Präzisionsmischer für die Pulvermetallurgie
Die Pulvermetallurgie ist ein Spezialgebiet der Werkstoffkunde. Feine Pulver aus Eisen, Stahl und Nichteisenmetallen werden zu einem Werkstück verpresst. Manche Methoden der Pulveraufbereitung und Verarbeitung ähneln der Herstellung von Hochleistungs-Ingenieurkeramik. Dort liegt eine definierte Metallpulvermatrix vor mit der sich Oxide, Boride, Karbide und Nitride der Elemente Aluminium, Zirkon, Silizium verbinden.
Der Mischprozess
Hier geht es einerseits um die homogene Verteilung der verschiedenen Pulverkomponenten. Andererseits müssen pulvrige Gleitmittel/ Presshilfsmittel (Stearinsäure, Zinkstearat) homogen im Metallpulver verteilt werden. Solche „Metallseifen“ verringern die innere Reibung des Pulverhaufwerkes und ermöglichen die gleichmäßige Druckverteilung in der Matrize während des Verpressens. Pressdrücke können tausend bar und mehr betragen. Die Partikel der Presshilfsmittel sind zumeist kleiner als die des Metallpulvers und sie sind extrem leicht. Ihre Schüttdichte beträgt oft weniger als ein Zwanzigstel der Metallpulverschüttdichte.
Die Herstellung der feindispersen Metallpulver:
Die Metallpulverpartikel müssen hinreichend klein und rein sein, beispielweise 10 bis 50 µm. Der Mahlprozess kann in Kugelmühlen, Prallmühlen oder Luftstrahlmühlen stattfinden. Zumeist aber entstehen die Metallpulver aus der Versprühung der Metallschmelze bei hohem Druck. Es gibt auch andere Verfahren um sehr feine Metallpartikel zu erzeugen: gelöste Metallsalze werden chemisch gefällt oder Elemente wie Mangan und Kupfer werden aus der Elektrolyse gewonnen. Wenn das Metallpulver nanofeine Partikel aufweisen soll, wird eine Metallschmelze unter inerten Bedingungen bis zur Verdampfung erhitzt und als Kondensat niedergeschlagen. Je nach angewandtem Verfahren müssen die gewonnenen Partikel desagglomeriert, gereinigt oder getrocknet werden.
Eine mischtechnische Herausforderung
Eine andere mischtechnische Herausforderung betrifft einen vorgelagerten Prozess, wenn Metallpulver im Glühofen bei hohen Temperaturen chemisch reduziert werden müssen. Dann muss für jede Metallpulverpartikel ausreichend viel Kohlenstoff verfügbar sein. Das wird in der Praxis erreicht, indem die Metallpulver im Mischer mit Kohlenstoff ummantelt werden. Hier kommen große Präzisionsmischer zum Einsatz. Auch hier stellt der amixon®- Mischprozess sicher, dass der feindisperse Kohlenstoff in Form von Industrieruß jede einzelne Eisenpartikel gleichmäßig ummantelt. Übrigens: „Die Schüttdichtedifferenz von Ruß und von Metallpulver unterscheidet sich um den Faktor 500“. Dieser Sachverhalt lässt vermuten, dass die Komponenten nur unzureichend mischbar sind oder zur Entmischung neigen. Beide Phänomene sind im amixon® Mischer ausgeschlossen.
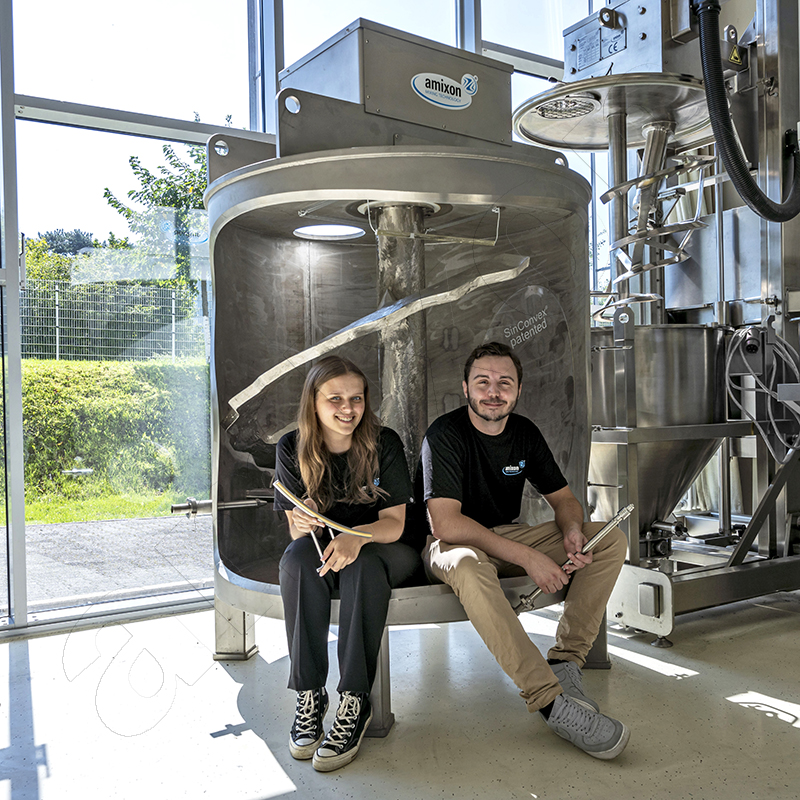
Demonstrationsobjekt für Heavy-Duty-Anwendungen.
