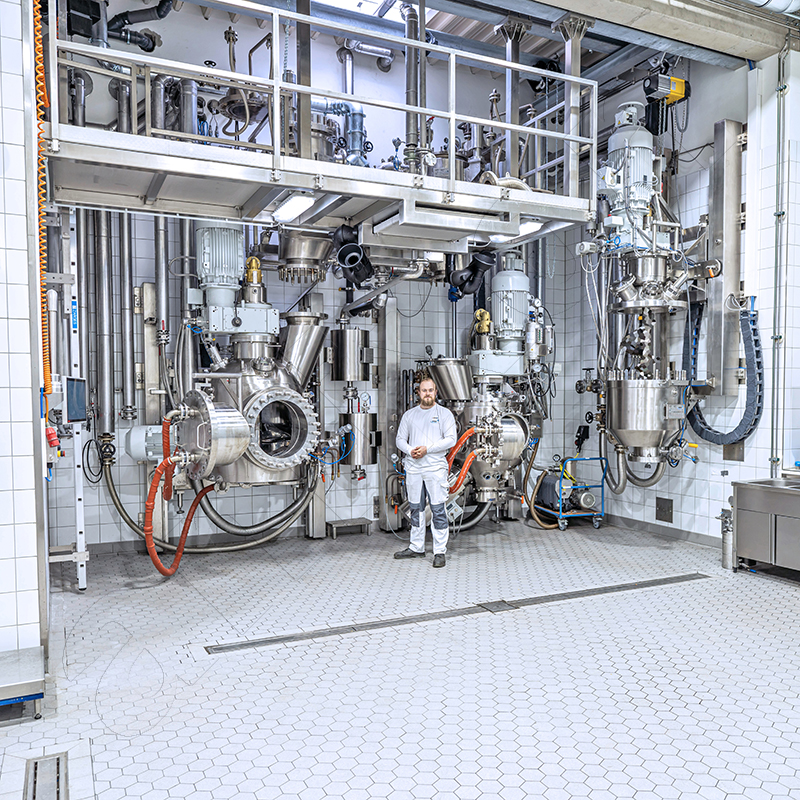
Kompleksowa technologia instalacji do przetwarzania metylocelulozy, karboksymetylocelulozy, hydroksyetylocelulozy itp.
Masa celulozowa to włóknista masa otrzymywana w wyniku chemicznego roztwarzania włókien roślinnych. Pulpa składa się z celulozy. Słowo to pochodzi z łaciny i oznacza małą komórkę. Celuloza jest podstawową statyczną strukturą wszystkich komórek roślinnych.
Pochodne celulozy: W chemicznie zmodyfikowanej formie - na przykład jako metyloceluloza - umożliwiła przede wszystkim rozwój fotografii. Jest ważnym składnikiem włókien tekstylnych. Pomaga w układaniu płytek, utrzymuje świeżość wypieków, nadaje konsystencję majonezowi i sprawia, że pasta do zębów jest gładka.
Najważniejszym eterem celulozy pod względem objętości jest karboilometyloceluloza (CMC)
Oczyszczona pulpa drzewna lub bawełniana jest mielona na drobny proszek (wielkość cząstek ok. 100-200 μm) i pneumatycznie przenoszona do mieszalnika o dużej pojemności i objętości od 10 do 30 m³.
Stamtąd homogenizowana pulpa jest transportowana do reaktora syntezy. Pięćdziesiąt procent sody kaustycznej jest rozpylane do reaktora. W wyniku reakcji egzotermicznej powstaje celuloza sodowa. Następnie do reaktora rozpylany jest kwas chlorooctowy. Powstaje karboksymetyloceluloza. Alternatywnie, syntezę CMC można przeprowadzić w postaci zawiesiny z rozpuszczalnikiem lub bez (izopronanol lub etanol).
Inne pochodne celulozy (np. hydroksypropylometyloceluloza) są wytwarzane w podobny sposób. Jednak w tym przypadku zazwyczaj nie stosuje się rozpuszczalników, a chemikalia reakcyjne są gazowe (chlorek metylu, tlenek propylenu lub tlenek etylenu). Konwersja materiału wymaga stosunkowo wysokiego ciśnienia w układzie (do 20 barów), aby gazowe reagenty pozostały w układzie w wysokich temperaturach.
