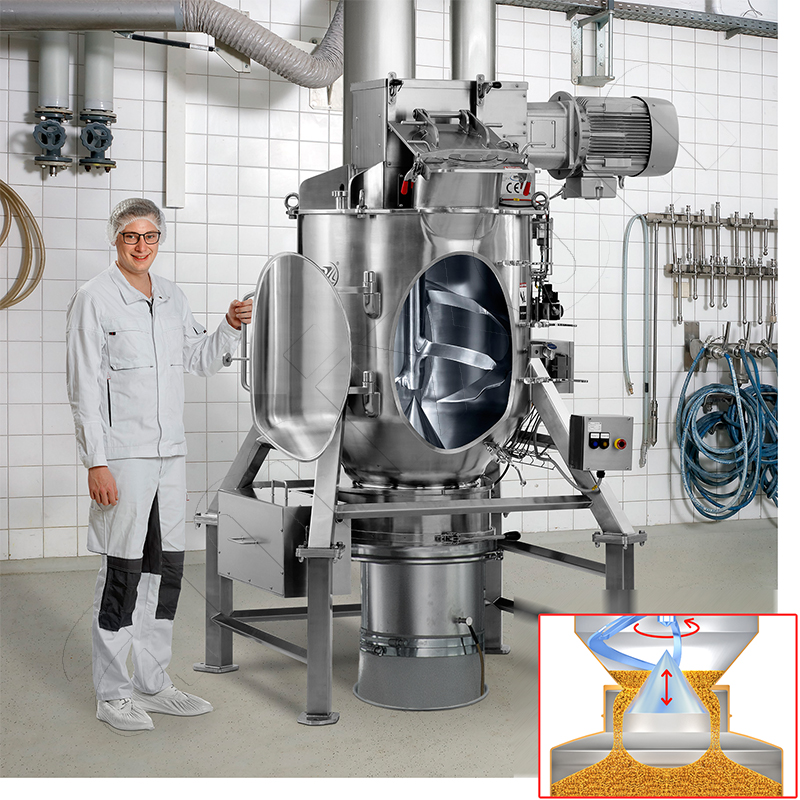
amixon® KoneSlid® mixers achieve ideal mixing qualities with minimal energy input. The mixing time is extremely short. The particle structure of the raw material is preserved.
Industrial mixer for baby food: Hygienic, quality-conscious, responsible - part 2
amixon® offers three mixing technologies for baby, infant and premature baby nutrition:
- large-batch mixing,
- quasi-continuous batch mixing,
- continuous mixing.
amixon® manufactures hygienic powder mixers/blenders. amixon® mixers refine spray-dried nutrients into valuable baby food: vitamins, minerals, prebiotics, probiotics, omega-3 and omega-6 fatty acids, emulsifiers and stabilisers are optimally and precisely distributed in the nutrient. The mixing process is so gentle that the instant properties can be improved.
Inline or with buffer? The right strategy for mixing and packaging. amixon® offers both solutions
When manufacturing baby food, choosing the right mixing process plays a crucial role. In the blog post Part 1, we described the amixon® twin-shaft mixer, which can homogenise batches of up to 12 m³ with ideal accuracy, precision and care. An amixon® twin-shaft mixer like this is shown on the right. It can be used flexibly, can be completely emptied, is easy to clean and enables convenient quality control. Only one analysis has to be carried out per batch. A retention sample is sufficient.
In this blog post, we report on two further mixing processes from amixon®: quasi-continuous powder mixing and continuous powder mixing. Both can be used as ‘end-of-line mixing systems’.
For reasons of process efficiency, it makes sense to produce similar product groups in campaigns. This minimises set-up times and increases productivity. Typical product groups are listed below:
- kosher
- halal
- allergen
- non-allergenic
- with milk protein
- without milk protein
- flavoured
- neutral (without added flavouring)
- dietary
- ....
- ...
In end-of-line mixing systems, the mixture is transferred to the packaging machine immediately after the mixing process. All processing units are arranged in a vertical line. Some baby food manufacturers have installed several identical mixing lines. These are used exclusively for certain product groups. This means that the set-up times can be reduced to almost zero. The amixon® KoneSlid® mixer is particularly suitable for this type of end-of-line production.
KoneSlid® powder mixer - Efficient powder processing in a quasi-continuous process
Two KoneSlid® mixers and a surge bin are installed directly above the packaging machine. The two KoneSlid® mixers are mounted on load cells. The product stream is continuously fed from the spray tower into the fluid bed agglomerator. Cooling and sieving are also continuous – the material flow remains continuous up to this point.
The spray-dried product flows into the KoneSlid® mixer (I). At the same time, vitamins, trace elements, probiotics and flavours are added to this mixer in batches. The mixing process begins immediately afterwards and ends with the emptying of the KoneSlid® mixer (I). Simultaneously with the start of one mixer (I), spray-dried product flows into the KoneSlid® mixer (II).
The two KoneSlid® mixers work in batches at a high cycle frequency. The entire mixing process, including emptying, takes only 120 to 180 seconds. Filling is relatively slow, depending on the capacity of the spray tower. The low speed of the mixing spirals ensures that the particle structure of the raw materials is preserved. Typical batch sizes are 300 to 1200 kg.