Insofern ist der Mischprozess in der Pulvermetallurgie sehr anspruchsvoll.
amixon® verfügt über viel Branchenerfahrung und kann für die Pulvermetallurgie ideale Mischg üten sicherstellen. Egal ob die Mischcharge 30 t oder 10 kg beträgt. Wahlweise kann der Mischvorgang auch kontinuierlich stattfinden. Entscheidend ist, dass die schweren, abrasiven Metallpulver den Mischer nicht zerstören und dass der Mischprozess mit maximal gefülltem Mischer starten kann. Darüber hinaus ist es wichtig, dass der Mischer schonend arbeitet. Durch den Mischprozess dürfen die Partikelgrößen und Partikelformen nicht verändert werden.
Was kann amixon® beitragen, wenn Pulvermetallurgie zum Einsatz kommt?
Ein pulvermetallurgisch produziertes Werkstück ist nur dann brauchbar, wenn dessen Gefüge homogen und stabil ist. Die Homogenität der Metallpulver ist von zentraler Bedeutung für nahezu alle Prozessschritte.
amixon® hat weitreichende Referenzen
- in der Metallurgie,
- in der Keramikaufbereitung
- in der Kohlenstoffchemie
- in der thermischen Prozesstechnik
- in der Schüttgutmischtechnik mit abrasiven Feststoffen (unter Vakuum und Überdruck bis 20 bar)
- in der Aufbereitung von Suspensionen
- in der Chemie mit aggressiven Chemikalien
- wenn es um besonders große Misch-Chargen geht
Insofern können unsere Verfahrensingenieure viel Know-how beisteuern, wenn Sie ein Investitionsprojekt beginnen möchten.
Nutzen Sie gern das Testcenter von amixon®
Wir empfehlen Ihnen den Besuch im amixon® Testcenter in Paderborn - wenn möglich mit Ihren original Mischgütern. Das amixon® Team freut sich auf Ihren Besuch. Sie erleben Pulvermischtechnologie auf höchstem Niveau und sammeln viel Detailwissen. Darüber hinaus zeigen wir Ihnen gerne unsere moderne Fertigung.
Anwendung für Hochleistungswerkstoffe:
Die Pulvermetallurgie und das „mechanische Legieren“ findet Anwendung, wenn die hergestellten Werkstoffe einzigartige Eigenschaften aufweisen:
- sie widerstehen dauerhaft hohen Temperaturen bis zu 800 °C (Turbinenschaufel, Feuerfestauskleidungen)
- sie sind von extremer Härte (Wolframcarbid für die spanende Fertigung)
- sie sind extrem abrasionsbeständig (Bremsscheiben)
- sie sind elektrisch leitend, isolierend oder wirken als Halbleiter
- sie verändern ihre Größe in Millisekunden, wenn Sie mit elektrischer Ladung verbunden werden (Piezoelektronik)
- sie sind schwammartig porös und dienen als chemische Katalysatoren
- sie sind mit definierter Porosität gefertigt und dienen als Gleitlager für hochtourig drehende Bauteile
- sie sind besonders gut magnetisierbar. Metallische Pulver dienen der Herstellung von Hart- und Weichmagneten. (Induktionsspulen in der Nachrichtentechnik)
- …
Weil die Schmelztemperaturen und die Dichten der Legierungsbestandteile stark differieren, sind viele Hochleistungswerkstoffe schmelzmetallurgisch nicht herstellbar. Darüber hinaus können sich viele Metallkomponenten chemisch nicht verbinden. Das macht pulvermetallurgisch hergestellte Werkstoffe interessant – trotz hoher Kosten.
Manch teure Komponente muss in Pulverform bereitgestellt werden.
Unter anderem sind es die Elemente Chrom, Eisen, Kobalt, Kupfer, Magnesium, Mangan, Molybdän, Nickel, Niob, seltene Erden, Tantal, Titan, Vanadium, Wolfram, Zink und deren Derivate, die in möglichst reiner Form verfügbar gemacht werden müssen. Die Qualität eines pulvermetallurgisch hergestellten Werkstücks steht und fällt mit der Reinheit der Einsatzstoffe und deren homogener Verteilung. Minimal kleine Partikel in hoher Reinheit herzustellen ist extrem herausfordernd.