Reaktory do produkcji pochodnych celulozy są zaprojektowane tak, aby były odporne na ciśnienie. Są one również wyposażone w podwójny płaszcz, dzięki czemu zawartość może być podgrzewana lub chłodzona. Większe reaktory posiadają również wydajne skraplacze.
amixon® oferuje trzy metody homogenizacji dużych objętości: (1), (2) i (3):
(1) Mieszalnik stożkowy amixon® miesza w sposób nieciągły
W mieszalniku stożkowym amixon® spotykają się dwa przeciwstawne przepływy. Na zewnątrz mieszanka jest transportowana spiralnie w górę, podczas gdy w środku dominuje przepływ w dół. W obszarach granicznych następuje zmiana położenia w układzie cząstek. Ramiona mieszalnika w kształcie łopaty generują uzupełniające się przepływy krzyżowe. Pomimo niskiej częstotliwości obrotów, gwarantowana jest idealna jakość mieszania, której nie można już poprawić w praktyce. Całkowity przepływ opisany powyżej powoduje, że wszystkie cząstki stale poruszają się względem siebie. Występuje on powszechnie, niezależnie od tego, czy poziom napełnienia wynosi 5%, czy jest maksymalny. Specjalny kształt spirali mieszającej w konstrukcji „SinConcave®” lub „SinConvex®” gwarantuje prawie 100% odprowadzanie resztek. Szczególnie delikatne traktowanie mieszanki jest bezpośrednim wynikiem niskiej mocy napędu. Cząstki mieszanki nie są kruszone, zaokrąglane ani łamane.
(2) mieszalnik stożkowy amixon® miesza w sposób ciągły
Interesującą cechą tego typu mieszalnika jest to, że może on pracować zarówno w trybie nieciągłym, jak i ciągłym, niezależnie od jego wielkości. Jeszcze bardziej interesujące jest jednak to, że wyrzucana mieszanka odpowiada idealnej jakości mieszania od samego początku. Nie występują żadne „straty rozruchowe”. Zostało to wyjaśnione poniżej:
Tryb pracy na początku produkcji:
Wylot mieszalnika jest zamknięty. Wszystkie dozowniki grawimetryczne są uruchamiane jednocześnie z niskim przepływem masowym. Główny układ sterowania dozowaniem harmonizuje wszystkie przepływy produktu. Poziom napełnienia mieszalnika wzrasta w sposób ciągły, a napęd mieszalnika rozpoczyna się od połowy poziomu napełnienia. Proces wyrównywania jest zakończony, gdy mieszalnik jest napełniony w nieco ponad połowie. Po osiągnięciu żądanego poziomu napełnienia (ok. 60-80% zawartości użytkowej) element wylotowy otwiera się powoli. Ten poziom napełnienia jest utrzymywany na stałym poziomie. Przepływ dozowania można zwiększyć do maksymalnego przepływu masowego pod stałą kontrolą.
Tryb pracy po zakończeniu produkcji:
Wszystkie elementy dozujące opóźniają przepływ masy jeden po drugim, a następnie wyłączają się i zamykają jednocześnie. Mieszalnik opróżnia się w sposób ciągły, dopóki nie pozostaną ostatnie resztki. Swobodnie przepływające produkty wypływają w całości.
Zalety dla użytkownika w skrócie:
- Technicznie idealna jakość mieszania
- Możliwość pracy jako mieszalnik wsadowy do premiksów lub jako mieszalnik ciągły
- Regulowana intensywność mieszania (od delikatnej homogenizacji do intensywnej deaglomeracji)
- Zdefiniowany, średni czas przebywania mieszanki w mieszalniku w oparciu o ciągły przepływ bojlera. Jest to niezależne od prędkości narzędzia mieszającego.