The plant is gas- and dust-tight, so that both the mixture and the operating personnel are reliably protected. Dust-free processing ensures maximum hygiene and a clean production environment.
The KoneSlid® powder mixer achieves the highest mixing quality with minimal energy input. Experience shows that even after spray-drying, fluidised bed granulation or vacuum freeze-drying, sensitive agglomerates remain virtually free of fines.
The instant food products manufactured in the KoneSlid® Blender are typically
- dust-free
- quickly dispersible
- reliable wettability and
- easily soluble
- in the liquid quickly sinking
The mixture is transported directly to the packaging machine.
Legend for picture on the left: c) Batch dosing feeder for vitamins, trace elements, probiotics d) Fluidised bed agglomerator e) Diverter valve f) Two KoneSlid® mixers (mirrored) with g) extra large inspection doors to the mixing chamber and to the discharge fitting h) Feeding i) Filling and packaging machine
Avoiding oxidation by inerting in the KoneSlid® mixer
The mixtures can be inerted in the KoneSlid® mixer. If required, amixon® can make the mixer vacuum- and pressure-tight. By applying a vacuum, the ambient air is removed from the mixing chamber and the powder, so that only the mixture remains in the container. This process can be carried out both during and after the mixing process.
Then the mixing chamber is flooded with inert gases such as nitrogen, carbon dioxide or a mixture of both gases up to atmospheric pressure. This renders the mixture inert. The minimum durability of the instant food is improved.
This inerting process is also suitable for highly flammable or dust explosive mixtures. Maximum operating safety: amixon® mixers are certified and meet the requirements of the type examination for dust explosion-prone goods according to Ex II 1D (Zone 20). In the Atex classification, Zone 20 refers to an area in which an explosive atmosphere is present for more than 50% of the operating time – for example, in the mixing chamber itself.
The KoneSlid® mixing principle works independently of the filling level. This can vary from approx. 10% to 100%. The KoneSlid® mixer empties in a few seconds. Free-flowing products usually flow out completely. This takes only a few seconds.
Continuous precision mixing – Perfect homogeneity from the first to the last gram
Continuous mixing is a particularly efficient process for manufacturing baby food in powder form. The amixon® continuous mixer AMK was specially developed for the production of product groups that are produced in large quantities – including many intermediate products.
The AMK conical mixer stands for particularly efficient continuous mixing. This amixon® flow mixer was specially developed for the production of large quantities of bulk materials over long periods of time. It can be operated both as a batch mixer and as a continuous mixer and always ensures uniform and gentle homogenisation – even with sensitive powder mixtures.
A well-known problem of conventional continuous mixers is the start-up of the mixing plant from a standstill: the initial mixture produced deviates from the recipe. The amixon® continuous mixer AMK sets new standards here: it combines the precision of a batch mixer with the efficiency of a continuous process.
During the start-up phase, the mixer remains closed until the dosing systems have fully synchronised. Dosing fluctuations are automatically corrected. The mixing tool then begins to rotate. The discharge valve only opens when the ideal mixing quality has been achieved. The discharge valve is controlled by the signal from the load cells. The discharge valve has no dead space and keeps the filling level in the mixer constant.
The result: from the first to the last kilogram, the mixture remains perfectly homogeneous – for consistently high product quality throughout the entire production campaign.
7 steps for starting from a standstill
- At the start of production, all gravimetric feeders are started simultaneously at a low mass flow rate.
- The discharge valve of the mixer is initially closed.
- The dosing elements ‘harmonise and correct’ their dosing behaviour.
- This increases the filling level in the amixon® AMK mixer.
- When the mixing container is about 50 percent full, the mixer drive starts.
- As soon as the filling level has reached approximately 80 per cent, the discharge device opens slowly.
- A constant mass flow leaves the mixer. Every gram is optimally mixed.
Thanks to the innovative amixon® SinConvex® mixing tool, a high degree of complete emptying is possible at the end of the campaign. Every gram of the mixture thus becomes saleable.
Fully automatic: wet cleaning, drying, closing the cleaning opening
If it is necessary to carry out wet cleaning: With the WaterDragon® wet cleaning system, all parts that come into contact with the product are cleaned without leaving any residue. Then it is dried.
It is often sufficient to clean either dry or moist. Here, too, amixon offers unique hygienic properties.
Our innovative inspection doors with OmgaSeal® allow convenient access. The O-ring seal in the groove provides a seal very close to the product and is dust-, gas- and watertight.
Our KwickKlamp® door closure makes operating the mixer's inspection doors quick and easy. Even with frequent use, the doors always close completely, gas-tight and dead-space-free. Electromechanical safety interlocks ensure the highest level of occupational safety.
amixon® offers you test centres at home and abroad
We warmly invite you to use them. Contact us and come to us with your mixtures. We are sure that you will achieve excellent results and a great deal of knowledge. This is how you get a great head start on information.
Our test centres are located in Germany, the United States, India, China, Japan, Korea and Thailand.
© Copyright by amixon GmbH