wet cleaning
- manual wet cleaning
- automatic wet cleaning.
Cleaning types (2) to (5) also include the important topic of residual water drying.
It is not unusual for 2 or 3 cleaning regimes to be used alternately in a mixing operation. Depending on the degree of soiling and contamination tolerance
Cooling after wet cleaning with warm water
Customers in the food industry often want automatic wet cleaning to be carried out with hot water only. They want to avoid the use of any kind of surfactant. This is possible if the temperature of the washing water is increased and the spray pressure (volume flow and pressure) is adjusted. After cleaning, the mixer must dry as quickly as possible. The warmer the cleaning water has been heated, the faster this happens.
As a rule, mixing operation should then be continued. However, this is only possible once the mixer has cooled down. Due to the spherical design, cooling takes slightly longer than with other mixer designs. The heat is dissipated from the hollow sphere by heat radiation Q˙. This can be calculated approximately using Stefan's law.
Q˙ = ε ⋅ σ ⋅ A ⋅ (Ts⁴ − Tu⁴)
Q˙: radiated heat output in watts [W]
ε: emissivity of the surface (dimensionless, between 0 and 1)
σ: Stefan-Boltzmann constant = 5.67 × 10⁻⁸ W/(m² K⁴)
A: outer surface area of the sphere in square metres [m²]
Ts: absolute temperature of the sphere surface in Kelvin [K]
Tu: absolute temperature of the environment in Kelvin [K]
Estimation of the cooling rate of a hollow sphere
Sphere diameter: 1,000 mm
Material: Stainless steel 1.4404 (austenitic, V4A), polished to a bright finish on the outside and inside
Wall thickness: 15 mm
Surface emissivity: 0.25
Initial temperature: 70 °C
Ambient temperature: 15 °C
Cooling to target temperature: 25 °C.
Two heat transfer mechanisms must be considered: heat radiation and convection with the air. Together, their total cooling capacity is approx. 2 kW. In purely mathematical terms, the cooling time is 4 to 5 hours. As the relative temperature difference becomes smaller and smaller, the cooling curve runs asymptotically. This situation can be illustrated well with the following exponential function:
T(t) = Tamb + (Tstart − Tamb) ⋅ e−kt
T: Temperature curve
t: Time
Tamb: Ambient temperature
Tstart: Initial temperature
k: Cooling coefficient, approximately 8.59 × 10⁻⁵ 1/s
The mixing tool in the hollow sphere is also heated by the washing water. It can only cool down quickly if the mixing chamber is opened. The escaping vapour can have a negative impact on the production environment if the air conditioning system does not remove the humidity quickly enough. In this respect, it may be advisable to remove the vapour with dry fresh air in a targeted manner.
Liquid addition and distribution in the ball mixer
In practice, in addition to mixing a wide variety of powders, it is also important to ensure that they are evenly wetted. So-called liquid addition lances feed into the area of action of the rapidly rotating grinding tool. This quickly produces an agglomerate-free, homogeneous end product.
amixon has published numerous blog posts on this topic. These deal with the surface tension of liquids and their rheological properties at changing temperatures and under shear stress. The porosity of the bulk materials also plays an important role. Equally important are the characteristics of the phase boundary between solids and liquids with their hydrophobic and hydrophilic properties.
Note on the term ‘ball mixer’.
The term ‘hollow ball mixer with dynamically moving mixing tools’ would actually be more accurate than ‘ball mixer’.
The term ‘ball mixer’ is also used in the sanitary sector. This refers to a modified tap fitting. A ball with multiple holes is connected to a lever and can mix and regulate the flow of cold and hot water.