- Brak strat produktu na początku produkcji
- Brak strat produktu na końcu produkcji
- Idealne opróżnianie pozostałości
- Zdefiniowany poziom napełnienia od 10% do 100% zawartości użytkowej
- Mikrodrobne mieszanie cieczy bez zanieczyszczenia mieszalnika
- Rozszerzone procesy, takie jak nawilżanie, odpuszczanie, suszenie,
- najwyższy standard higieny (standard GMP); łatwe czyszczenie, na sucho lub na mokro - mieszalnik jest podparty i napędzany tylko od góry.
(3) Mieszalnik Gyraton® miesza w sposób ciągły lub nieciągły.
Do homogenizacji szczególnie dużych partii o objętości do 100 m³, amixon® stworzył interesującą nowość w postaci mieszalnika Gyraton®: Spirala mieszająca obraca się zgodnie z ruchem wskazówek zegara i przenosi mieszankę do góry. Dodatkowy napęd porusza dolną częścią wału mieszalnika po okręgu. Punkt obrotu znajduje się na górze, w środku uszczelnienia wału. Mieszalnik ten może być również stosowany do suchych, wilgotnych lub zawieszonych materiałów sypkich. Rozmiary można dowolnie wybierać w zakresie od 10 m³ do 100 m³. Rozmiary do 70 m³ mogą być transportowane w pełni zmontowane na drodze.
Najlepsze wyniki mieszania uzyskuje się przy poziomie napełnienia wynoszącym zaledwie 10%. Mieszanie jest niezwykle delikatne przy bardzo niskim nakładzie energii. Mieszalnik jest zasilany od góry przez jedną lub więcej standardowych wylewek. Mieszanka jest odprowadzana w dół przez standardową wylewkę, gdy dolna klapa jest otwarta.
Mieszalnik Gyraton® charakteryzuje się następującymi cechami
- Proces mieszania odbywa się bez martwej przestrzeni, szczególnie delikatnie i przy minimalnym nakładzie energii.
- Bardzo dobre opróżnianie pozostałości
- Opcjonalna odporność na ciśnienie lub próżnię
- komora mieszania może być opcjonalnie sterowana temperaturą
- Oszczędność miejsca, kompaktowa konstrukcja. Duży mieszalnik może być transportowany na drodze
- Komora mieszania jest łatwo dostępna przez duże drzwi inspekcyjne
- Proste czyszczenie
- na mokro (automatycznie)
- na sucho ręcznie za pomocą odkurzacza
- W zależności od długości czasu mieszania, który może być określony przez klienta, częstotliwość obrotów narzędzia mieszającego i nałożony ruch wahadłowy są regulowane. Silniki są bardzo małe. Zużycie energii jest odpowiednio niskie.
- System mieszania może być również stosowany do wilgotnych, słabo płynących produktów.
Próby w centrum technicznym amixon®
Jeśli masz zamiar podjąć decyzję inwestycyjną w zakresie mieszania, homogenizacji, aglomeracji, syntezy, chłodzenia lub suszenia próżniowego mieszanek, powinieneś porozmawiać z nami. amixon® oferuje wyjątkowe i wysoce wydajne rozwiązania. Oferujemy szeroki zakres wiedzy specjalistycznej w zakresie inżynierii procesowej i dysponujemy doskonale wyposażonym działem inżynierii maszyn i urządzeń. Chętnie umówimy się z Państwem z krótkim wyprzedzeniem na testy w naszym centrum technicznym.
Ciągłe chłodzenie lodem płatkowym
Produktem reakcji jest wilgotna pochodna celulozy, która nadal zawiera sól kuchenną i niektóre produkty uboczne (wyższe alkohole). Surowy produkt jest przenoszony do łaźni wodnej o temperaturze 90°C i zawieszany. Sole i produkty uboczne rozpuszczają się w gorącej wodzie. Ale nie etery celulozy: MC, HEMC i HPMC są nierozpuszczalne w wodzie w temperaturach powyżej 50-60 °C.