Anwendungen im Maschinenbau
Die eisenbasierte Pulvermetallurgie wird vornehmlich für kleinere Werkstücke (bis zu 4 kg) angewandt, die mit hoher Geschwindigkeit und hoher Stückzahl produziert werden. Sinterformteile entstehen, indem Metallpulver in Matrizen vergossen und verpresst werden. Der anschließende Sinterungsprozess lässt pulvermetallurgisch produzierte Bauteile definiert schrumpfen. Die fertiggestellten Bauteile zeichnen sich durch hohe Maßhaltigkeit aus. Sie verfügen über ähnliche Festigkeiten wie ein Stahlguss. Ihre Dichte beträgt aber nur 93% bis 95% der Dichte eines gegossenen Bauteils. Typische Maschinenelemente sind feinmechanische Bauteile wie beispielsweise Zahnräder mit Schrägverzahnung, Schaltwippen, Ventilschäfte oder Nutbuchsen für die Automobilindustrie. Bei Bauteilen mit komplizierten geometrischen Formen kann das Spritzgussverfahren angewandt werden. Das Metallpulver wird zuvor mit einem thermoplastischen Binder vermischt und dann in einer Knetmaschine plastifiziert.
Das pulvermetallurgische Produktionsverfahren ist Massenprodukten mit kleinen Abmessungen vorbehalten, denn das Verfahren ist teuer. Die hohen Kosten werden durch mehrere Faktoren bedingt:
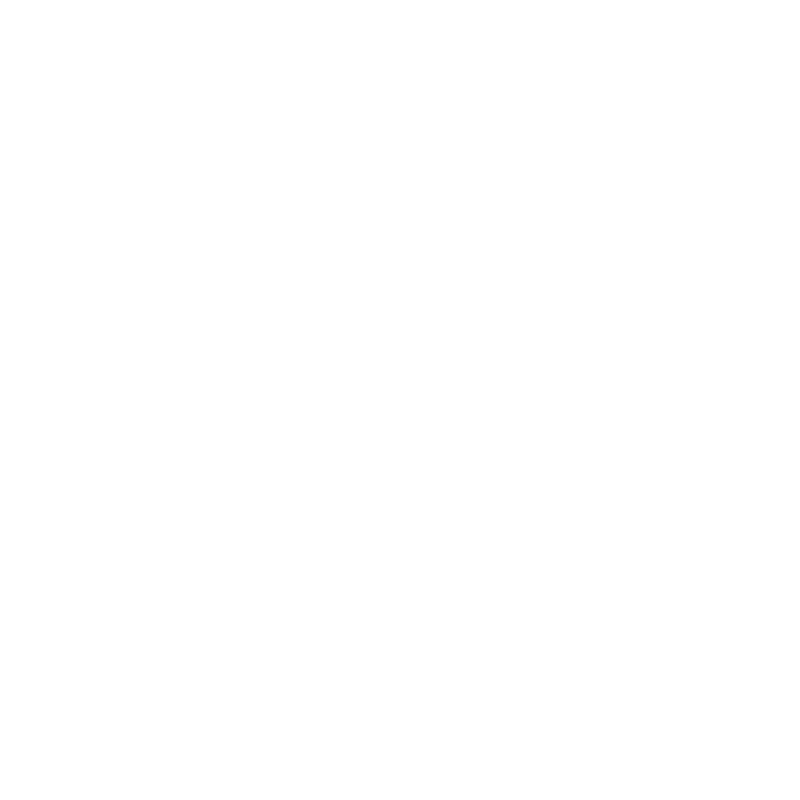
Die Anfertigung der verschleißbeständigen Bauteilmatrize
Die Bauteilmatrize muss um das Schwundmaß vergrößert angefertigt werden. Oftmals ist die Frage der ausreichend hohen Dauerfestigkeit der Presswerkzeuge gleichbedeutend mit der Frage nach der Verschleißbeständigkeit. Die Entnahme/ der Ausstoß der erzeugten Grünlinge muss ohne Beschädigung erfolgen. Das muss in einer Serienproduktion schnell und effizient stattfinden.
In vielen Fällen findet die Heißsinterung unter Inertbedingungen statt, manchmal sogar unter Gasausschluss im Vakuum. Die Verdichtung der Metallpulver kann unter Verschluss isostatisch stattfinden, wenn die Verpressung im Wasserbad stattfindet. Oft werden die so erzeugten Halbzeuge in einer Sinterschmiede nachverdichtet.
Formgebung und Entbinderung durch chemische Zersetzung
Hochleistungspressen müssen sehr hohe Drücke aufbringen um die Grünlinge zu erzeugen. Nach dem Pressen wird der Binder aus den Grünlingen thermisch ausgetrieben, indem er eine optimierte Temperaturkurve absolviert.
Die hohe Temperatur der Heißsinterung
Die Wärmebehandlung erstreckt sich über mehrere Stunden. So diffundieren die Atome der artgleichen und artfremden Metallpartikel. Das ist nur dann möglich, wenn die Partikel eng miteinander verreiben und verdichten. Die Gefügeausbildung findet statt, obwohl die beteiligten Elemente schmelzmetallurgisch nicht miteinander vereinbar sind. Hierin liegen die Besonderheiten des Werkstoffs begründet.
Mechanische Nacharbeit
Die mechanische Nacharbeit sollte normalerweise auf ein Minimum begrenzt sein.
© Copyright by amixon GmbH