Gorąca woda płucząca jest następnie oddzielana przez filtrację, a placek filtracyjny jest płukany bez soli. Gorąca woda płucząca może być używana wielokrotnie do czyszczenia, ponieważ może wchłonąć do 30% soli kuchennej. Oszczędza to energię i wodę. Wilgotność resztkowa oczyszczonego produktu po etapie filtrowania i mycia nadal wynosi około 50-60%. Gęstość nasypowa eteru celulozy po płukaniu nadal wynosi około 150 g/l. Do chłodzenia wykorzystywane są mieszalniki poziome pracujące w trybie ciągłym. Chłodzenie odbywa się zazwyczaj za pomocą płatków lodu. W temperaturze poniżej 45°C produkt nie jest już rozpuszczalny w wodzie.
Duże masy muszą być suszone wydajnie i higienicznie.
Stosowane tutaj suszarki błyskawiczne to zazwyczaj pracujące w trybie ciągłym suszarki rozdrabniające. Są one w stanie skutecznie rozbijać aglomeraty. Proces suszenia odbywa się w atmosferze. Duże ilości powietrza są wstępnie oczyszczane, suszone i podgrzewane. Proces suszenia jest bardzo ważny. Zużywa on dużo energii.
Wysuszony proszek jest następnie odpylany w cyklonie. Najdrobniejszy pył jest oddzielany w filtrach tkaninowych. Ciężkie cząstki są następnie sortowane i przesiewane. Określony rozmiar cząstek jest ważny dla końcowego zastosowania.
Masa celulozowa jest odnawialnym produktem naturalnym. Podobnie jak wszystkie produkty naturalne, masa celulozowa podlega wahaniom sezonowym i związanym z miejscem produkcji. Masa celulozowa jest również przetwarzana partiami. Również w tym przypadku występują niewielkie różnice w jakości poszczególnych partii. Jednym z głównych zadań mieszalnika końcowego o dużej objętości jest wyrównanie tych różnic. Towary są następnie pakowane w worki lub big-bagi.
Materiały o wysokiej wytrzymałości muszą być również trwale odporne na korozję. Technologia spawania ma tu ogromne znaczenie.
Istnieją również inne kryteria, które należy wziąć pod uwagę podczas projektowania reaktora. Na przykład, oprócz wysokiej wytrzymałości, materiał zbiornika musi być szczególnie odporny na korozję, ponieważ chlorki wytwarzane przez sole są agresywne chemicznie w wysokich temperaturach w połączeniu z wodą. Zjawisko pękania korozyjnego naprężeniowego opisuje spadek odporności materiałów na korozję, gdy są one narażone na zwiększone naprężenia rozciągające. Ponadto należy wziąć pod uwagę zjawisko zmęczenia materiału spowodowane zmieniającymi się obciążeniami i temperaturami.
Obsługa odczynników i produktów ubocznych reakcji również wymaga dużej wiedzy specjalistycznej. Tlenek etylenu (produkcja HEC lub mieszanych eterów HE, takich jak HEMC) ma najwyższy potencjał zagrożenia: Jest wybuchowy i musi być przechowywany w atmosferze azotu. Podczas produkcji metylocelulozy (MC, HEMC lub HPMC) w reakcji ubocznej powstaje eter dimetylowy, który jest wysoce łatwopalny, wybuchowy i toksyczny. Musi on zostać usunięty pod koniec reakcji wraz z nieprzereagowanym chlorkiem metylu. W procesie przemysłowym mieszanina gazów jest zbierana pod ciśnieniem i w najlepszym przypadku ponownie wykorzystywana w procesie.
Celuloza ma wiele talentów
Nie ma prawie żadnego innego surowca, z którym historia ludzkości byłaby tak ściśle związana jak z celulozą. Bez papieru historia ludzkości wyglądałaby zupełnie inaczej. Nawet szmaty były początkowo wykorzystywane do produkcji papieru. Dzieje się tak, ponieważ są one wykonane z bawełny. Celuloza jest obecna w jej włóknach w szczególnie czystej postaci.
Rozwój chemicznego wykorzystania celulozy rozpoczął się w 1846 roku wraz z produkcją nitrocelulozy, znanej również jako trinitrat celulozy. Początkowo była ona wykorzystywana do celów wojskowych i była również znana jako bawełna strzelnicza. Jest ona wytwarzana, gdy celuloza jest traktowana kwasem nitrującym, mieszaniną kwasu siarkowego i azotowego. W dalszych etapach procesu bawełna strzelnicza jest myta, mielona i suszona.
Historia
Równolegle do zastosowań wojskowych, cywilne wykorzystanie nitrocelulozy rozpoczęło się w XIX wieku. Słabo nitrowana nitroceluloza (dwuazotan celulozy) została zmieszana z kamforą i jako celuloid stanowiła podstawę pierwszych technicznych tworzyw sztucznych.
Celuloid był używany jako nośnik filmu fotograficznego do 1951 roku, a piłeczki do tenisa stołowego były również produkowane z celuloidu do 2014 roku. Pierwsza przezroczysta folia z tworzywa sztucznego była również oparta na celulozie. W latach dwudziestych XX wieku szkło celulozowe (nazwa handlowa: celofan) było produkowane do celów opakowaniowych. Jest ono szczególnie błyszczące i, w przeciwieństwie do nowoczesnych folii opakowaniowych, może być trwale pogniecione. Używano go na przykład do pakowania słodyczy, ponieważ można go było łatwo „skręcić” na obu końcach. W międzyczasie celofan został w dużej mierze zastąpiony plastikowymi foliami na bazie oleju ze względów cenowych i technicznych. Jednak renesans celofanu w przyszłości może wynikać z jego doskonałej biodegradowalności.
Istnieje ważny powód, dla którego celuloid został zastąpiony przez inne tworzywa sztuczne. Jest nim łatwopalność celuloidu.
Celuloza jest biodegradowalna
Zawartość celulozy w bawełnie wynosi około 84-91%. Ze względu na długie włókna, jest ona wykorzystywana głównie jako surowiec tekstylny. Z drugiej strony, zawartość celulozy w drewnie wynosi tylko około 40-45% i musi zostać wyizolowana w złożonym procesie chemicznego roztwarzania. Pozostałości z tartaków i niskiej jakości drewno iglaste są w szczególności wykorzystywane jako surowiec do przemysłowego wykorzystania do produkcji papieru. Jednak wyższej jakości drewno iglaste i liściaste, głównie z plantacji, jest również wykorzystywane jako masa celulozowa.
Szczególnie czysta celuloza jest uzyskiwana z drewna w procesie roztwarzania siarczynowego. Celuloza chemiczna otrzymywana w ten sposób jest również znana jako masa celulozowa rozpuszczalna lub masa celulozowa specjalna.
Celuloza musi jednak najpierw zostać wyekstrahowana z drewna. Kłody są rozdrabniane na zrębki. Celem jest osiągnięcie jednolitego rozmiaru.
Zrębki te są gotowane w reaktorach ciśnieniowych z kwaśnymi chemikaliami w wysokiej temperaturze i pod ciśnieniem przez kilka godzin. Celulozowe produkty uboczne, takie jak lignina i hemicelulozy, rozpuszczają się w kwasie i są oddzielane wraz z filtratem. Filtrat nazywany jest czarnym ługiem i zawiera pozostałości ligniny, węglowodany z rozkładu hemiceluloz, węglan sodu, siarczan sodu i inne sole nieorganiczne. Sód, siarka i wapń są w dużej mierze odzyskiwane z czarnego ługu i poddawane recyklingowi. Wanilina może być ekstrahowana z ligniny, podobnie jak w przypadku kory drzewnej.
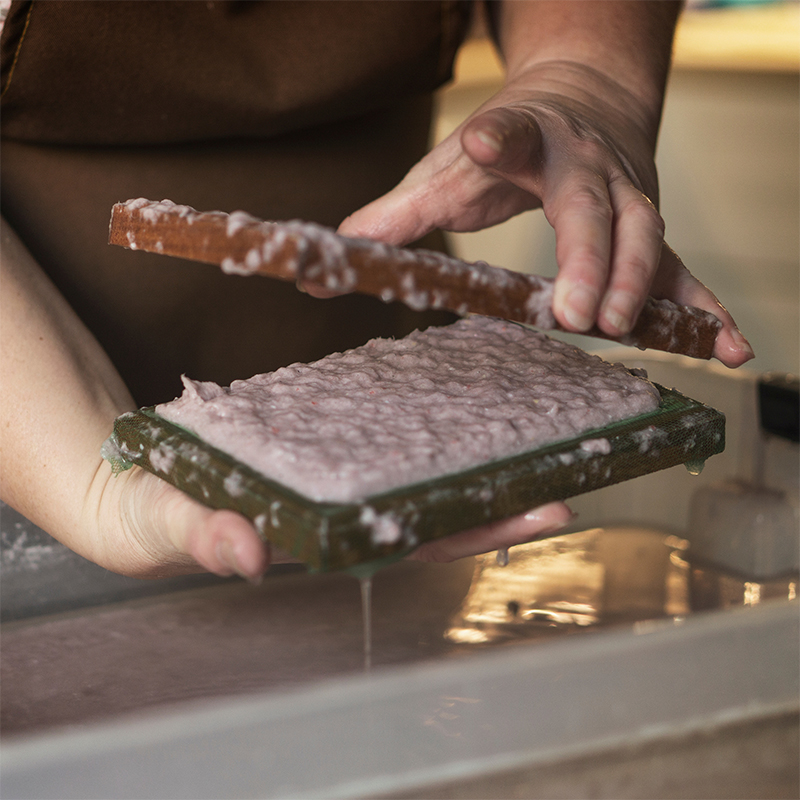
Osad celulozowy jest odwadniany ręcznie.
Pochodne celulozy: globalna produkcja w 2020 r.
Product | World production in 2019 | Application |
Cellulose regenerated | 3.300.000 t/a | Textiles |
Cellulose acetate | 900,000 t/a | Coatings and membranes |
Cellulose nitrate | 420.000 t/a | Coatings, membranes and explosives |
Carboxymethyl-cellulose | 360.000 t/a | Food, Cosmetics, Pharma, Oilfield, Paper |
Methylcelluloses | 180,000 t/a | Food, pharma and construction |
Hydroxylethyl-cellulose | 8,000 t/a | Paints, lacquers, films and cosmetics |
Etery celulozy i ich zastosowania w przemyśle
Name | Abbreviation | Production | Application |
Carboxymethyl cellulose | CMC | Converted to alkali cellulose with sodium hydroxide solution. Alkylation with chloroacetic acid. | Petroleum industry, textile industry, detergent additive, binder, thickener, paper sizing agent (wallpaper paste), protective colloid, food additive E 466 (ice cream, mayo, jelly, baked goods), toothpaste, cross-linked as tablet disintegrant. |
Methylcelluloses | MC | Converted to alkali cellulose with sodium hydroxide solution. Alkylation with methyl chloride, | Additives in various building materials (concrete, mortar, tile adhesives, fillers, plasters, etc.) Wallpaper paste, thickener, gelling and coating agent, emulsifier, stabiliser in food (MC: E 461, HPMC: E 464) meat substitutes, ice cream, bakery products, mayo, instant products and frozen products) and cosmetics. In pharmacy as "artificial tears", laxative, negative contrast agent, retardation of active ingredients, tablet coating, material for hard capsules. |
Ethyl cellulose | EC | Converted to alkali cellulose with sodium hydroxide solution. Alkylation with ethyl chloride. | Thickener, binder, adhesive, as well as film former and water-repellent barrier layer. Main ingredient lightfast cellulose ether coatings, packaging materials, thermoplastics, artificial snow for Christmas trees, cable insulation, protective skins and seals. As an additive of synthetic resins and waxes for varnishing coloured Easter eggs and as an additive for stamping inks in the food industry (E 462). In pharmacy, excipient for increasing viscosity, as a binder for tablet granules, as a builder and disintegrant for tablets, and in particular also as a film former (e.g. trademarked under Surelease®) for lacquer tablets. |
Hydroxyethylcellulose | HEC | Converted to alkali cellulose with sodium hydroxide solution. Etherification with ethylene oxide. | In the building materials industry in water-soluble paints and dispersion adhesives as well as plasters and fillers. In pharmaceuticals as an excipient and in toothpaste. |
Hydroxypropylcellulose | HPC | Converted to alkali cellulose with sodium hydroxide solution. Etherification with propylene oxide. | Application as pharmaceutical excipient, binder for ceramic masses, for coatings and adhesives, in cosmetic articles, in printing inks and in polymerisation technology. In food as a stabiliser, protective layer and gloss coating. |
Pochodne celulozy spotykamy niemal wszędzie
Postępy w chemii makromolekularnej doprowadziły do opracowania wielu pochodnych celulozy o cennych właściwościach.
Estry celulozy: W 1856 roku wyprodukowano pierwszy termoplast z kamfory i azotanu celulozy. Był on wykorzystywany do produkcji piłek do tenisa stołowego i materiałów filmowych do fotografii i ruchomych obrazów.
Octan celulozy: Następnie powstał drugi termoplast, który mógł być przetwarzany na piankę (filtry papierosowe) i włókna. Dalszy rozwój doprowadził do powstania przezroczystych formowanych korpusów, kostek i uchwytów narzędzi.
Etery celulozy: Od wczesnych lat trzydziestych XX wieku ta grupa pochodnych celulozy zyskała znaczenie przemysłowe, triumf, który trwa do dziś i ma coraz szerszy zakres zastosowań. Etery celulozy są nietoksycznymi, w większości rozpuszczalnymi w wodzie produktami, które są zwykle sprzedawane w postaci białych proszków lub granulek. Specyficzne właściwości poszczególnych eterów celulozy zależą od rodzaju, liczby i rozmieszczenia podstawników, które są wprowadzane w wyniku reakcji chemicznej po aktywacji cząsteczki celulozy sodą kaustyczną.
Obszary zastosowania
Nazwy są podawane poprzez określenie podstawnika, np: metyloceluloza (MC), hydroksypropylometyloceluloza (HPMC), karboksymetyloceluloza (CMC), hydroksypropyloceluloza (HPC), etyloceluloza (EC) itp. Są one stosowane w przemyśle budowlanym jako dodatki optymalizujące różne właściwości zapraw, klejów do płytek lub wypełniaczy (HEMC lub HPMC). Pasta do tapet składa się głównie z metylocelulozy (MC) lub karboksymetylocelulozy (CMC).
Pochodne celulozy są stosowane jako smary w obróbce metali oraz jako regulatory lepkości i spoiwa w produkcji farb i lakierów. W zmywarkach do naczyń jako materiał wybuchowy lub w rolnictwie do opóźniania działania pestycydów.
Niektóre pochodne celulozy są dopuszczone jako dodatki do żywności i do stosowania w preparatach kosmetycznych. Wykorzystywane jest między innymi zachowanie różnych eterów celulozy w środowisku wodnym w różnych temperaturach. Są one często niezbędnymi dodatkami w emulgatorach, stabilizatorach i konserwantach. Poprawiają płynność sosów instant i zup. W lodach wpływają na topnienie i odczucie w ustach oraz nadają im kremowy smak pomimo zmniejszenia zawartości śmietanki.
W przemyśle spożywczym i farmaceutycznym wpływają na teksturę, formę, strukturę i konsystencję produktów płynnych i półstałych. Ich zastosowania obejmują zarówno pasty do zębów, jak i związki powlekające dla farmaceutyków. W kosmetyce służą jako regulatory lepkości i stabilizatory oraz określają reologię maści, kremów do opalania i makijażu. Ich potencjał jest daleki od wyczerpania i jest przedmiotem intensywnych badań.
Cena „prostych” pochodnych celulozy, takich jak karboksymetyloceluloza (CMC), zaczyna się od 1,50 euro/kg i wzrasta do ponad 100 euro/kg w przypadku specjalnych pochodnych celulozy w zastosowaniach farmaceutycznych. W wielu zastosowaniach etery celulozy trudno jest zastąpić produktami ropopochodnymi. Zwiększy to ich znaczenie w różnych gałęziach przemysłu. W szczególności w wielu zastosowaniach farmaceutycznych lub jako dodatki do żywności, zwłaszcza w produktach gotowych.
© Copyright by amixon GmbH